An internal batch mixer is a specialized machine used in industries like rubber manufacturing to mix and plasticize polymer materials. It operates in a closed system with adjustable temperature and pressure, ensuring consistent and high-quality mixing. The process involves preheating the mixer, adding raw materials (such as rubber, fillers, and softeners) in a specific sequence, and monitoring the temperature. The mixed material is then processed further, often on an open mill, to add sulfur and cool the product. Internal mixers are versatile, capable of handling various rubber compounds without requiring changes to the machine's geometry.
Key Points Explained:
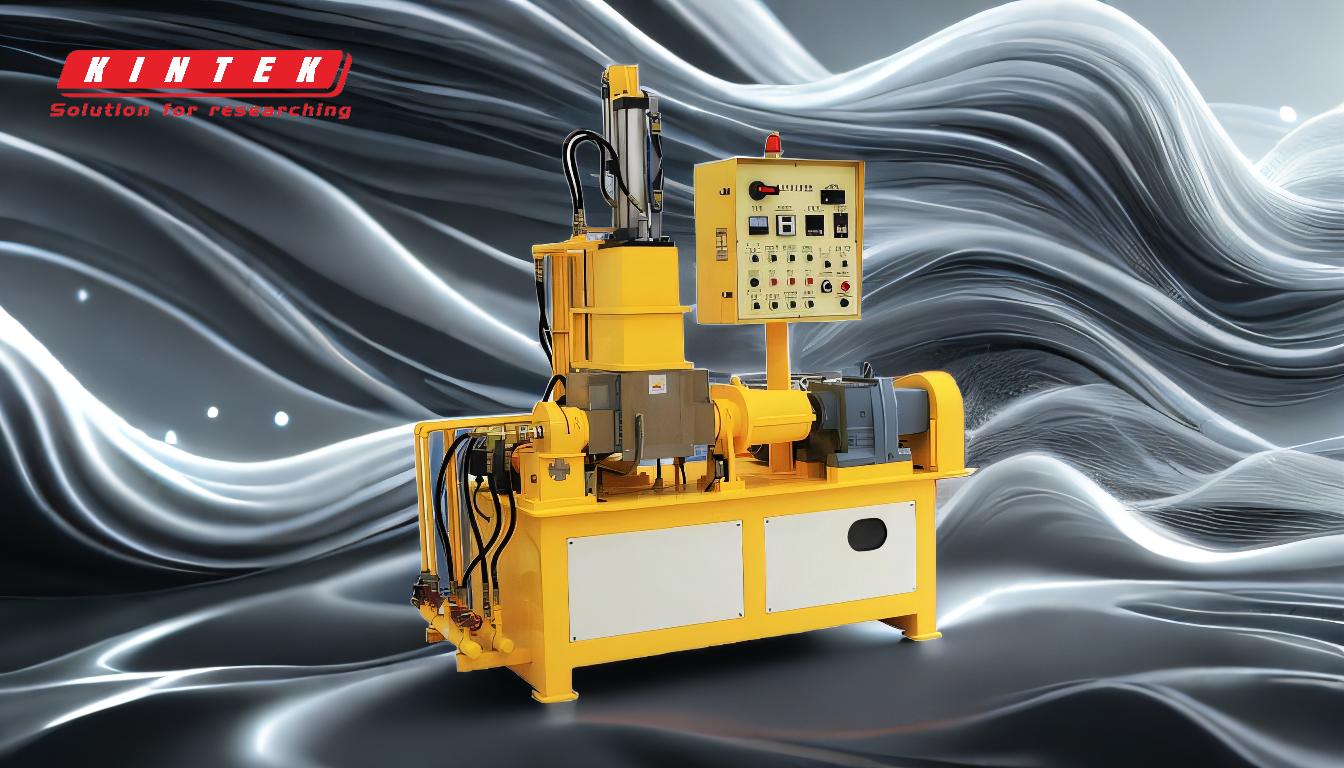
-
Definition and Purpose of an Internal Batch Mixer:
- An internal batch mixer is a machine designed for mixing and plasticizing polymer materials, such as rubber, in a closed system.
- It features a pair of rotors that rotate relative to each other, creating shear forces that mix the materials uniformly.
- The mixer operates intermittently, meaning it processes materials in batches rather than continuously.
- It is widely used in industries where mix quality and consistency are critical, such as rubber manufacturing.
-
Key Components and Functionality:
- Rotors: The rotors are the core components that generate shear forces to mix materials. Their design and rotation speed are crucial for achieving the desired mix quality.
- Closed System: The mixer operates in a closed state, allowing for precise control over temperature and pressure, which are essential for consistent results.
- Adjustable Parameters: Temperature and pressure can be adjusted to suit different materials and mixing requirements.
- Versatility: Internal mixers can handle a wide range of rubber compounds without needing modifications to the machine's geometry.
-
Operating Process:
- Preheating: The mixer is preheated to the required temperature to ensure optimal mixing conditions.
-
Material Addition: Raw materials are added in a specific sequence:
- Raw rubber is added first and mixed.
- Small materials, fillers (e.g., carbon black), and liquid softeners are added next.
- Temperature Monitoring: The temperature is closely monitored to prevent overheating and ensure proper mixing.
- Further Processing: The mixed material is transferred to an open mill, where sulfur is added, and the material is cooled and labeled for later use.
-
Advantages of Internal Batch Mixers:
- Consistency: The closed system and adjustable parameters ensure consistent mix quality.
- Efficiency: The machine can handle large batches, making it suitable for industrial-scale production.
- Versatility: It can process a wide range of materials without requiring changes to the machine's setup.
- Quality Control: The ability to monitor and adjust temperature and pressure allows for precise control over the mixing process.
-
Applications:
- Rubber Manufacturing: Internal batch mixers are extensively used in the rubber industry to produce compounds with specific properties.
- Polymer Processing: They are also used in the plastics industry for mixing and plasticizing polymer materials.
- Other Industries: Any industry requiring consistent and high-quality mixing of materials can benefit from using an internal batch mixer.
-
Considerations for Equipment Purchasers:
- Capacity: Ensure the mixer's capacity aligns with production needs, considering the filling factor (typically 0.6-0.7).
- Material Compatibility: Verify that the mixer can handle the specific materials used in your production process.
- Temperature and Pressure Control: Look for mixers with precise and adjustable temperature and pressure controls.
- Maintenance and Durability: Consider the ease of maintenance and the durability of the machine to minimize downtime and long-term costs.
By understanding these key points, equipment and consumable purchasers can make informed decisions when selecting an internal batch mixer for their specific needs.
Summary Table:
Key Aspect | Details |
---|---|
Definition | A machine for mixing and plasticizing polymer materials in a closed system. |
Key Components | Rotors, closed system, adjustable temperature and pressure controls. |
Operating Process | Preheating, material addition, temperature monitoring, further processing. |
Advantages | Consistency, efficiency, versatility, and precise quality control. |
Applications | Rubber manufacturing, polymer processing, and other industries. |
Purchasing Considerations | Capacity, material compatibility, temperature control, and durability. |
Ready to enhance your production process? Contact us today to find the perfect internal batch mixer for your needs!