The sputtering process is a complex physical phenomenon influenced by a variety of parameters that determine the efficiency, quality, and characteristics of the deposited film. The primary parameters include the mass of the ions, the angle of incidence, the energy of the incident ions, and the properties of the target material. Additionally, factors such as chamber pressure, the type of power source (DC or RF), and the kinetic energy of emitted particles play significant roles in the process. These parameters collectively influence the sputtering yield, deposition rate, and the quality of the coating. Understanding these parameters is crucial for optimizing the sputtering process for specific applications.
Key Points Explained:
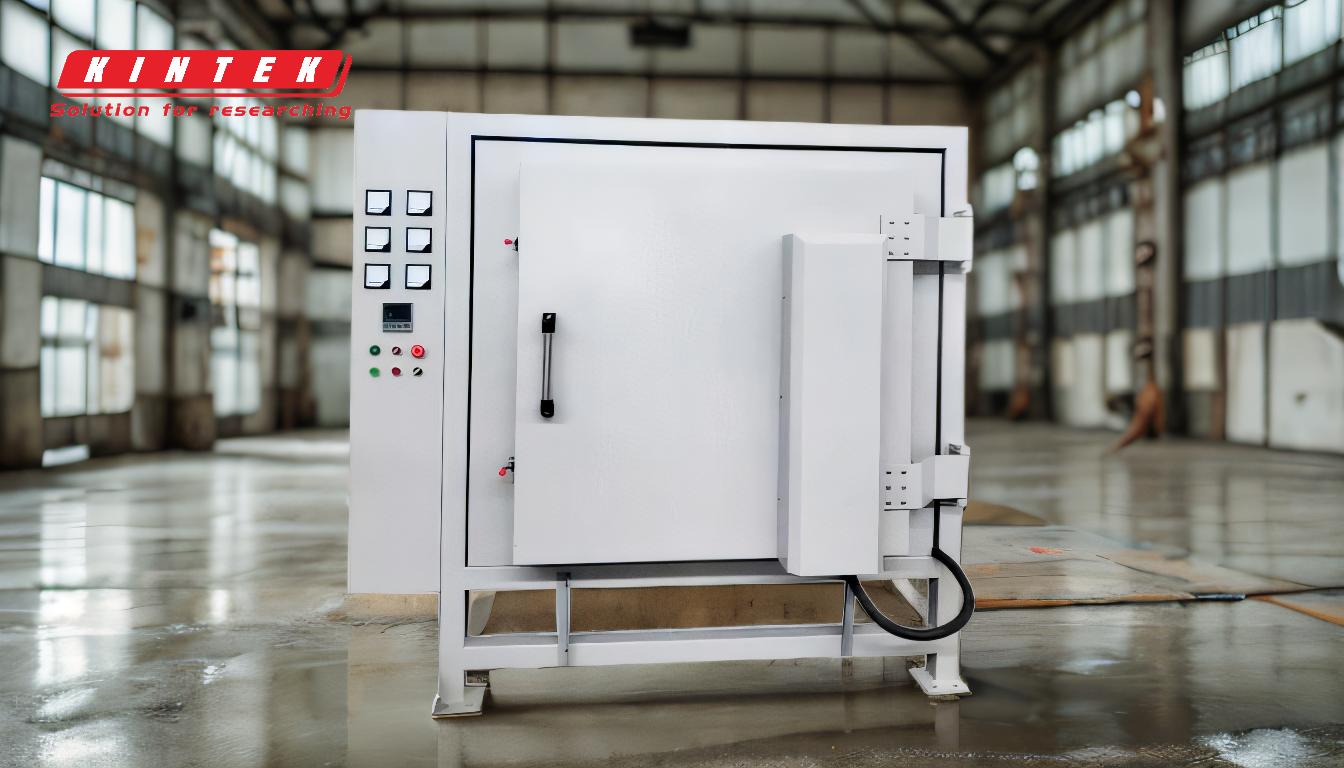
-
Mass of the Ions and Target Atoms:
- The mass of the ions and the target atoms significantly affects the sputtering yield, which is the number of target atoms ejected per incident ion.
- Heavier ions tend to transfer more momentum to the target atoms, leading to a higher sputtering yield.
