A planetary mill, specifically a planetary ball mill, is a specialized grinding machine used in laboratories and industrial settings to grind materials into fine powders. It operates on a unique principle where grinding jars (planets) rotate around a central axis while simultaneously rotating in the opposite direction on a rotating disc (sun wheel). This dual rotational movement generates high-energy collisions between grinding balls and the material inside the jars, resulting in efficient and uniform grinding. Planetary mills are highly versatile, allowing control over grinding speed and movement to achieve specific particle sizes and textures. They are widely used in materials science, chemistry, and pharmaceuticals for tasks such as sample preparation, nanoparticle synthesis, and mechanical alloying.
Key Points Explained:
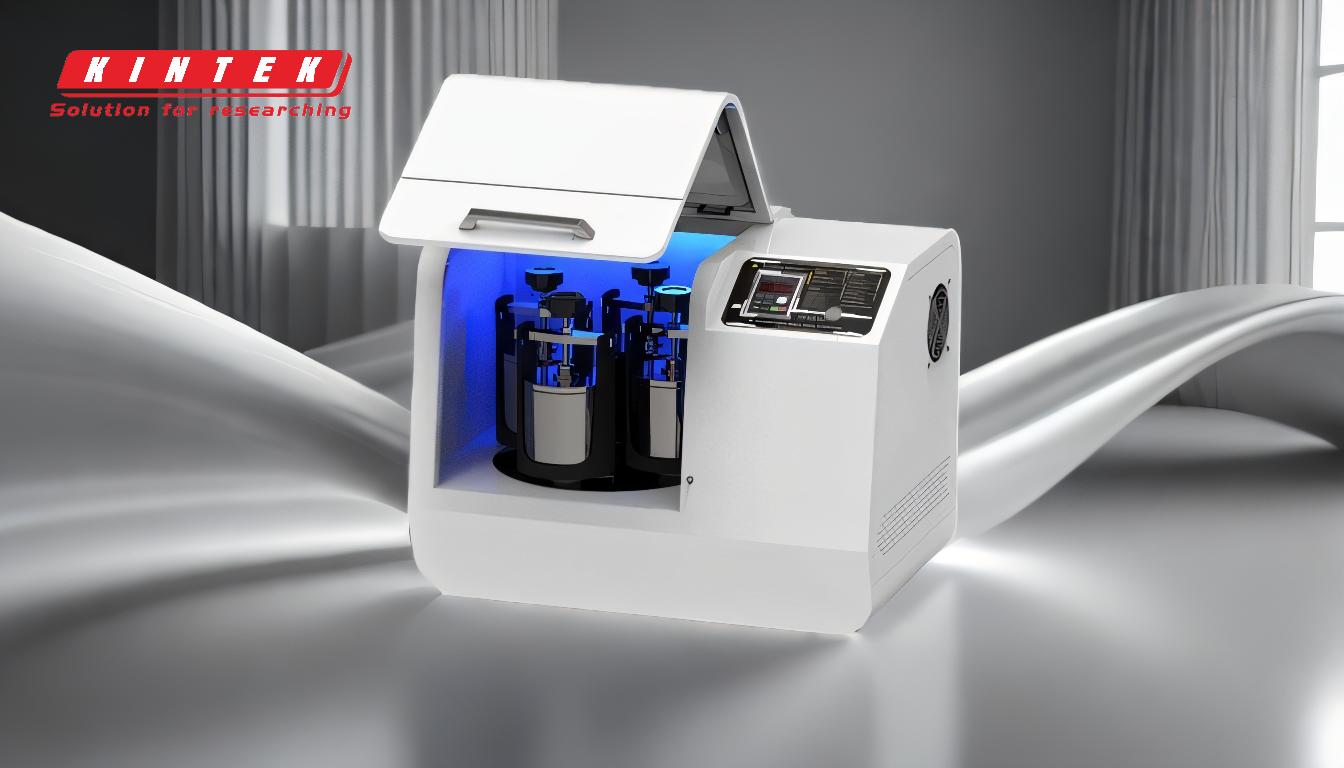
-
Basic Principle of Operation:
- A planetary mill operates by rotating grinding jars (planets) around a central axis while the jars themselves rotate in the opposite direction on a rotating disc (sun wheel).
