Pyrolysis reactors are essential equipment in the thermal decomposition of organic materials in the absence of oxygen, producing biochar, bio-oil, and syngas. The choice of reactor type depends on factors such as heat transfer efficiency, residence time, processing capacity, and the nature of the feedstock. Common types include fluidized-bed reactors, fixed-bed reactors, rotary kiln reactors, and ablative reactors, each offering distinct advantages for specific industrial applications. Understanding the characteristics of these reactors is crucial for optimizing pyrolysis processes and achieving desired outputs.
Key Points Explained:
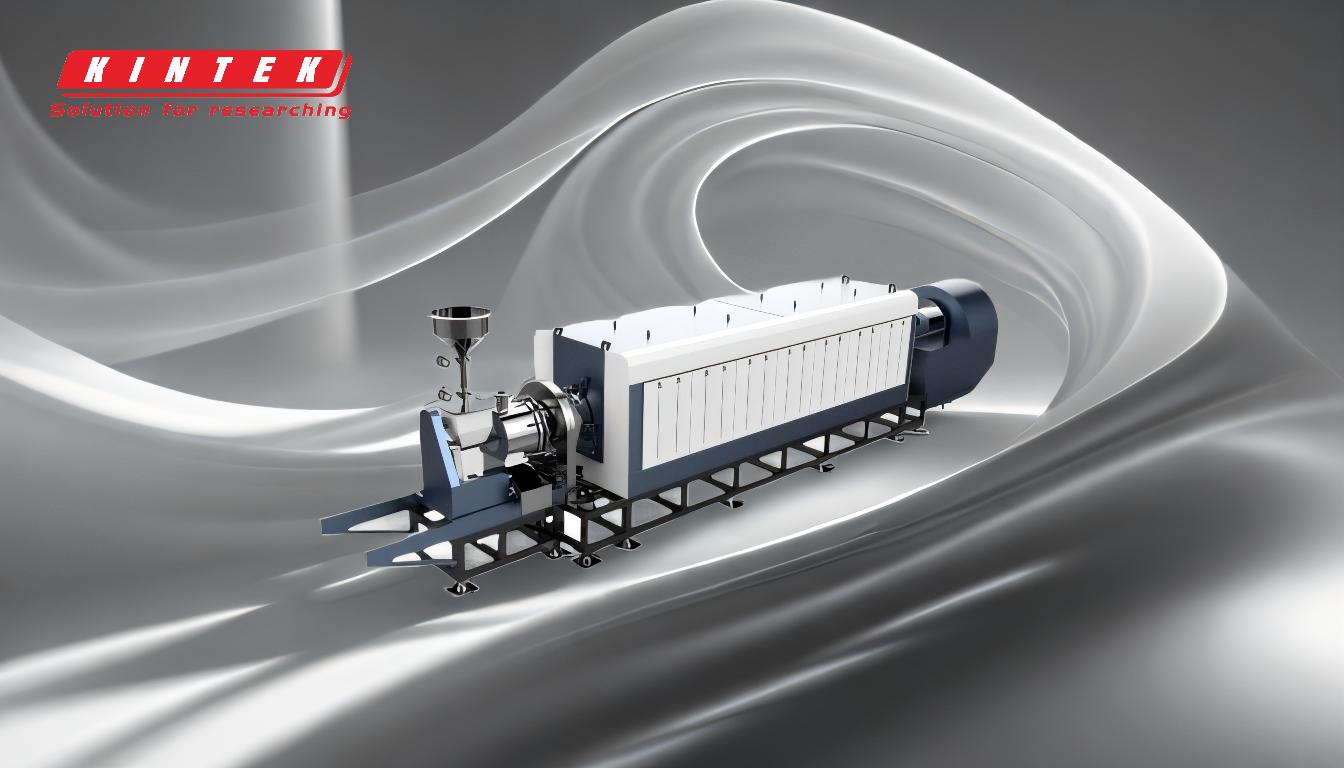
-
Fluidized-Bed Reactors
- Description: Fluidized-bed reactors suspend feedstock particles in a stream of gas, creating a fluid-like state that ensures uniform heat transfer and efficient mixing.