- The mass ratio between the incident ions and the target atoms also plays a role; a closer mass ratio can enhance the efficiency of energy transfer, thereby increasing the sputtering yield.
-
Angle of Incidence:
- The angle at which ions strike the target surface (angle of incidence) influences the sputtering yield.
- At normal incidence (90 degrees), the sputtering yield is generally lower compared to oblique angles.
- An optimal angle of incidence (typically around 45 degrees) can maximize the sputtering yield by enhancing the momentum transfer from the ions to the target atoms.
-
Incident Ion Energy:
- The energy of the incident ions is a critical parameter that determines the sputtering yield.
- Higher ion energies generally result in a higher sputtering yield, as more energy is transferred to the target atoms, causing them to be ejected.
- However, excessively high ion energies can lead to damage to the target material and the substrate, so it is essential to find an optimal energy level.
-
Chamber Pressure:
- The pressure within the sputtering chamber affects the mean free path of the sputtered particles and the overall coverage of the deposited film.
- Lower pressures (higher vacuum) can improve the directionality of the sputtered particles, leading to better coverage and uniformity.
- However, too low a pressure can reduce the number of collisions, potentially decreasing the deposition rate.
-
Type of Power Source (DC or RF):
- The choice between DC (Direct Current) and RF (Radio Frequency) power sources affects the deposition rate, material compatibility, and cost.
- DC sputtering is typically used for conductive materials, while RF sputtering is suitable for both conductive and insulating materials.
- RF sputtering can provide better control over the deposition process, especially for insulating targets, but it is generally more expensive.
-
Kinetic Energy of Emitted Particles:
- The kinetic energy of the sputtered particles determines their direction and how they deposit on the substrate.
- Higher kinetic energy can improve the adhesion and density of the deposited film but may also lead to increased surface roughness.
- Controlling the kinetic energy is crucial for achieving the desired film properties.
-
Sputter Current and Voltage:
- The sputter current and voltage directly influence the deposition rate and the energy of the incident ions.
- Higher currents and voltages can increase the deposition rate but may also lead to overheating and damage to the target material.
- Optimizing these parameters is essential for achieving a balance between deposition rate and film quality.
-
Distance from Target to Sample:
- The distance between the target and the substrate affects the deposition rate and the uniformity of the coating.
- A shorter distance can increase the deposition rate but may lead to non-uniform coatings due to shadowing effects.
- A longer distance can improve uniformity but may reduce the deposition rate.
-
Sputter Gas:
- The choice of sputter gas (e.g., Argon, Krypton) influences the sputtering yield and the characteristics of the deposited film.
- Inert gases like Argon are commonly used due to their high sputtering yield and chemical inertness.
- The choice of gas can also affect the energy transfer and the overall efficiency of the sputtering process.
-
Target and Sample Material:
- The properties of the target material, such as its thickness and composition, directly affect the sputtering yield and the quality of the deposited film.
- The sample material also plays a role, as different materials may require different sputtering conditions to achieve optimal adhesion and film quality.
In summary, the sputtering process is governed by a complex interplay of parameters that must be carefully controlled to achieve the desired film properties. Understanding and optimizing these parameters is essential for the successful application of sputtering in various industries.
Summary Table:
Parameter | Impact on Sputtering Process |
---|---|
Mass of Ions & Target Atoms | Higher mass increases sputtering yield; closer mass ratio enhances energy transfer efficiency. |
Angle of Incidence | Optimal angle (~45°) maximizes sputtering yield by improving momentum transfer. |
Incident Ion Energy | Higher energy increases yield but excessive energy can damage the target or substrate. |
Chamber Pressure | Lower pressure improves particle directionality but too low can reduce deposition rate. |
Power Source (DC/RF) | DC for conductive materials; RF for conductive and insulating materials (better control). |
Kinetic Energy of Particles | Higher energy improves adhesion but may increase surface roughness. |
Sputter Current & Voltage | Higher values increase deposition rate but risk overheating and target damage. |
Target-to-Sample Distance | Shorter distance increases rate; longer distance improves coating uniformity. |
Sputter Gas | Inert gases like Argon are preferred for high yield and chemical inertness. |
Target & Sample Material | Material properties affect yield, adhesion, and film quality; requires tailored conditions. |
Need help optimizing your sputtering process? Contact our experts today for tailored solutions!