A ceramic mill is a type of milling tool used in machining processes, specifically designed for cutting, shaping, or removing material from a workpiece. It is made from advanced ceramic materials, such as silicon nitride or zirconia, which provide exceptional hardness, wear resistance, and thermal stability. Ceramic mills are particularly effective for high-speed machining of hard materials like hardened steels, superalloys, and composites. They are widely used in industries such as aerospace, automotive, and medical manufacturing due to their ability to maintain precision and durability under extreme conditions. Compared to traditional carbide mills, ceramic mills offer longer tool life and higher productivity, making them a valuable choice for demanding applications.
Key Points Explained:
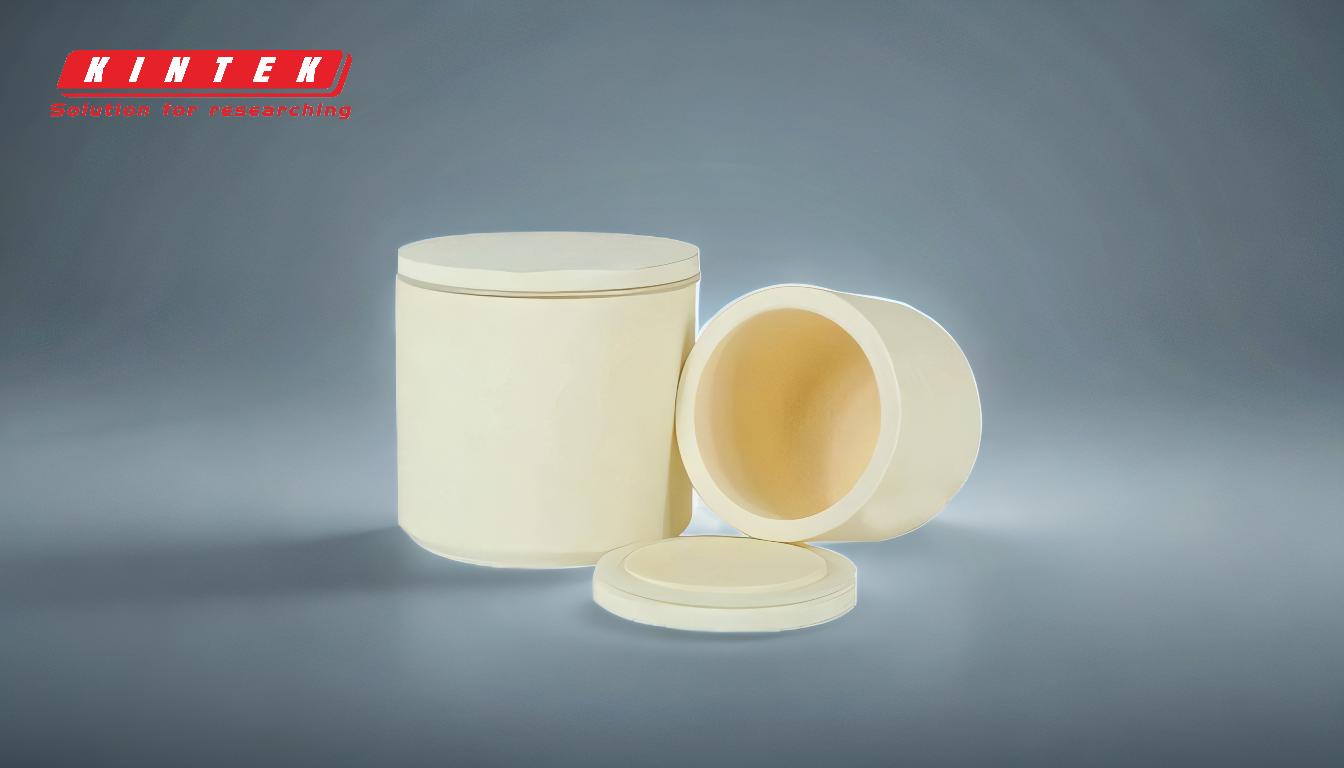
-
Definition and Purpose of a Ceramic Mill:
- A ceramic mill is a cutting tool used in machining operations to shape or remove material from a workpiece.
- It is specifically designed for high-performance applications, particularly in industries requiring precision and durability.
-
Material Composition:
- Ceramic mills are made from advanced ceramic materials, such as silicon nitride (Si3N4) or zirconia (ZrO2).
- These materials are chosen for their exceptional properties, including high hardness, wear resistance, and thermal stability.
-
Advantages Over Traditional Mills:
- Hardness: Ceramic mills are significantly harder than traditional carbide mills, allowing them to cut through tough materials like hardened steels and superalloys.
- Wear Resistance: The wear-resistant properties of ceramics extend the tool's lifespan, reducing the need for frequent replacements.
- Thermal Stability: Ceramic mills can withstand high temperatures generated during high-speed machining, maintaining their performance without deformation.
-
Applications in Industry:
- Aerospace: Used for machining high-strength materials like titanium and nickel-based alloys.
- Automotive: Ideal for cutting hardened steels and composites in engine components and transmission parts.
- Medical Manufacturing: Employed in precision machining of biocompatible materials for implants and surgical tools.
-
Performance Benefits:
- High-Speed Machining: Ceramic mills enable faster cutting speeds, improving productivity.
- Longer Tool Life: Reduced wear and tear result in fewer tool changes and lower operational costs.
- Precision: Maintains dimensional accuracy even under extreme conditions, ensuring high-quality finished products.
-
Comparison with Carbide Mills:
- While carbide mills are more commonly used due to their versatility and lower cost, ceramic mills outperform them in specific high-demand applications.
- Ceramic mills are better suited for machining hard materials and high-temperature environments, where carbide tools may fail.
-
Considerations for Purchasers:
- Material Compatibility: Ensure the ceramic mill is suitable for the specific materials being machined.
- Machining Conditions: Evaluate the operating environment, including speed, temperature, and cutting forces.
- Cost-Benefit Analysis: While ceramic mills may have a higher upfront cost, their extended lifespan and productivity gains often justify the investment.
By understanding these key points, purchasers can make informed decisions about whether ceramic mills are the right choice for their specific machining needs.
Summary Table:
Feature | Ceramic Mill | Carbide Mill |
---|---|---|
Hardness | Exceptionally high, ideal for cutting hard materials like hardened steels. | Lower than ceramic mills, suitable for general-purpose machining. |
Wear Resistance | Superior, leading to longer tool life and fewer replacements. | Moderate, requires more frequent replacements in demanding applications. |
Thermal Stability | Excellent, maintains performance under high temperatures. | Limited, may deform under extreme heat. |
Applications | Aerospace, automotive, medical manufacturing (hard materials, high-speed needs). | Versatile, suitable for a wide range of materials and applications. |
Cost | Higher upfront cost but cost-effective in the long run due to durability. | Lower upfront cost but may incur higher operational costs over time. |
Ready to enhance your machining process? Contact us today to find the perfect ceramic mill for your needs!