The size and shape of tablets produced by a tablet press are primarily defined by the punches and dies. These components are critical in determining the final product's dimensions and form. Punches and dies are subject to wear and tear due to the high-pressure environment in which they operate, necessitating periodic replacement to maintain the precision and quality of the tablets. Understanding the role and maintenance of these components is essential for ensuring consistent tablet production.
Key Points Explained:
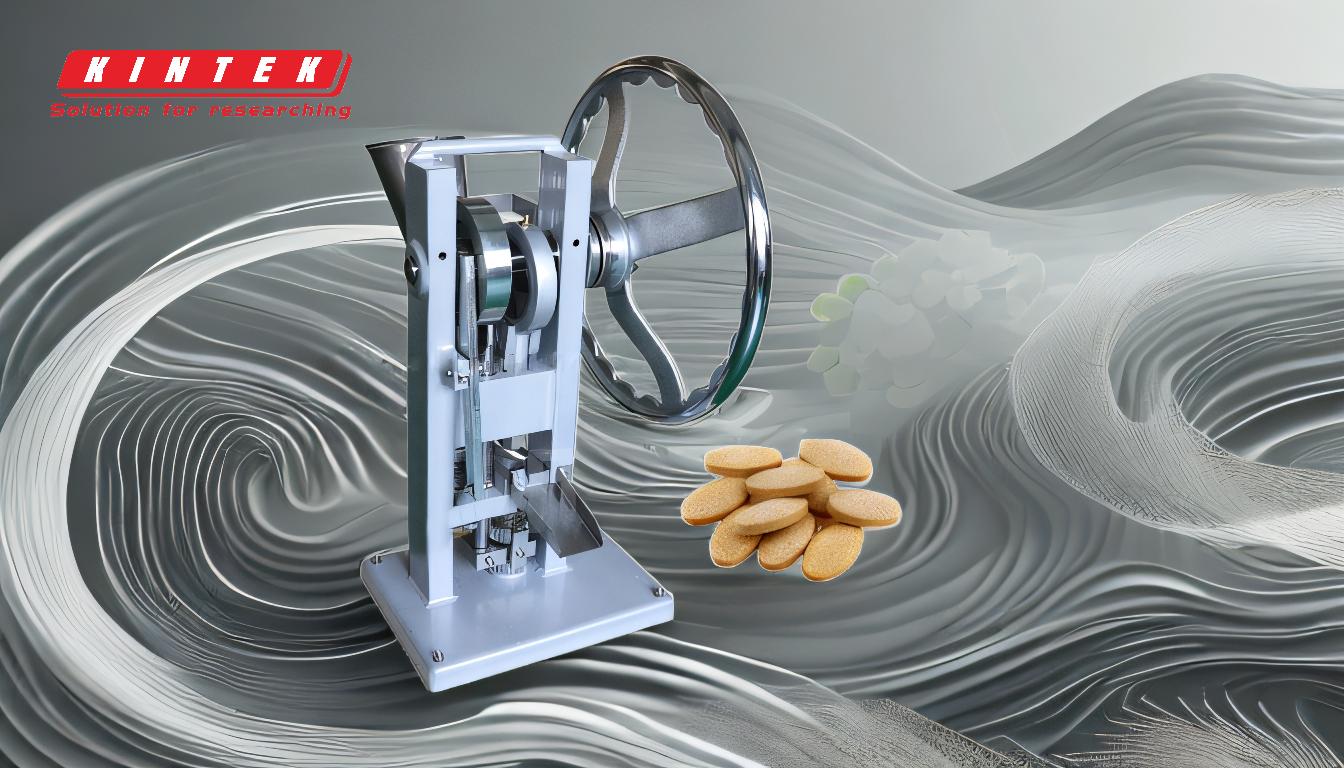
-
Punches and Dies: The Core Components
- Punches: These are the tools that apply pressure to the powder or granulate material to form the tablet. They come in pairs (upper and lower punches) and are designed to fit into the die cavity. The shape of the punch tips determines the shape of the tablet (e.g., round, oval, capsule-shaped).
- Dies: The die is a hollow cavity where the powder or granulate material is compressed by the punches. The size of the die cavity directly influences the diameter and thickness of the tablet. Dies are typically made from high-strength materials to withstand the compression forces.
-
Determining Tablet Size and Shape
- Tablet Size: The size of the tablet is primarily determined by the die cavity's dimensions. The diameter and depth of the die cavity set the upper limits for the tablet's dimensions. Adjustments to the die cavity can be made to produce tablets of different sizes.
- Tablet Shape: The shape of the tablet is defined by the design of the punch tips. Different punch tip configurations (flat, concave, convex, etc.) can produce tablets with various shapes and surface profiles. Custom punch designs can also be created to produce unique tablet shapes.
-
Wear and Tear on Punches and Dies
- Material Wear: Due to the high-pressure environment, punches and dies are subject to wear over time. This wear can lead to changes in the tablet's dimensions and shape, affecting the overall quality and consistency of the product.
- Maintenance and Replacement: Regular inspection and maintenance of punches and dies are necessary to ensure they remain within acceptable tolerances. Worn-out components should be replaced promptly to avoid defects in the tablets.
-
Impact on Tablet Quality
- Consistency: Properly maintained punches and dies ensure that each tablet produced is consistent in size, shape, and weight. This consistency is crucial for meeting regulatory standards and ensuring the efficacy of the medication.
- Defects: Worn or damaged punches and dies can lead to defects such as capping, lamination, or uneven tablet thickness. These defects can affect the tablet's appearance, dissolution rate, and overall performance.
-
Customization and Flexibility
- Custom Tooling: Tablet presses can be equipped with custom punches and dies to produce tablets with unique shapes and sizes. This flexibility allows manufacturers to create branded or specialized products.
- Interchangeability: Many tablet presses are designed to allow for easy interchangeability of punches and dies, enabling quick changes between different tablet sizes and shapes without significant downtime.
In summary, the punches and dies are the primary components of a tablet press that define the size and shape of the tablets. Their design, maintenance, and replacement are critical factors in ensuring the quality and consistency of the tablets produced. Regular inspection and timely replacement of these components are essential for maintaining the precision and reliability of the tablet press.
Summary Table:
Component | Role | Impact on Tablets |
---|---|---|
Punches | Apply pressure to form tablets; upper and lower punches shape the tablet. | Determines tablet shape (e.g., round, oval). |
Dies | Hollow cavity where material is compressed; defines tablet dimensions. | Influences tablet diameter and thickness. |
Wear and Tear | High-pressure operation causes wear, affecting tablet consistency. | Requires regular maintenance and replacement to avoid defects. |
Customization | Custom punches and dies enable unique tablet shapes and sizes. | Allows for branded or specialized tablet production. |
**Interchangeability | Easy swapping of punches and dies for different tablet designs. | Reduces downtime and enhances production flexibility. |
Ensure your tablet production meets the highest standards—contact our experts today for tailored solutions!