- This dual rotation creates centrifugal forces that propel the grinding balls inside the jars, leading to high-energy collisions with the material being ground.
- The opposing rotations ensure that the grinding balls and material are constantly in motion, resulting in efficient and uniform grinding.
-
Components of a Planetary Mill:
- Rotating Disc (Sun Wheel): The central disc that rotates in one direction, driving the movement of the grinding jars.
- Grinding Jars (Planets): Smaller jars mounted on the sun wheel that rotate in the opposite direction. These jars contain the grinding balls and the material to be ground.
- Grinding Balls: Typically made of hard materials like steel, ceramic, or tungsten carbide, these balls collide with the material to break it down into fine particles.
- Central Shaft: The axis around which the grinding jars rotate.
-
Mechanism of Grinding:
- The grinding process relies on the kinetic energy transferred from the rotating jars and sun wheel to the grinding balls.
- As the jars and sun wheel rotate in opposite directions, the grinding balls are subjected to Coriolis and centrifugal forces, causing them to move in complex trajectories.
- These movements result in high-energy impacts and friction between the balls and the material, leading to efficient grinding and particle size reduction.
-
Control and Versatility:
- Planetary mills allow precise control over grinding parameters such as rotational speed, grinding time, and the size/number of grinding balls.
- By adjusting these parameters, users can achieve specific particle sizes, textures, and grinding outcomes tailored to their needs.
- This versatility makes planetary mills suitable for a wide range of applications, from fine powder production to mechanical alloying and nanoparticle synthesis.
-
Applications:
- Materials Science: Used for grinding and mixing materials to create composites, alloys, or nanomaterials.
- Chemistry: Ideal for sample preparation, chemical synthesis, and mechanochemical reactions.
- Pharmaceuticals: Employed for grinding active pharmaceutical ingredients (APIs) into fine powders for drug formulation.
- Geology and Mining: Used to prepare rock and mineral samples for analysis.
-
Advantages of Planetary Mills:
- High Grinding Efficiency: The dual rotational movement ensures thorough and uniform grinding, even for hard or brittle materials.
- Scalability: Suitable for both small-scale laboratory experiments and larger industrial processes.
- Flexibility: Can handle a variety of materials, including metals, ceramics, polymers, and biological samples.
- Precision: Allows fine-tuning of grinding conditions to achieve desired results.
-
Limitations and Considerations:
- Heat Generation: The high-energy grinding process can generate heat, which may affect heat-sensitive materials. Cooling systems or intermittent grinding may be required.
- Wear and Tear: The grinding balls and jars are subject to wear over time, especially when grinding hard materials. Regular maintenance and replacement may be necessary.
- Cost: Planetary mills can be expensive due to their complex design and high-performance capabilities.
-
Comparison with Other Grinding Methods:
- Compared to traditional ball mills, planetary mills offer higher grinding efficiency and faster processing times due to their unique dual rotational mechanism.
- Unlike vibratory mills, which rely on vibrations for grinding, planetary mills use centrifugal forces, resulting in more controlled and consistent grinding outcomes.
In summary, a planetary mill is a highly efficient and versatile grinding machine that leverages dual rotational movements to achieve precise and uniform grinding. Its ability to control grinding parameters and handle a wide range of materials makes it an indispensable tool in various scientific and industrial applications. However, users must consider factors such as heat generation, wear, and cost when selecting and operating a planetary mill.
Summary Table:
Aspect | Details |
---|---|
Principle | Dual rotational movement: grinding jars rotate around a central axis and opposite direction on a sun wheel. |
Components | Rotating disc (sun wheel), grinding jars (planets), grinding balls, central shaft. |
Grinding Mechanism | High-energy collisions and friction from centrifugal and Coriolis forces. |
Applications | Materials science, chemistry, pharmaceuticals, geology, and mining. |
Advantages | High efficiency, scalability, flexibility, and precision. |
Limitations | Heat generation, wear and tear, and high cost. |
Ready to enhance your grinding processes? Contact us today to find the perfect planetary mill for your needs!