The principle of a ball mill depends on a combination of mechanical and operational factors that work together to grind materials into fine particles. The key principles include impact and attrition, where heavy balls inside the mill collide with the material to break it down. The efficiency of the grinding process is influenced by factors such as drum dimensions, rotation speed, ball size and density, material properties, and the filling ratio of the mill. Achieving the critical speed ensures the balls rotate along the inner walls, effectively grinding the material. Additionally, factors like residence time, feed rate, and the nature of the grinding material play a significant role in determining the degree of milling.
Key Points Explained:
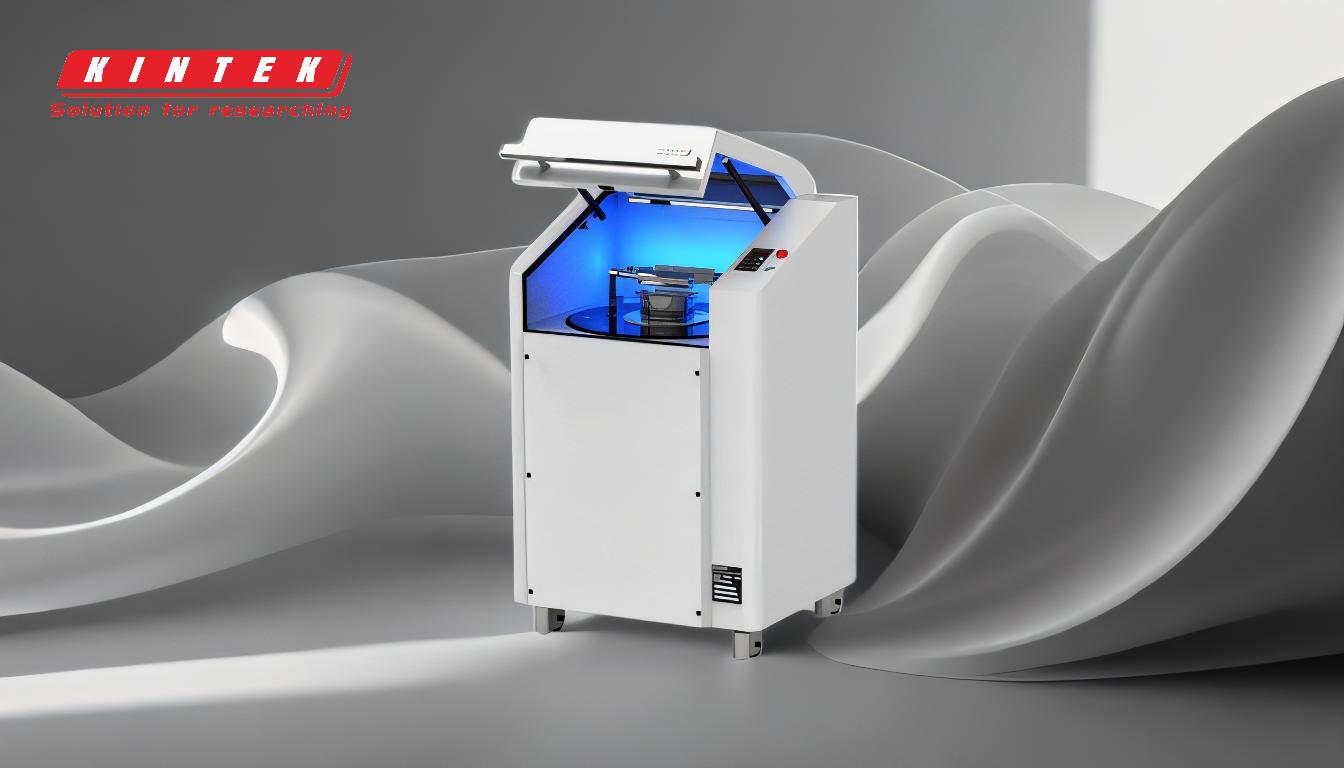
-
Principles of Operation: Impact and Attrition
- Impact: This occurs when heavy balls inside the mill collide with the material, exerting pressure and breaking it into smaller particles.
- Attrition: This involves the reduction of material size as particles collide with the balls and each other, resulting in finer particles over time.
- These two principles work together to ensure effective grinding, with impact providing the initial breakdown and attrition refining the material further.
-
Critical Speed
- The ball mill must achieve a specific rotational speed, known as the critical speed, to ensure the balls rotate along the inner walls of the drum.
- Below the critical speed, the balls may not generate enough force to grind the material effectively.
- Above the critical speed, the balls may stick to the walls due to centrifugal force, reducing grinding efficiency.
-
Drum Dimensions and Design
- The diameter of the drum and the ratio of drum diameter to length (L:D ratio) significantly affect productivity.
- An optimal L:D ratio of 1.56–1.64 ensures efficient grinding by balancing the distribution of balls and material within the mill.
- The shape of the armor surface (inner lining of the drum) also influences grinding efficiency by affecting the movement of the balls.
-
Grinding Media: Balls
- The size, density, and number of balls used in the mill play a crucial role in determining grinding efficiency.
- Larger balls are effective for breaking down coarse materials, while smaller balls reduce void spaces and produce finer particles.
- The filling ratio (percentage of the mill volume filled with balls) must be optimized to ensure effective grinding without overloading the mill.
-
Material Properties
- The physical and chemical properties of the feed material, such as hardness, density, and moisture content, influence the grinding process.
- Harder materials require more energy and time to grind, while softer materials may be ground more quickly.
-
Operational Factors
- Rotation Speed: The speed at which the drum rotates affects the movement of the balls and the grinding efficiency.
- Residence Time: The amount of time the material spends in the mill chamber determines the degree of milling.
- Feed Rate and Level: The rate at which material is fed into the mill and the level of material in the vessel must be controlled to maintain optimal grinding conditions.
-
Timely Removal of Ground Product
- Efficient removal of ground material from the mill ensures that the grinding process remains continuous and prevents over-grinding or clogging.
- This is particularly important for achieving the desired fineness of the final product.
-
Factors Affecting Grinding Performance
- Speed of Rotation: Must be adjusted to achieve the critical speed for optimal grinding.
- Type of Grinding Medium: Steel balls or rods are commonly used, with their size and density tailored to the material being ground.
- Nature of the Material: Hardness, size, and other properties of the material determine the energy required for grinding.
- Filling Ratio: The percentage of the mill volume filled with grinding medium must be optimized to balance grinding efficiency and energy consumption.
By understanding and optimizing these factors, the efficiency and effectiveness of a ball mill can be maximized, ensuring high-quality grinding results for a wide range of materials.
Summary Table:
Key Factor | Description |
---|---|
Principles of Operation | Impact (collision force) and attrition (particle refinement) ensure grinding. |
Critical Speed | Optimal rotation speed for balls to grind material effectively. |
Drum Dimensions | L:D ratio of 1.56–1.64 ensures balanced grinding. |
Grinding Media (Balls) | Size, density, and filling ratio affect grinding efficiency. |
Material Properties | Hardness, density, and moisture content influence grinding energy and time. |
Operational Factors | Rotation speed, residence time, and feed rate determine milling effectiveness. |
Timely Product Removal | Ensures continuous grinding and prevents over-grinding or clogging. |
Optimize your grinding process with expert insights—contact us today for tailored solutions!