A sputter coater is a specialized device used primarily in scanning electron microscopy (SEM) to prepare non-conductive samples for high-resolution imaging. It works by depositing a thin layer of conductive material, such as gold or platinum, onto the sample surface. This coating enhances electrical conductivity, reduces heat buildup, and increases secondary electron emission, which improves image quality and resolution. Sputter coating involves bombarding a target material with high-energy ions, ejecting atoms from the target, and depositing them onto the sample. Key parameters like sputter current, voltage, vacuum pressure, and target-sample distance influence the coating process. This technique is essential for SEM analysis of materials that would otherwise be difficult to image due to their non-conductive nature.
Key Points Explained:
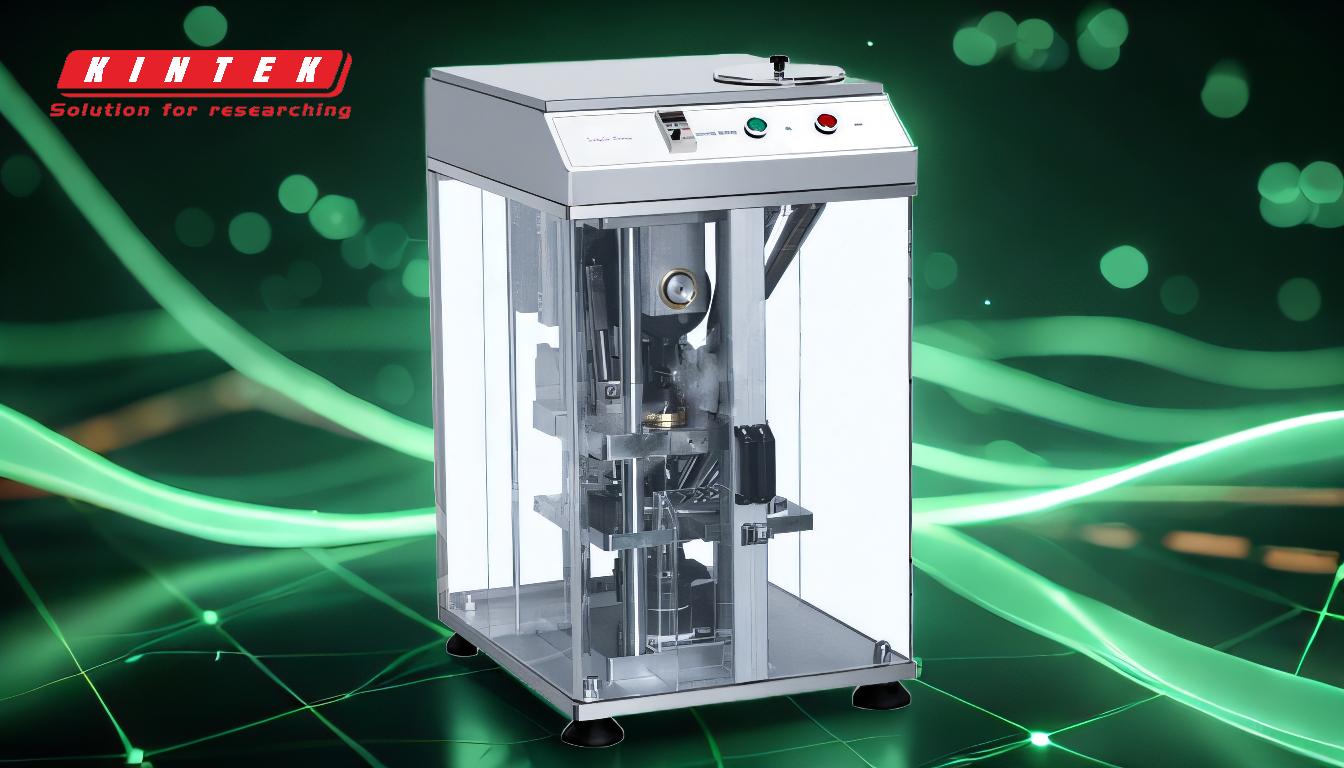
-
Purpose of a Sputter Coater:
- A sputter coater is used to apply a thin, conductive layer of metal (e.g., gold or platinum) onto non-conductive samples. This is crucial for SEM imaging, as non-conductive materials can accumulate charge under the electron beam, leading to poor image quality or damage to the sample.
- The coating improves electrical conductivity, dissipates heat, and enhances secondary electron emission, which is critical for high-resolution imaging.
-
How Sputter Coating Works:
- The process involves bombarding a solid metal target (e.g., gold) with high-energy ions in a vacuum chamber. This bombardment ejects atoms from the target, which then deposit onto the sample surface.
- The ejected atoms form a fine spray of microscopic particles, creating a uniform conductive layer on the sample.
-
Key Parameters in Sputter Coating:
- Sputter Current and Voltage: These control the energy and rate of ion bombardment, affecting the deposition rate and coating quality.
- Vacuum Pressure: A controlled vacuum environment is necessary to ensure proper ion movement and deposition.
- Distance from Target to Sample: This influences the uniformity and thickness of the coating.
- Sputter Gas: Typically argon, it ionizes to create the high-energy particles needed for sputtering.
- Target Material and Thickness: The choice of metal (e.g., gold, platinum) and its thickness determine the coating's properties.
- Sample Material: Different materials may require adjustments in coating parameters to achieve optimal results.
-
Advantages of Sputter Coating for SEM:
- Enables imaging of non-conductive samples at higher voltages, leading to better resolution.
- Provides a conductive path to prevent charge buildup and heat damage.
- Increases secondary electron yield, improving the signal-to-noise ratio and image clarity.
- Suitable for high-magnification applications, such as those requiring up to 100,000x magnification.
-
Applications:
- Primarily used in SEM sample preparation for materials like polymers, ceramics, and biological specimens.
- Also applicable in other fields requiring thin film deposition, such as electronics and optics.
-
Heat Management:
- The sputtering process generates significant heat, which is managed through specialized chilling systems to prevent sample damage and ensure consistent coating quality.
By understanding these key points, users can optimize the sputter coating process for their specific applications, ensuring high-quality results in SEM imaging and other related fields.
Summary Table:
Aspect | Details |
---|---|
Purpose | Applies conductive layers to non-conductive samples for SEM imaging. |
Process | Bombards metal targets with ions to deposit atoms onto samples. |
Key Parameters | Sputter current, voltage, vacuum pressure, target-sample distance, etc. |
Advantages | Improves conductivity, reduces heat, enhances image clarity, and resolution. |
Applications | SEM sample prep, electronics, optics, and more. |
Heat Management | Uses chilling systems to prevent sample damage. |
Optimize your SEM imaging with precision sputter coating—contact our experts today!