An internal mixer is a specialized machine used primarily in rubber manufacturing and other industries for plasticizing and mixing polymer materials. It consists of a mixing chamber with two rotors that rotate relative to each other, enabling efficient mixing of viscous materials. The machine operates in a closed state with adjustable temperature and pressure, ensuring consistent mix quality. Internal mixers are versatile, capable of handling a wide range of rubber compounds without requiring changes to the machine geometry. They are widely used due to their ability to produce high-quality mixtures, though they require powerful motors and gearboxes and can be challenging to maintain if blockages occur.
Key Points Explained:
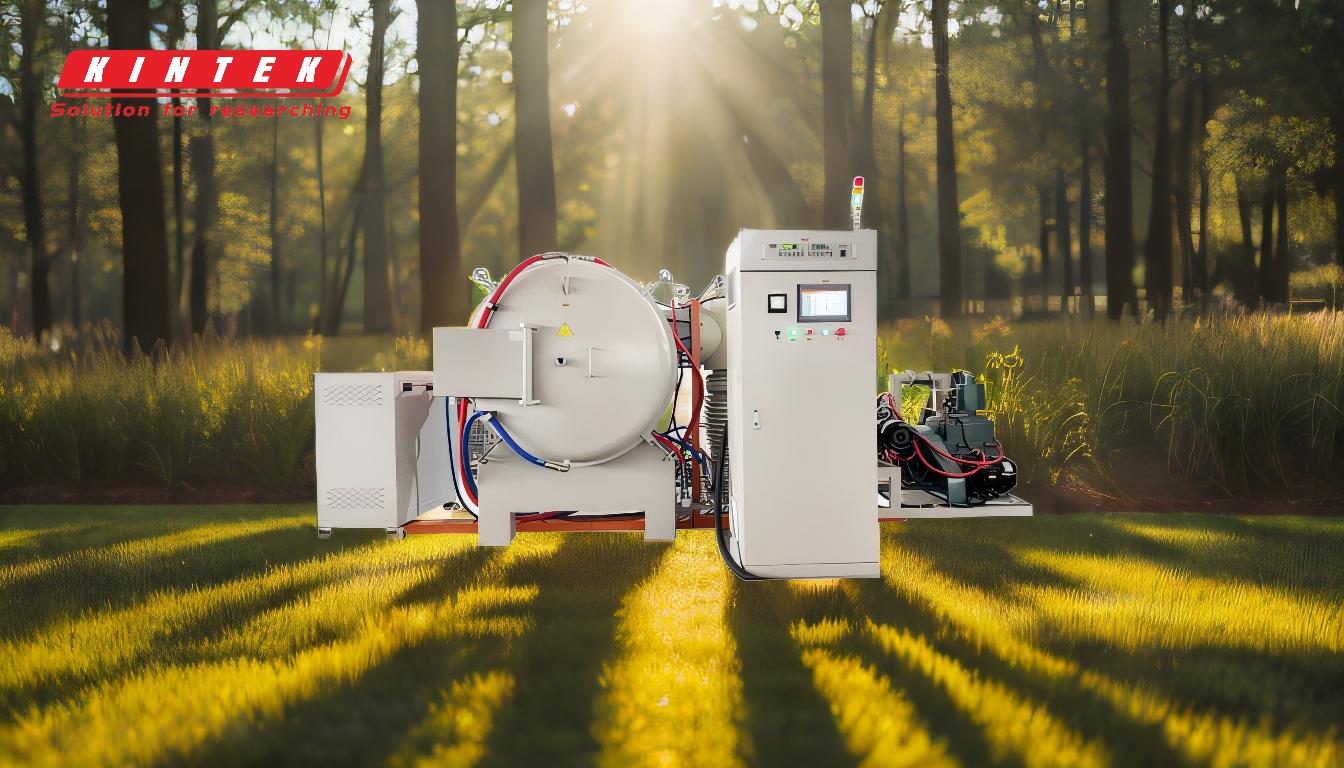
-
Definition and Purpose:
- An internal mixer is a machine designed for plasticizing and mixing polymer materials, particularly rubber compounds, in a closed state.
- It is equipped with a pair of rotors that rotate relative to each other, facilitating efficient mixing of viscous materials.
- The machine is widely used in rubber manufacturing and other industries where mix quality and consistency are critical.
-
Key Components:
- Mixing Chamber: The working part of the mixer, composed of two sets of C-shaped heating chambers and two rollers. It is equipped with a double circulating water jacket for temperature control.
- Rotors: Two rotors that rotate at different speeds to plasticize and mix materials.
- Cooling System: Ensures the temperature is regulated during the mixing process with the help of a cooling circulator.
- Lubrication System: Keeps the machine running smoothly.
- Sealing Device: Maintains the closed state of the mixing chamber.
- Transmission Device: Transfers power from the motor to the rotors.
-
Operation Process:
- Preheating: The mixer is preheated to the required temperature.
- Material Addition: Raw rubber is added first, followed by small materials, carbon black or filler, and liquid softener.
- Mixing: The materials are mixed in the chamber while monitoring the temperature.
- Post-Processing: The mixed rubber is processed on an open mill, where sulfur is added, and the material is cooled and labeled for later use.
-
Advantages:
- Versatility: Capable of mixing a wide range of rubber compounds without needing changes to the machine geometry.
- Consistency: Ensures high-quality and consistent mixtures due to the closed state and adjustable temperature and pressure.
- Efficiency: Handles viscous mixtures effectively, making it a preferred choice in rubber manufacturing.
-
Challenges:
- Maintenance: Requires a powerful motor and gearbox, and if blockages occur, it can be difficult to clear and restart production, leading to significant downtime.
- Complexity: The operation involves several steps and requires careful monitoring of system parameters and temperature.
-
Applications:
- Primarily used in rubber manufacturing for producing high-quality rubber compounds.
- Also used in other industries where mix quality and consistency are important, such as plastics and polymers.
By understanding these key points, purchasers and users of internal mixers can better appreciate the machine's capabilities, operational requirements, and potential challenges, ensuring optimal use and maintenance.
Summary Table:
Aspect | Details |
---|---|
Purpose | Plasticizing and mixing polymer materials, especially rubber compounds. |
Key Components | Mixing chamber, rotors, cooling system, lubrication system, sealing device. |
Advantages | Versatility, consistent mix quality, efficient handling of viscous materials. |
Challenges | Requires powerful motors, complex maintenance, potential for blockages. |
Applications | Rubber manufacturing, plastics, and polymer industries. |
Ready to enhance your rubber or polymer production? Contact us today to find the perfect internal mixer for your needs!