Ceramic powder is primarily composed of inorganic, non-metallic materials that are processed into fine particles. These materials often include clay, silica, alumina, and other minerals, which are selected based on the desired properties of the final ceramic product. The composition can vary widely depending on the application, such as in pottery, advanced ceramics, or industrial uses. The raw materials are typically mined, purified, and then ground into fine powders before being shaped and fired at high temperatures to form the final ceramic product.
Key Points Explained:
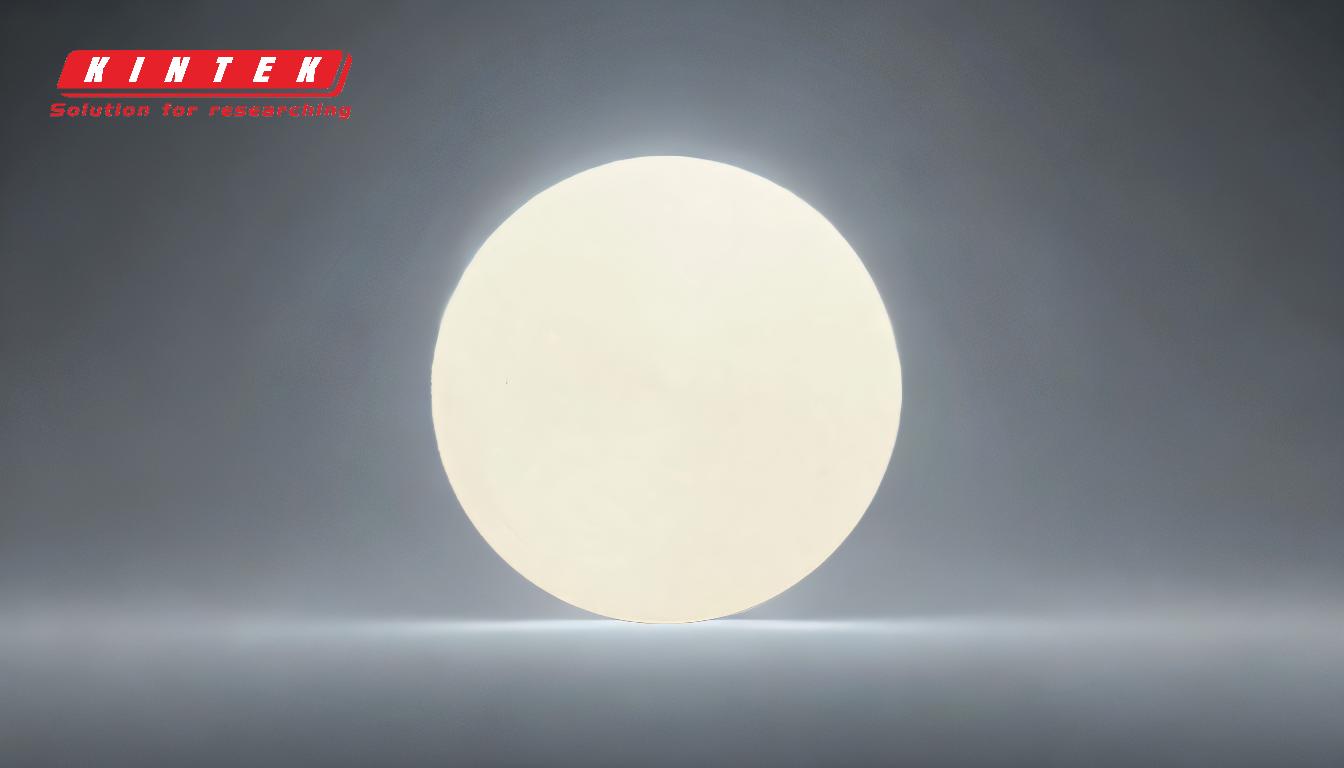
-
Primary Components of Ceramic Powder:
- Clay: A key ingredient in many ceramic powders, clay provides plasticity and workability when mixed with water. It is primarily composed of hydrated aluminum silicates.
- Silica (SiO₂): Silica is a fundamental component that contributes to the hardness and durability of ceramics. It is often derived from quartz or sand.
- Alumina (Al₂O₃): Alumina is added to enhance the strength, thermal stability, and resistance to wear and corrosion in ceramics.
- Other Minerals: Depending on the application, other minerals like feldspar, talc, or zirconia may be included to modify properties such as melting point, color, or electrical conductivity.
-
Processing of Raw Materials:
- Mining and Purification: Raw materials are extracted from natural deposits and then purified to remove impurities that could affect the quality of the ceramic.
- Grinding and Milling: The purified materials are ground into fine powders. The particle size distribution is critical, as it affects the packing density and sintering behavior during firing.
- Mixing: Different powders are mixed in specific proportions to achieve the desired composition and properties. Additives like binders or plasticizers may be included to aid in shaping.
-
Types of Ceramic Powders:
- Traditional Ceramics: Used in pottery, tiles, and bricks, these powders typically contain a higher proportion of clay and silica.
- Advanced Ceramics: These are engineered for specific applications, such as in electronics, aerospace, or biomedical fields. They often contain high-purity alumina, zirconia, or silicon carbide.
- Industrial Ceramics: Designed for high-performance applications, these powders may include specialized additives to enhance properties like thermal shock resistance or electrical insulation.
-
Shaping and Firing:
- Shaping: The ceramic powder is formed into the desired shape using techniques like pressing, extrusion, or slip casting.
- Firing: The shaped ceramic is heated to high temperatures in a kiln. During this process, the particles sinter together, forming a dense, solid structure. The firing temperature and atmosphere are carefully controlled to achieve the desired properties.
-
Applications of Ceramic Powders:
- Construction: Used in bricks, tiles, and cement.
- Electronics: Essential for components like insulators, capacitors, and substrates.
- Biomedical: Used in dental implants, bone substitutes, and surgical tools.
- Aerospace: High-performance ceramics are used in turbine blades, heat shields, and other critical components.
-
Customization of Ceramic Powders:
- Particle Size: Finer powders can lead to stronger ceramics, while coarser powders may be used for specific textures or properties.
- Additives: Various additives can be included to modify properties such as color, thermal conductivity, or mechanical strength.
- Composition: The ratio of different components can be adjusted to tailor the ceramic for specific applications, such as increasing alumina content for higher thermal resistance.
By understanding the composition and processing of ceramic powders, manufacturers can tailor the materials to meet the specific needs of various industries, ensuring optimal performance and durability in the final product.
Summary Table:
Aspect | Details |
---|---|
Primary Components | Clay, Silica (SiO₂), Alumina (Al₂O₃), and other minerals (e.g., feldspar, zirconia) |
Processing Steps | Mining, purification, grinding, milling, mixing, shaping, and firing |
Types of Ceramics | Traditional, Advanced, Industrial |
Applications | Construction, Electronics, Biomedical, Aerospace |
Customization | Particle size, additives, and composition tailored for specific needs |
Need high-quality ceramic powders for your industry? Contact our experts today to find the perfect solution!