A sieve shaker is a critical piece of equipment used in particle analysis, material separation, and sample size reduction. It automates the sieving process, replacing manual hand sieving to improve efficiency, accuracy, and consistency. The primary components of a sieve shaker include the sieve, screen frame, skirt, power unit, cradle, base, and supporting mechanisms such as vertical rods, retaining rings, and sieve holders. These components work together to ensure precise particle size distribution and classification, making the sieve shaker indispensable in quality assurance and quality control processes.
Key Points Explained:
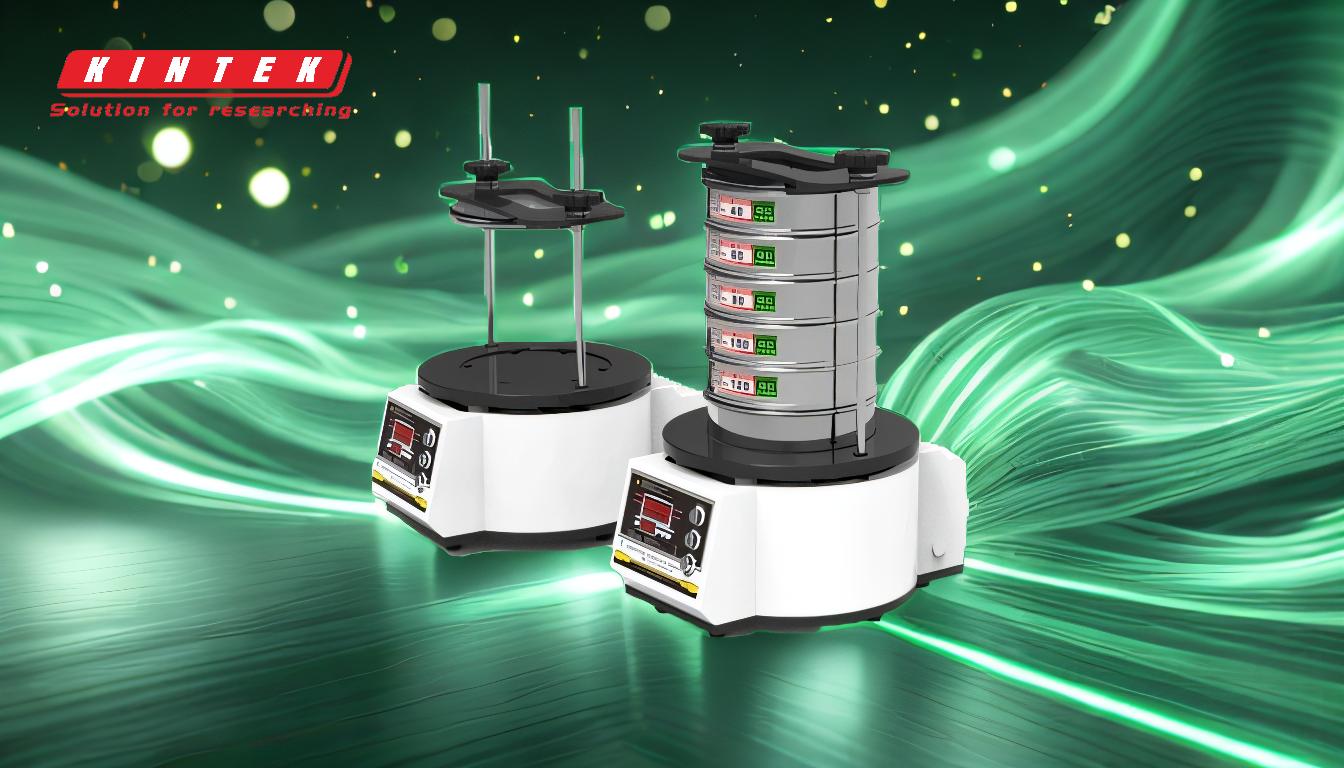
-
Sieve
- The sieve is the core component of a sieve shaker, typically made of stainless steel woven wire mesh.
- It is designed to separate particles based on size, with apertures ranging from 20 µm to 63 mm.
- Sieves are stacked in order from the largest aperture at the top to the smallest at the bottom to facilitate efficient particle separation.
-
Screen Frame
- The screen frame holds the sieve mesh in place and is usually constructed from durable materials like stainless steel or brass.
- It ensures the sieve remains stable during the shaking process, preventing deformation or damage to the mesh.
- The frame's design allows for easy stacking and secure attachment to the sieve shaker.
-
Skirt
- The skirt is a structural component that enables sieves to stack securely without tipping over during operation.
- It ensures proper alignment of the sieves, maintaining the integrity of the particle separation process.
- The skirt is typically made of the same materials as the screen frame for durability and consistency.
-
Power Unit
- The power unit is the driving force behind the sieve shaker, providing the necessary energy to agitate the sieves.
- It can be adjusted to control the intensity and frequency of the shaking motion, accommodating different materials and particle sizes.
- The power unit is designed for consistent performance, ensuring repeatable results in particle analysis.
-
Cradle
- The cradle holds the stack of sieves in place during operation.
- It consists of a platform fastened to vertical supporting rods, which are shock-mounted to a horizontal support.
- The cradle's design allows for smooth and controlled movement, minimizing vibrations and ensuring accurate particle separation.
-
Base
- The base provides stability to the sieve shaker, preventing it from moving or tipping during operation.
- It is typically made of heavy-duty materials to absorb vibrations and maintain balance.
- The base also houses the power unit and supports the cradle, ensuring all components work in harmony.
-
Supporting Mechanisms
- Vertical rods, retaining rings, and sieve holders are critical for securing the sieves in place.
- The vertical rods support the cradle and are shock-mounted to reduce vibrations.
- Retaining rings and sieve holders ensure the top bar remains inflexible, maintaining consistent pressure on the sieves for accurate results.
-
Functionality and Applications
- A sieve shaker automates the agitation of particles, replacing manual sieving for increased efficiency and accuracy.
- It is used for dry and wet sieving, measuring particle size distribution and classifying materials up to 2 kg.
- Applications include quality assurance, quality control, and particle analysis in industries such as pharmaceuticals, construction, and food processing.
By understanding these components and their roles, equipment and consumable purchasers can make informed decisions when selecting a sieve shaker that meets their specific needs. The combination of durability, precision, and ease of use makes the sieve shaker a vital tool in particle analysis and material separation.
Summary Table:
Component | Function |
---|---|
Sieve | Separates particles by size using stainless steel mesh with apertures 20 µm–63 mm. |
Screen Frame | Holds sieve mesh securely, ensuring stability during operation. |
Skirt | Enables secure stacking of sieves and maintains alignment. |
Power Unit | Drives the shaking motion with adjustable intensity and frequency. |
Cradle | Holds sieve stack in place, minimizing vibrations for accurate results. |
Base | Provides stability and houses the power unit and cradle. |
Supporting Mechanisms | Secures sieves with vertical rods, retaining rings, and sieve holders. |
Ready to enhance your particle analysis process? Contact us today to find the perfect sieve shaker for your needs!