-
Types:
- Bubbling Fluidized Bed: Ideal for moderate-temperature pyrolysis, offering good heat transfer and control over residence time.
- Circulating Fluidized Bed: Suitable for large-scale operations, providing high heat transfer rates and continuous processing.
- Advantages: High heat transfer efficiency, scalability, and adaptability to various feedstocks.
- Applications: Biomass pyrolysis, waste-to-energy systems.
-
Fixed-Bed Reactors
- Description: Fixed-bed reactors consist of a stationary bed of feedstock through which a gas or liquid flows, facilitating pyrolysis.
- Advantages: Simple design, low operating costs, and suitability for small-scale or batch processes.
- Limitations: Limited heat transfer efficiency and challenges in scaling up.
- Applications: Laboratory-scale pyrolysis, niche industrial applications.
-
Rotary Kiln Reactors
- Description: Rotary kiln reactors use indirect heating to thermally decompose materials as they rotate within a cylindrical chamber.
- Advantages: Reduced risk of contamination, uniform heating, and ability to handle a wide range of feedstocks.
- Applications: Waste recycling, pyrolysis of plastics and tires.
-
Ablative Reactors
- Description: Ablative reactors use mechanical pressure and heat to rapidly decompose feedstock on a hot surface.
- Advantages: High heating rates, minimal residence time, and suitability for high-viscosity feedstocks.
- Applications: Fast pyrolysis for bio-oil production.
-
Auger Reactors
- Description: Auger reactors use a screw mechanism to transport and heat feedstock through a heated barrel.
- Advantages: Compact design, continuous operation, and good control over residence time.
- Applications: Biomass and plastic pyrolysis.
-
Vacuum Reactors
- Description: Vacuum reactors operate under reduced pressure, lowering the boiling point of pyrolysis products and minimizing secondary reactions.
- Advantages: High-quality bio-oil production, reduced tar formation.
- Applications: High-value chemical production from biomass.
-
Other Reactor Types
- Tubular Reactors: Designed for continuous processing with precise temperature control.
- Heinz Retort: A specialized batch reactor for high-temperature pyrolysis.
- Wire Mesh Reactors: Used for rapid pyrolysis studies in research settings.
- Batch and Semi-Batch Reactors: Suitable for small-scale or intermittent operations.
Each reactor type has unique characteristics that make it suitable for specific applications. For example, fluidized-bed reactors are ideal for large-scale biomass pyrolysis, while rotary kiln reactors excel in waste recycling. Ablative reactors are preferred for fast pyrolysis, and vacuum reactors are used for high-quality bio-oil production. Understanding these differences is critical for selecting the right reactor for a given industrial process.
Summary Table:
Reactor Type | Key Advantages | Applications |
---|---|---|
Fluidized-Bed Reactors | High heat transfer efficiency, scalability, adaptability to various feedstocks | Biomass pyrolysis, waste-to-energy systems |
Fixed-Bed Reactors | Simple design, low operating costs, suitable for small-scale or batch processes | Laboratory-scale pyrolysis, niche industrial applications |
Rotary Kiln Reactors | Reduced contamination, uniform heating, handles a wide range of feedstocks | Waste recycling, pyrolysis of plastics and tires |
Ablative Reactors | High heating rates, minimal residence time, suitable for high-viscosity feedstocks | Fast pyrolysis for bio-oil production |
Auger Reactors | Compact design, continuous operation, good control over residence time | Biomass and plastic pyrolysis |
Vacuum Reactors | High-quality bio-oil production, reduced tar formation | High-value chemical production from biomass |
Other Reactor Types | Specialized designs for continuous processing, batch operations, or research | Tubular reactors, Heinz Retort, wire mesh reactors, batch and semi-batch reactors |
Need help selecting the right pyrolysis reactor for your application? Contact our experts today!