The ball mill process is influenced by several key parameters that determine its efficiency and output quality. These parameters include the drum dimensions (diameter and length), the ratio of drum diameter to length (L:D ratio), the physical and chemical properties of the feed material, ball characteristics (size, density, and filling ratio), armor surface shape, rotation speed, milling fineness, and the timely removal of ground product. Additionally, factors such as residence time, feed rate, and material hardness play a significant role in the grinding performance. Understanding and optimizing these parameters is crucial for achieving desired milling outcomes, whether for fine or coarse particle production.
Key Points Explained:
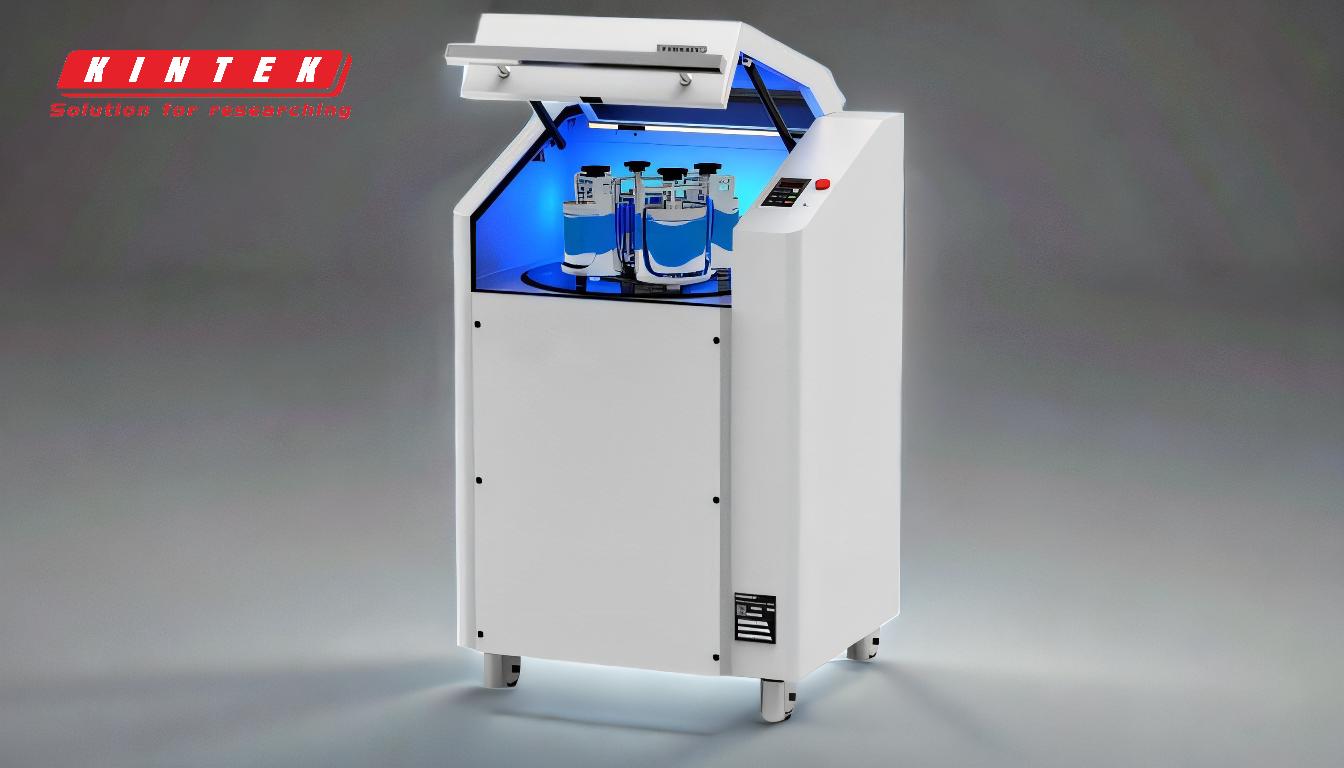
-
Drum Dimensions and L:D Ratio:
- Drum Diameter: The diameter of the drum directly affects the grinding efficiency. Larger diameters allow for greater impact and grinding action.
- Length-to-Diameter Ratio (L:D Ratio): The optimal L:D ratio for ball mills is typically between 1.56 and 1.64. This ratio ensures efficient grinding by balancing the grinding action and material residence time.
-
Physical-Chemical Properties of Feed Material:
- The nature of the material being ground, including its hardness, density, and chemical composition, significantly impacts the grinding process. Harder materials may require longer grinding times or specific ball sizes to achieve the desired fineness.
-
Ball Characteristics:
- Ball Size: Smaller balls are generally used for finer grinding, while larger balls are suitable for coarser grinding.
- Ball Density: Higher density balls provide more impact force, which can be beneficial for harder materials.
- Ball Filling Ratio: This refers to the percentage of the mill volume filled with grinding balls. An optimal filling ratio ensures efficient grinding without overloading the mill.
-
Armor Surface Shape:
- The shape of the mill's internal armor (lining) affects the movement of the balls and the material. Smooth linings may reduce wear but could also decrease grinding efficiency, whereas textured linings can enhance grinding action.
-
Rotation Speed:
- The speed at which the mill rotates is critical. Too slow, and the balls may not cascade effectively; too fast, and the balls may centrifuge, reducing grinding efficiency. The optimal speed depends on the mill's diameter and the desired grinding action.
-
Milling Fineness:
- The desired particle size of the ground product influences the choice of parameters. Finer particles generally require longer grinding times, smaller balls, and possibly higher rotation speeds.
-
Timely Removal of Ground Product:
- Efficient removal of the ground product prevents over-grinding and ensures consistent product quality. This can be managed through proper discharge mechanisms and control of the feed rate.
-
Residence Time:
- The time the material spends in the mill chamber affects the degree of grinding. Longer residence times can lead to finer particles but may also increase energy consumption.
-
Feed Rate and Level:
- The rate at which material is fed into the mill and the level of material in the vessel influence the grinding efficiency. Overloading the mill can reduce efficiency, while underloading may lead to insufficient grinding.
-
Material Hardness:
- Harder materials require more energy to grind and may necessitate specific adjustments in ball size, density, and rotation speed to achieve the desired fineness.
-
Grinding Medium and Filling Ratio:
- The type and size of the grinding medium (balls) and the filling ratio (percentage of mill volume filled with grinding medium) are crucial for optimizing the grinding process. The right combination ensures effective grinding without unnecessary energy expenditure.
By carefully considering and optimizing these parameters, operators can enhance the performance of ball mills, achieving the desired particle size and quality while minimizing energy consumption and wear on the equipment.
Summary Table:
Parameter | Impact on Grinding Process |
---|---|
Drum Dimensions (L:D Ratio) | Optimal L:D ratio (1.56–1.64) ensures efficient grinding by balancing action and residence time. |
Ball Size & Density | Smaller balls for fine grinding; higher density for harder materials. |
Rotation Speed | Critical for ball cascade; too slow or fast reduces efficiency. |
Material Hardness | Harder materials require more energy and specific ball adjustments. |
Feed Rate & Level | Overloading reduces efficiency; underloading leads to insufficient grinding. |
Residence Time | Longer times produce finer particles but increase energy consumption. |
Optimize your ball mill performance today—contact our experts for tailored solutions!