Atomic Layer Deposition (ALD) is a highly precise thin-film deposition technique, but it has several limitations that can impact its applicability in certain scenarios. These limitations include time-consuming processes, material constraints, temperature sensitivity, challenges in achieving uniform thickness and purity, and issues related to stress during cooling. Additionally, ALD relies on gas precursors, which can introduce complexities in handling and safety. Understanding these limitations is crucial for equipment and consumable purchasers to make informed decisions about when and where to use ALD.
Key Points Explained:
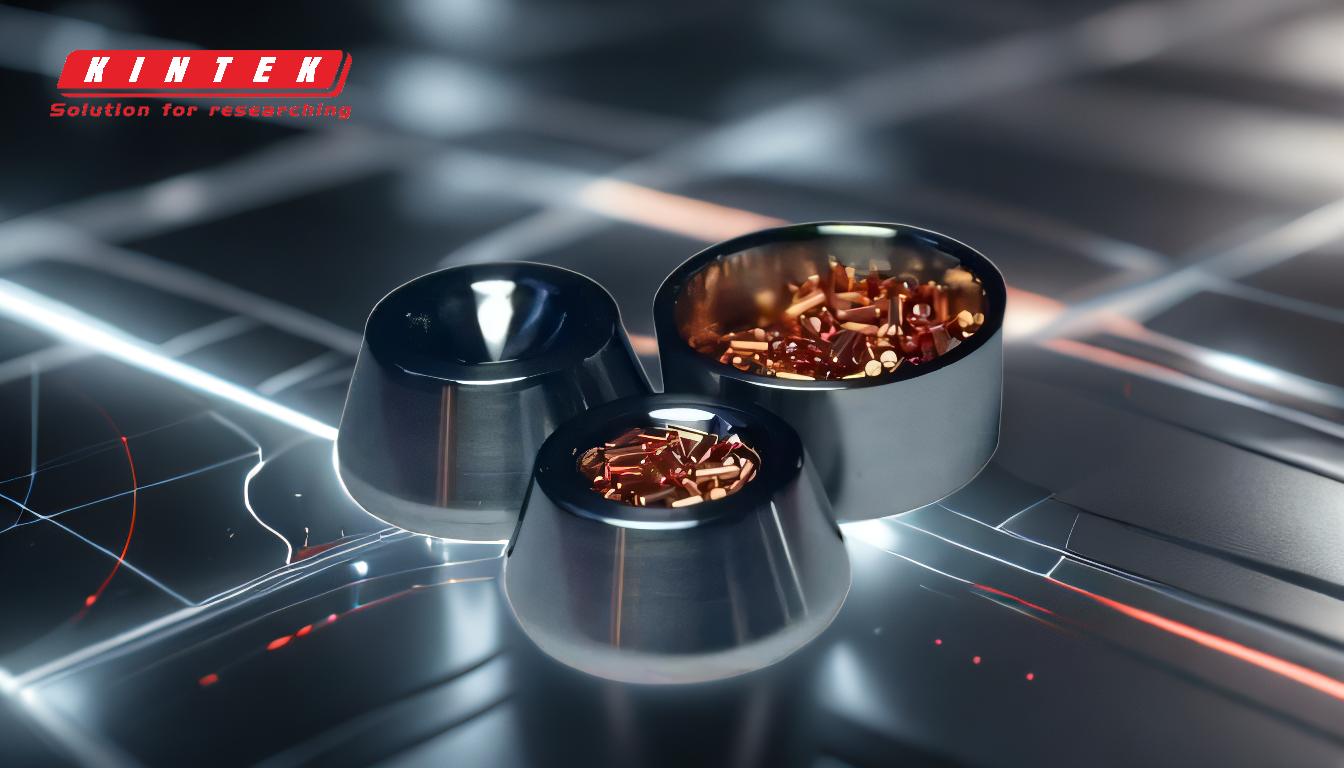
-
Time-Consuming Process:
- ALD is a sequential process that involves alternating exposure of the substrate to different precursors, separated by purge steps. This results in a slow deposition rate compared to other techniques like Chemical Vapor Deposition (CVD). For high-throughput applications, the slow deposition rate can be a significant drawback.
-
Material Constraints:
- ALD is limited in the types of materials that can be deposited. While it excels at depositing certain oxides, nitrides, and metals, it may not be suitable for all materials. This limitation arises from the need for specific gas-phase precursors that can react in a self-limiting manner.
-
Temperature Constraints:
- ALD processes often require elevated temperatures to ensure proper precursor reactivity and film quality. However, these temperatures may not be compatible with all substrate materials, particularly those that are temperature-sensitive, such as polymers or certain biological materials.
-
Uniformity and Purity Challenges:
- Achieving uniform thickness and high purity in ALD coatings can be challenging, especially on complex or three-dimensional structures. Non-uniformities can arise from issues such as incomplete precursor reactions, inadequate purging, or uneven gas flow.
-
Stress During Cooling:
- The thermal expansion mismatch between the deposited film and the substrate can lead to undesirable stresses during cooling. These stresses can cause film cracking, delamination, or other mechanical failures, particularly in multi-layer structures.
-
Precursor Handling and Safety:
- ALD relies on gas-phase precursors, which can be toxic, flammable, or explosive. Handling these precursors requires specialized equipment and safety protocols, adding to the complexity and cost of the process.
-
Cost and Scalability:
- The equipment and precursor costs for ALD can be high, making it less economical for large-scale production. Additionally, scaling up ALD processes while maintaining precision and uniformity is challenging, limiting its use in high-volume manufacturing.
-
Environmental and Health Concerns:
- The use of hazardous precursors and the generation of toxic byproducts during ALD can pose environmental and health risks. Proper disposal and handling of these materials are essential, adding to the operational complexity.
In summary, while ALD offers exceptional control over film thickness and conformality, its limitations in terms of deposition rate, material compatibility, temperature sensitivity, and safety concerns must be carefully considered. Equipment and consumable purchasers should weigh these factors against the specific requirements of their applications to determine whether ALD is the most suitable deposition technique.
Summary Table:
Limitation | Description |
---|---|
Time-Consuming Process | Slow deposition rate due to sequential precursor exposure and purge steps. |
Material Constraints | Limited to specific materials due to precursor requirements. |
Temperature Constraints | High temperatures may not suit temperature-sensitive substrates. |
Uniformity and Purity Challenges | Difficult to achieve uniform thickness and purity on complex structures. |
Stress During Cooling | Thermal expansion mismatch can cause film cracking or delamination. |
Precursor Handling and Safety | Requires specialized equipment and safety protocols for toxic, flammable gases. |
Cost and Scalability | High equipment and precursor costs; challenging to scale for large production. |
Environmental and Health Risks | Hazardous precursors and byproducts require careful handling and disposal. |
Need help deciding if ALD is right for your application? Contact our experts today for personalized guidance!