Diamond-like carbon (DLC) coatings are primarily composed of carbon atoms arranged in a combination of sp3 (diamond-like) and sp2 (graphite-like) bonds. These coatings are known for their high hardness, low coefficient of friction, and excellent performance in corrosive environments. The process of creating DLC coatings involves the use of hydrocarbons, which are compounds of hydrogen and carbon. These elements are introduced into a plasma environment, where they recombine on the surface of the substrate to form the coating. The unique properties of DLC coatings make them ideal for applications requiring enhanced sliding properties and durability.
Key Points Explained:
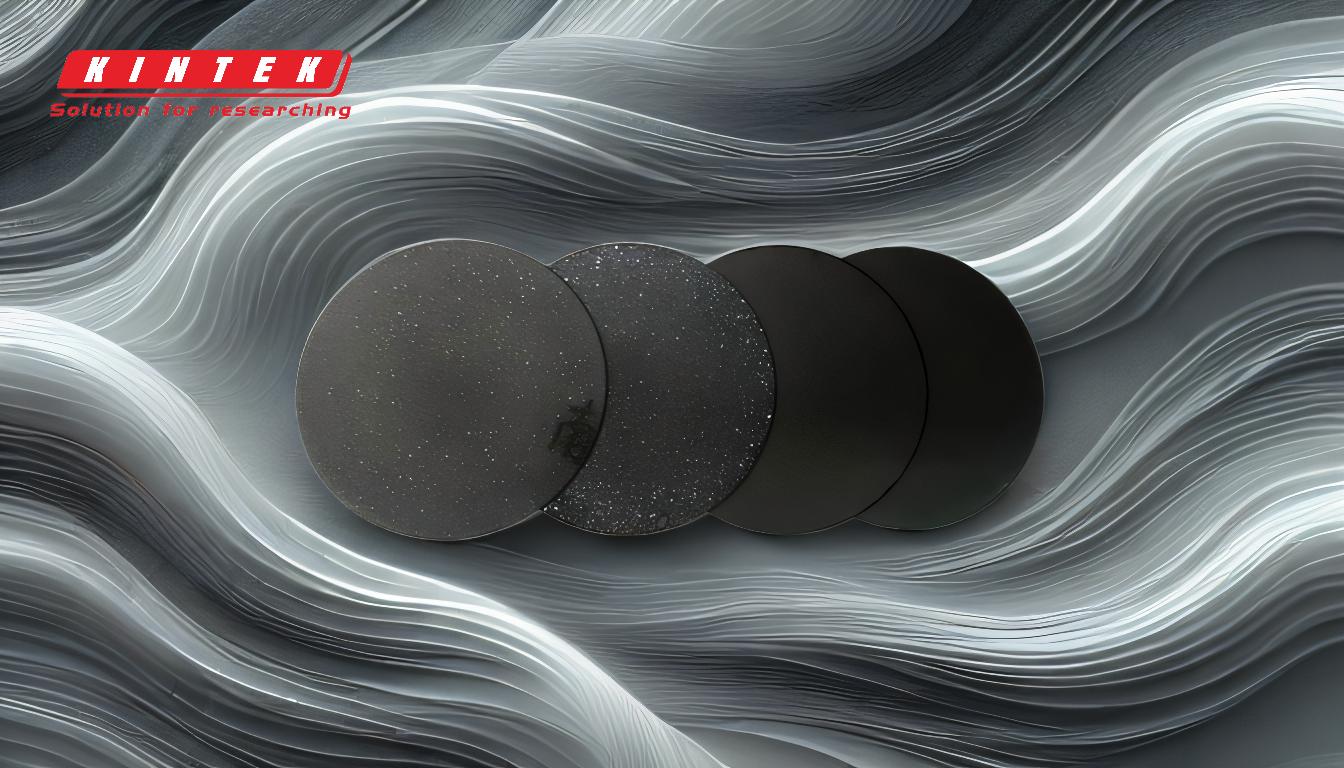
-
Composition of DLC Coatings:
- Carbon Bonds: DLC coatings are characterized by the presence of both sp3 (diamond-like) and sp2 (graphite-like) carbon bonds. The sp3 bonds contribute to the hardness and durability of the coating, while the sp2 bonds provide a lower coefficient of friction, making the coating suitable for sliding applications.
- Hydrocarbons: The process of creating DLC coatings involves the use of hydrocarbons, which are compounds consisting of hydrogen and carbon. These hydrocarbons are introduced into a plasma environment, where they break down and recombine on the substrate surface to form the coating.
-
Properties of DLC Coatings:
- High Hardness: The sp3 carbon bonds in DLC coatings give them a hardness that is comparable to that of diamond. This makes DLC coatings highly resistant to wear and abrasion.
- Low Coefficient of Friction: The presence of sp2 carbon bonds in DLC coatings results in a low coefficient of friction, which is beneficial for applications involving sliding or moving parts.
- Corrosion Resistance: DLC coatings exhibit excellent performance in corrosive environments, making them suitable for use in industries where components are exposed to harsh conditions.
-
Application of DLC Coatings:
- Substrates: DLC coatings can be applied to a variety of substrates, including metals (such as stainless steel and aluminum), plastics, glass, and ceramics. The versatility of DLC coatings allows them to be used in a wide range of industries.
- Industries: Due to their unique properties, DLC coatings are commonly used in industries such as automotive, aerospace, and electronics. They are particularly valuable in applications where components are subjected to high wear and friction, such as engine parts, cutting tools, and electronic components.
-
Comparison with Other Coating Materials:
- PVD Coatings: While PVD (Physical Vapor Deposition) coatings can include a variety of materials such as titanium, zirconium, and gold, DLC coatings are specifically known for their carbon-based composition and unique properties. PVD coatings are often used for decorative purposes or to enhance the surface properties of materials, whereas DLC coatings are primarily valued for their mechanical properties.
- CVD Coatings: CVD (Chemical Vapor Deposition) coatings can include materials such as silicon compounds, carbon, and fluorocarbons. While CVD coatings can be tailored for specific performance goals, DLC coatings are distinct in their combination of high hardness and low friction, making them particularly suitable for demanding mechanical applications.
-
Future Trends and Enhancements:
- Doping: The properties of DLC coatings can be further enhanced by doping the surface with other materials. For example, adding silicon or other elements can functionalize the coating for specific performance goals, such as increased wear resistance or improved thermal stability.
- Advanced Applications: As industries continue to demand higher performance from materials, DLC coatings are likely to see increased use in advanced applications, such as in the development of next-generation electronic devices, high-performance automotive components, and aerospace systems.
In summary, DLC coatings are primarily composed of carbon atoms arranged in a combination of sp3 and sp2 bonds, with the addition of hydrocarbons during the coating process. These coatings offer a unique combination of high hardness, low friction, and corrosion resistance, making them ideal for a wide range of industrial applications. The ability to further enhance DLC coatings through doping and other techniques ensures that they will continue to play a critical role in the development of advanced materials and components.
Summary Table:
Aspect | Details |
---|---|
Composition | Carbon atoms with sp3 (diamond-like) and sp2 (graphite-like) bonds. |
Properties | High hardness, low friction, and corrosion resistance. |
Applications | Automotive, aerospace, electronics, and more. |
Substrates | Metals, plastics, glass, and ceramics. |
Future Enhancements | Doping with silicon or other elements for improved performance. |
Learn how DLC coatings can enhance your components—contact us today!