An insert in casting refers to a component, often made of steel or another durable material, that is placed into a mold cavity to create specific features or shapes in the final cast part. These inserts are used to enhance the functionality, durability, or complexity of the cast product. They are particularly useful in die casting, where precision and repeatability are critical. By incorporating inserts, manufacturers can achieve intricate designs, improve part strength, or integrate additional materials without altering the entire mold structure.
Key Points Explained:
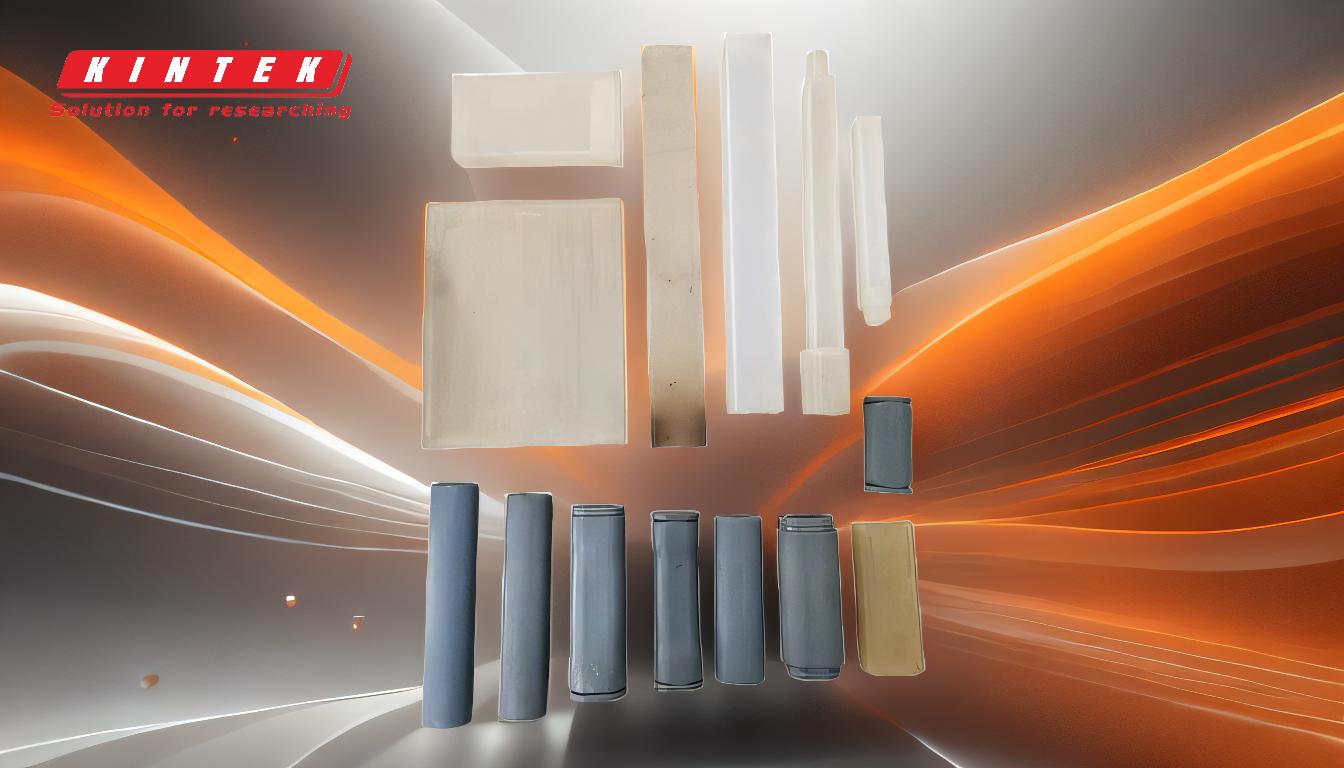
-
Definition of a Casting Insert:
- A casting insert is a separate piece of material, typically steel, that is placed into a mold cavity before the casting process begins.
- It is designed to create specific features, shapes, or functionalities in the final cast part.
-
Purpose of Using Inserts:
- Complexity and Precision: Inserts allow for the creation of intricate and precise features that might be difficult or impossible to achieve with a standard mold.
- Enhanced Durability: Inserts can be made from materials that are more durable than the base mold material, increasing the lifespan of the mold and the quality of the cast parts.
- Material Integration: Inserts enable the integration of different materials within a single cast part, which can be crucial for applications requiring specific material properties in certain areas.
-
Types of Inserts:
- Steel Inserts: Commonly used due to their strength and durability, especially in high-pressure die casting.
- Ceramic Inserts: Used in applications requiring high thermal resistance or electrical insulation.
- Composite Inserts: These can combine the benefits of different materials, such as strength and lightweight properties.
-
Insert Placement and Design:
- Precision Placement: Inserts must be precisely placed within the mold cavity to ensure the desired feature is accurately formed in the final part.
- Design Considerations: The design of the insert must account for factors such as thermal expansion, material compatibility, and ease of removal or replacement.
-
Benefits of Using Inserts:
- Cost Efficiency: By using inserts, manufacturers can avoid the need for complex and expensive mold modifications.
- Flexibility: Inserts provide flexibility in design, allowing for quick changes or updates to the mold without significant downtime.
- Improved Part Quality: Inserts can lead to higher quality parts with better surface finishes and more precise dimensions.
-
Challenges and Considerations:
- Material Compatibility: Ensuring that the insert material is compatible with the casting material and process is crucial to avoid defects or failures.
- Thermal Management: Inserts must be able to withstand the thermal conditions of the casting process without degrading or causing issues in the final part.
- Maintenance and Replacement: Inserts may require regular maintenance or replacement, especially in high-volume production environments.
By understanding these key points, a purchaser of equipment or consumables can make informed decisions about the use of inserts in their casting processes, ensuring they achieve the desired outcomes in terms of part quality, cost efficiency, and production flexibility.
Summary Table:
Key Aspect | Details |
---|---|
Definition | A separate piece of material placed into a mold to create specific features. |
Purpose | Achieve complexity, precision, durability, and material integration. |
Types | Steel, ceramic, and composite inserts. |
Benefits | Cost efficiency, design flexibility, and improved part quality. |
Challenges | Material compatibility, thermal management, and maintenance. |
Ready to optimize your casting process with inserts? Contact us today for expert guidance!