When tungsten is heated, its behavior is influenced by several factors, including temperature, environment, and thermal management. At elevated temperatures, tungsten is prone to embrittlement, oxidation, and mechanical or thermal shock, especially when exposed to air above 500°C. To mitigate these issues, precise temperature control and protective environments are necessary. Tungsten heating elements, such as tungsten mesh, can operate at extremely high temperatures, up to 2400°C, with a long-term use temperature of 2300°C. These elements are valued for their fast heating, precise temperature control, and durability. The heating process involves the transfer of kinetic energy from electrons to tungsten atoms, generating heat that warms the surrounding environment. Proper handling and temperature ramping during start-up are critical to prevent embrittlement and ensure longevity.
Key Points Explained:
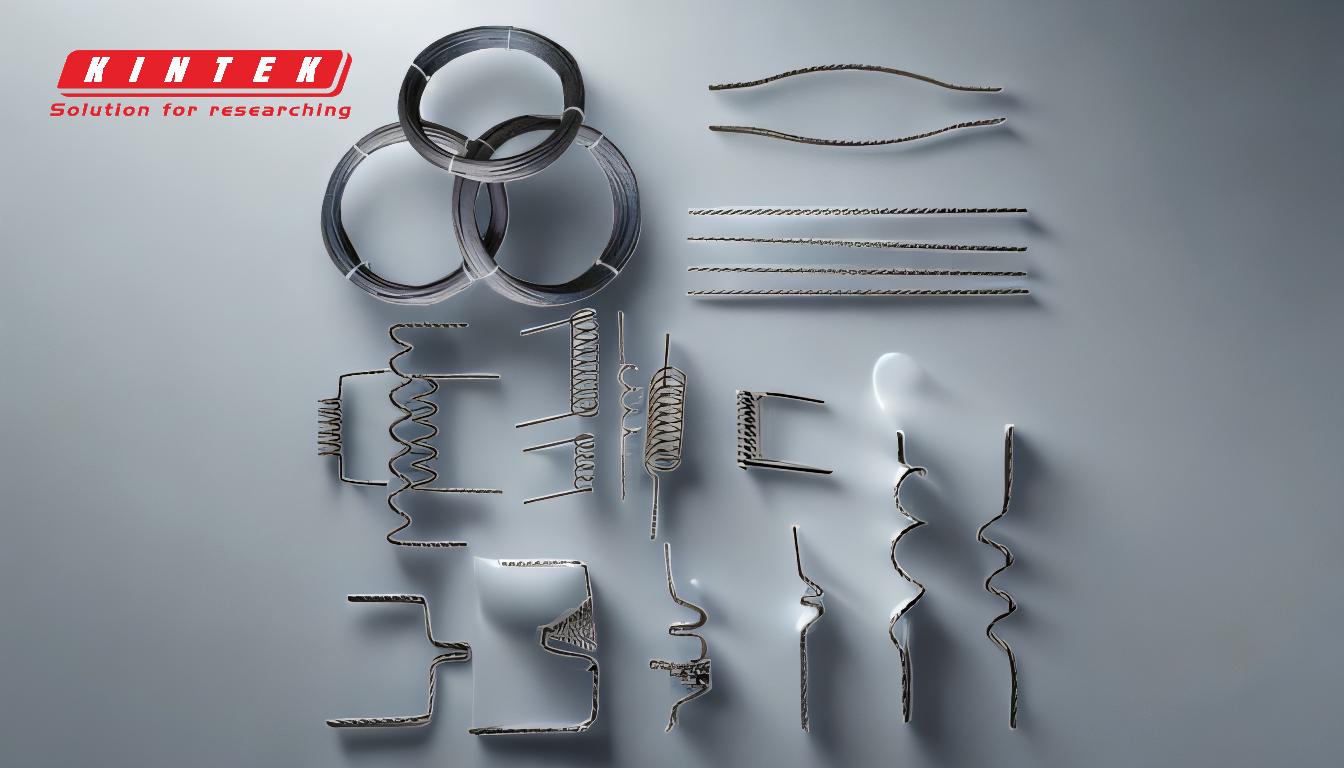
-
Tungsten's Susceptibility to Embrittlement and Oxidation:
- Tungsten becomes brittle and prone to oxidation when exposed to air at temperatures above 500°C (932°F). This oxidation can degrade its structural integrity and performance.
- To prevent embrittlement, especially during cold start-up, a ramping temperature control system is essential. This system gradually increases the temperature, reducing the risk of thermal shock.
-
High-Temperature Performance of Tungsten Heating Elements:
- Tungsten mesh heating elements can withstand extremely high temperatures, with a maximum operating temperature of 2400°C and a recommended long-term use temperature of 2300°C.
- These elements are designed for fast heating and precise temperature control, making them ideal for applications requiring high thermal stability.
-
Mechanism of Heat Generation in Tungsten:
- The heating process in tungsten involves the transfer of kinetic energy from electrons to tungsten atoms. This energy transfer generates heat, which is then used to warm the surrounding environment or chamber.
- This efficient heat generation mechanism contributes to the long service life and reliability of tungsten heating elements.
-
Importance of Environmental Protection:
- Tungsten must be protected from exposure to air at high temperatures to prevent oxidation and degradation. This is typically achieved by operating in inert or vacuum environments.
- Proper environmental control ensures the longevity and performance of tungsten components in high-temperature applications.
-
Applications and Benefits of Tungsten Heating Elements:
- Tungsten heating elements are widely used in industries requiring high-temperature processes, such as semiconductor manufacturing, vacuum furnaces, and high-temperature research.
- Their fast heating, precise control, and durability make them a preferred choice for demanding thermal applications.
By understanding these key points, equipment and consumable purchasers can make informed decisions about the use of tungsten in high-temperature environments, ensuring optimal performance and longevity.
Summary Table:
Key Aspect | Details |
---|---|
Embrittlement & Oxidation | Occurs above 500°C in air; requires ramping temperature control for safety. |
High-Temperature Performance | Operates up to 2400°C; long-term use at 2300°C for stability and durability. |
Heat Generation Mechanism | Kinetic energy transfer from electrons to tungsten atoms generates heat. |
Environmental Protection | Requires inert or vacuum environments to prevent oxidation. |
Applications | Used in semiconductor manufacturing, vacuum furnaces, and high-temp research. |
Need high-performance tungsten heating solutions? Contact our experts today to learn more!