A two-roll mill is a specialized machine used primarily in the rubber and plastic industries for compounding, mixing, and refining materials. It consists of two horizontally opposed stainless steel rolls that rotate in opposite directions at different speeds. This design allows for the efficient mixing of rubber or plastic materials with various additives, such as pigments, fillers, and curing agents. The machine is essential for tasks like formula development, color matching, small batch testing, and quality control. It operates by generating heat through friction, which helps in breaking down large molecules in the rubber, ensuring uniform mixing and refining of the material. The two-roll mill is valued for its durability, temperature control, and cost-effectiveness in production processes.
Key Points Explained:
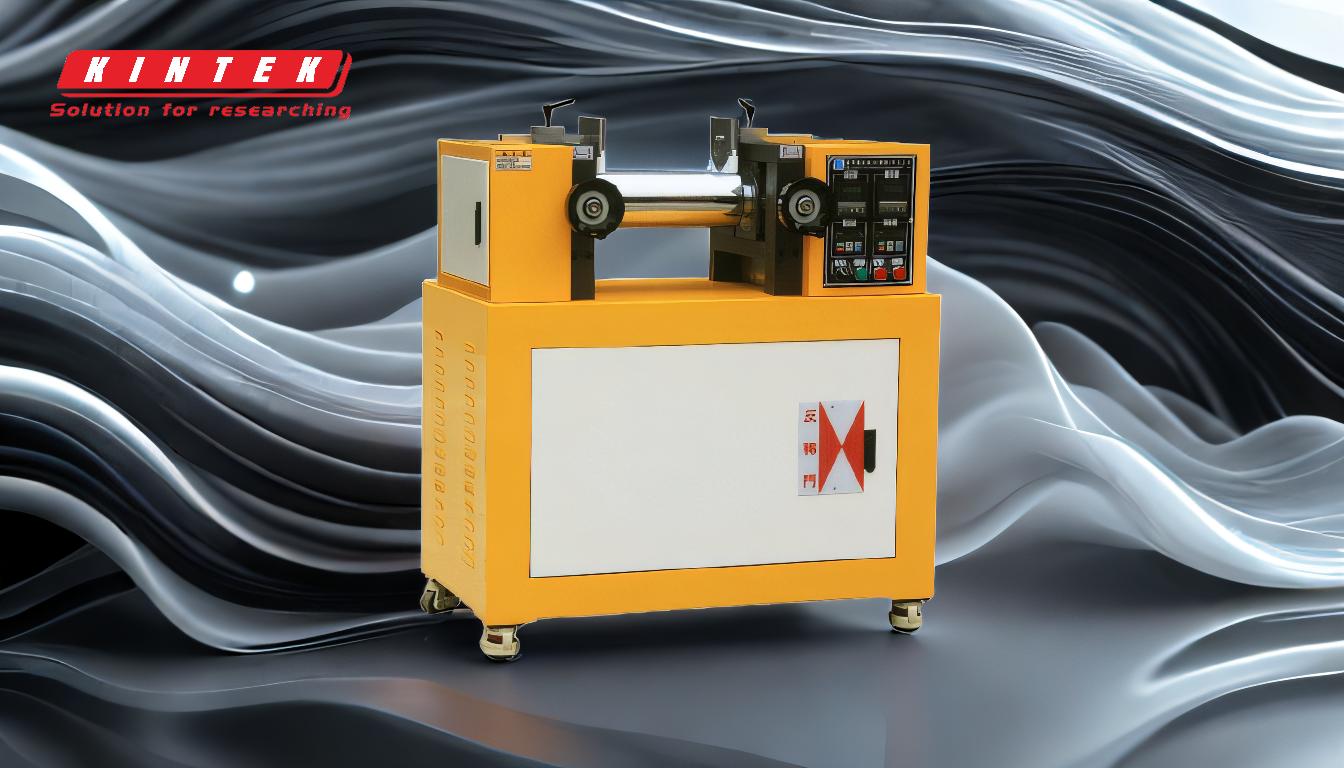
-
Basic Functionality and Design:
- A two-roll mill consists of two horizontally opposed stainless steel rolls that rotate in opposite directions at different speeds.
- The rotation of the rolls creates a shearing action, which is crucial for mixing and refining rubber or plastic materials.
- The machine is designed to handle materials like natural rubber, synthetic rubber, and various polymers.
-
Applications in Rubber and Plastic Industries:
- Rubber Compounding: The two-roll mill is extensively used in the rubber industry to mix rubber with additives such as curing agents, fillers, and pigments.
- Plastic Mixing: It is also used in the plastic industry for tasks like PVC powder mixing, color sampling, and polymer milling.
- Formula Development and Testing: The machine is essential for developing new rubber or plastic formulas, conducting small batch tests, and ensuring quality control.
-
Temperature Control and Cooling:
- The two-roll mill is designed to provide optimum temperature control during the mixing process.
- Cooling systems are often integrated to prevent overheating, which is crucial for maintaining the quality of the material being processed.
-
Material Refining Process:
- The machine works by breaking down large molecules in the rubber through repeated kneading and chemical action.
- This process ensures that all components within the rubber are mixed uniformly, achieving the desired consistency and properties.
-
Versatility and Customization:
- The two-roll mill is highly customizable, allowing it to be adapted for various industrial applications.
- It can be used for material development, testing, and educational purposes, making it a versatile tool in both research and production settings.
-
Cost-Effectiveness and Maintenance:
- The machine is designed to reduce production costs by ensuring efficient mixing and minimal waste.
- It requires minimal maintenance, which further contributes to its cost-effectiveness in industrial applications.
-
Importance in Quality Control:
- The two-roll mill plays a critical role in quality control by ensuring that the mixed materials meet the required standards.
- It is used for contrast testing, color matching, and ensuring the uniformity of pigments and polymers.
By understanding these key points, one can appreciate the importance of the two-roll mill in the rubber and plastic industries, where it serves as an indispensable tool for material processing, development, and quality assurance.
Summary Table:
Key Aspect | Details |
---|---|
Basic Functionality | Two horizontally opposed stainless steel rolls rotating at different speeds. |
Applications | Rubber compounding, plastic mixing, formula development, and quality control. |
Temperature Control | Integrated cooling systems for optimal temperature regulation. |
Material Refining Process | Breaks down large molecules for uniform mixing and refining. |
Versatility | Customizable for various industrial, research, and educational applications. |
Cost-Effectiveness | Reduces production costs with efficient mixing and minimal maintenance. |
Quality Control | Ensures uniformity, color matching, and adherence to material standards. |
Upgrade your material processing with a two-roll mill—contact us today for expert advice!
For more information on related equipment, check out our laboratory mill and rubber calender.