Biomass boilers are an eco-friendly alternative to traditional fossil fuel boilers, but they come with certain risks that need to be carefully managed. These risks include fire hazards, emissions of particulate matter, potential health impacts, and operational challenges. Proper installation, maintenance, and adherence to safety standards are crucial to mitigate these risks. Additionally, the efficiency and environmental benefits of biomass boilers can be compromised if not operated correctly. Understanding these risks is essential for anyone considering the installation or use of a biomass boiler.
Key Points Explained:
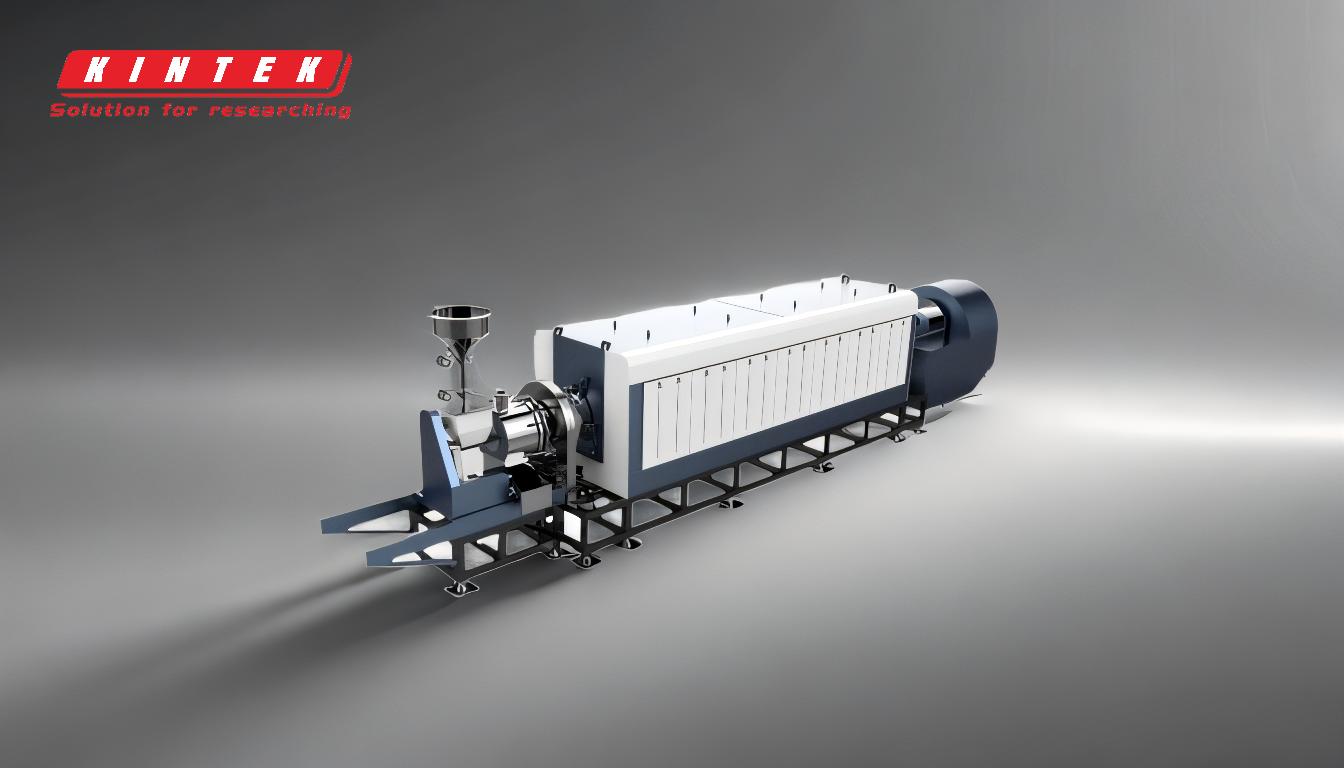
-
Fire Hazards:
- Biomass boilers use organic materials like wood pellets, chips, or logs as fuel, which are highly combustible.
- Improper storage of biomass fuel can lead to spontaneous combustion, especially if the fuel is damp or stored in large quantities.
- Regular cleaning of the boiler and fuel storage area is necessary to prevent the buildup of dust and debris, which can ignite easily.
-
Emissions and Air Quality:
- Biomass boilers emit particulate matter (PM), which can contribute to air pollution and respiratory issues.
- The type of fuel used and the efficiency of the boiler significantly impact the level of emissions. Poor-quality fuel or inefficient combustion can lead to higher emissions of harmful pollutants like carbon monoxide (CO) and nitrogen oxides (NOx).
- Proper ventilation and the use of high-quality, low-moisture fuel can help reduce emissions.
-
Health Risks:
- Exposure to particulate matter and other pollutants from biomass boilers can pose health risks, particularly for individuals with pre-existing respiratory conditions.
- Workers involved in the handling and maintenance of biomass boilers may be at higher risk of exposure to harmful substances.
- Implementing safety measures such as wearing protective equipment and ensuring proper ventilation can mitigate these health risks.
-
Operational Challenges:
- Biomass boilers require more frequent maintenance compared to traditional boilers. This includes regular cleaning of the combustion chamber, ash removal, and inspection of fuel feed systems.
- The efficiency of a biomass boiler can be affected by the quality of the fuel, the design of the boiler, and the skill of the operator. Inefficient operation can lead to higher fuel consumption and increased emissions.
- Ensuring that the boiler is correctly sized for the heating demand is crucial to avoid operational inefficiencies.
-
Regulatory Compliance:
- Biomass boilers are subject to various regulations and standards aimed at minimizing their environmental and health impacts. Non-compliance can result in legal penalties and increased operational costs.
- It is important to stay informed about local regulations regarding emissions, fuel quality, and boiler operation.
- Regular inspections and adherence to maintenance schedules are essential to ensure compliance with regulatory requirements.
-
Environmental Impact:
- While biomass boilers are considered a renewable energy source, their environmental benefits can be offset if the biomass fuel is not sourced sustainably.
- The carbon neutrality of biomass fuel depends on the balance between carbon emissions during combustion and carbon sequestration during the growth of the biomass. Unsustainable harvesting practices can disrupt this balance.
- Choosing certified sustainable biomass fuel and ensuring efficient boiler operation can help maximize the environmental benefits.
In conclusion, while biomass boilers offer significant environmental advantages, they come with inherent risks that require careful management. By understanding and addressing these risks, users can ensure the safe and efficient operation of biomass boilers, maximizing their benefits while minimizing potential drawbacks.
Summary Table:
Risk Category | Key Risks | Mitigation Strategies |
---|---|---|
Fire Hazards | Combustible fuel, improper storage, dust buildup | Regular cleaning, proper fuel storage, and maintenance |
Emissions & Air Quality | Particulate matter, CO, NOx emissions | Use high-quality fuel, ensure proper ventilation, and optimize combustion efficiency |
Health Risks | Respiratory issues, exposure to pollutants | Wear protective equipment, ensure proper ventilation, and follow safety guidelines |
Operational Challenges | Frequent maintenance, inefficiency, incorrect sizing | Regular inspections, proper training, and correct boiler sizing |
Regulatory Compliance | Non-compliance with emissions and safety standards | Stay informed about regulations, conduct regular inspections, and adhere to maintenance |
Environmental Impact | Unsustainable fuel sourcing, carbon neutrality disruption | Use certified sustainable fuel, ensure efficient operation, and monitor carbon balance |
Ensure safe and efficient operation of your biomass boiler—contact our experts today for tailored advice!