Carburizing is a case hardening process used to enhance the surface properties of low-carbon steel alloys. By diffusing carbon into the steel's surface at high temperatures, the process creates a hard, wear-resistant outer layer while maintaining a soft, ductile core. This is achieved through a combination of heating the steel in a carbon-rich environment and quenching it in oil. Carburizing is widely used in industries requiring parts with high surface hardness and durability, such as automotive and machinery manufacturing. The process can be applied to the entire surface or specific areas, with case depths typically ranging from 0.020″ to 0.050″.
Key Points Explained:
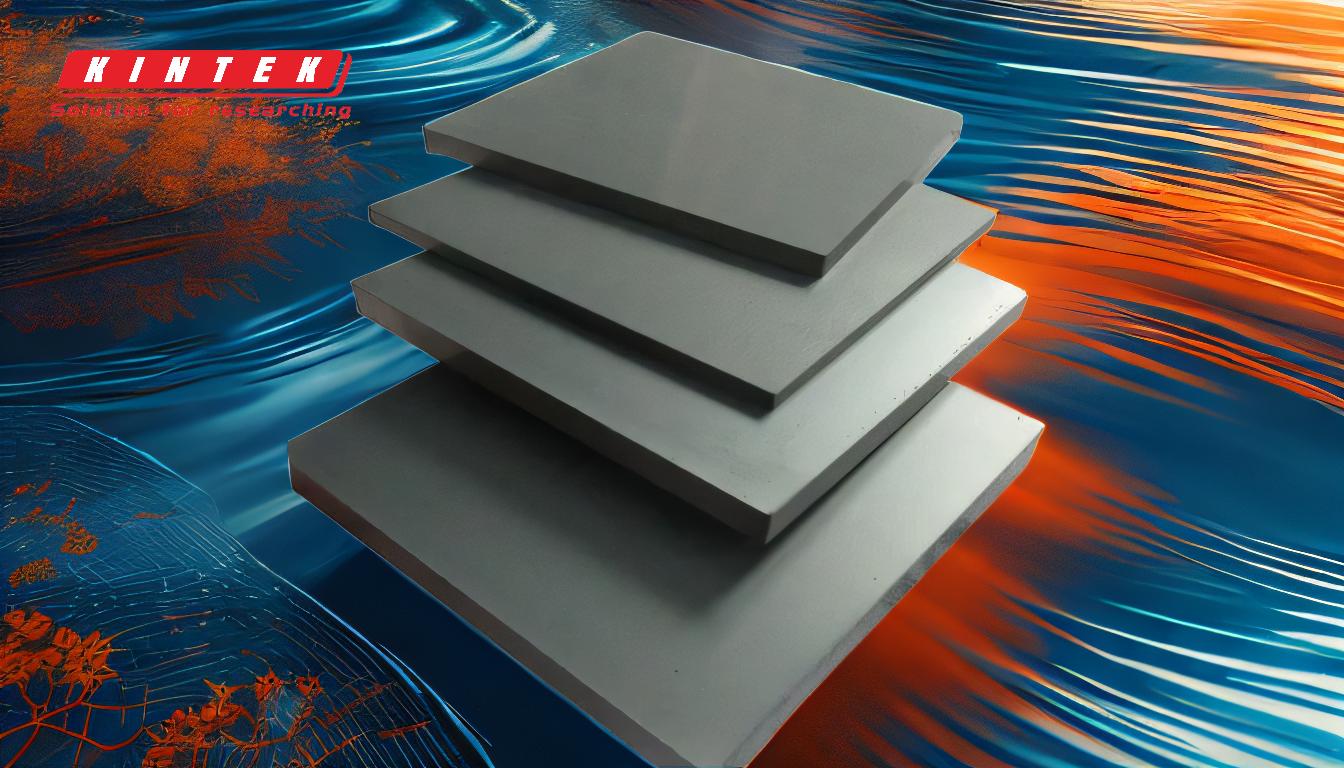
-
Definition and Purpose of Carburizing:
- Carburizing is a heat treatment process that enriches the surface of low-carbon steel with carbon.
- The primary goal is to increase surface hardness and abrasion resistance while retaining a soft, ductile core.
- This dual property makes carburized parts ideal for applications requiring both wear resistance and toughness.
-
Process Mechanism:
- The steel is heated to elevated temperatures (typically between 850°C and 950°C) in a carbon-rich environment.
- Carbon atoms diffuse into the steel's surface, forming a high-carbon layer.
- After carburizing, the steel is quenched in oil to harden the surface.
-
Types of Carburizing:
- Gas Carburizing: Uses a carbon-rich gas (e.g., methane or propane) to introduce carbon into the steel.
- Liquid Carburizing: Involves immersing the steel in a molten salt bath containing carbon.
- Solid Carburizing: Uses solid carbon-rich materials (e.g., charcoal) packed around the steel parts.
-
Case Depth and Control:
- Case depth refers to the thickness of the hardened surface layer, typically ranging from 0.020″ to 0.050″.
- Depth can be controlled by adjusting factors such as temperature, time, and carbon concentration in the atmosphere.
- Specific areas can be masked using carbon-stopping paint to prevent carburizing in undesired regions.
-
Applications and Benefits:
- Commonly used in automotive components (e.g., gears, shafts, and bearings) and industrial machinery.
- Provides excellent wear resistance, extending the lifespan of parts subjected to friction and stress.
- Maintains core ductility, reducing the risk of brittle failure.
-
Comparison with Other Hardening Methods:
- Unlike through-hardening, which hardens the entire part, carburizing selectively hardens the surface.
- Can be used as a precursor to induction hardening, where localized hardening is required.
-
Material Considerations:
- Best suited for low-carbon steels (e.g., AISI 1018, 1020) due to their ability to absorb carbon.
- High-carbon steels are not typically carburized, as they already have sufficient carbon content.
-
Environmental and Process Control:
- Requires precise control of temperature, atmosphere, and time to achieve consistent results.
- Endothermic atmospheres are commonly used to maintain a stable carbon-rich environment.
By understanding these key points, purchasers of equipment and consumables can make informed decisions about when and how to use carburizing for their specific applications. This process is particularly valuable for industries requiring high-performance components with a balance of surface hardness and core toughness.
Summary Table:
Aspect | Details |
---|---|
Purpose | Increases surface hardness and wear resistance while retaining core ductility. |
Process | Heating steel in a carbon-rich environment, followed by oil quenching. |
Types | Gas, liquid, and solid carburizing. |
Case Depth | Typically 0.020″ to 0.050″, controlled by temperature, time, and atmosphere. |
Applications | Automotive parts (gears, shafts, bearings) and industrial machinery. |
Material Suitability | Best for low-carbon steels (e.g., AISI 1018, 1020). |
Key Benefits | Enhanced wear resistance, extended part lifespan, and reduced brittle failure. |
Discover how carburizing can improve your components' performance—contact our experts today!