A colloidal mill is a specialized piece of equipment widely used in the pharmaceutical industry for particle size reduction, dispersion, and homogenization of materials. It operates on the rotor-stator principle, where a rapidly rotating rotor and a static stator create a shear force that grinds, emulsifies, and disperses solid materials into a liquid medium. This process is essential for preparing colloidal dispersions, suspensions, emulsions, and ointments, which are critical in pharmaceutical formulations. The colloidal mill is highly efficient, capable of achieving superfine grinding and simultaneous emulsification in a single process cycle. It is versatile, suitable for small, medium, and large-scale production, and is also used in laboratories for research and development purposes.
Key Points Explained:
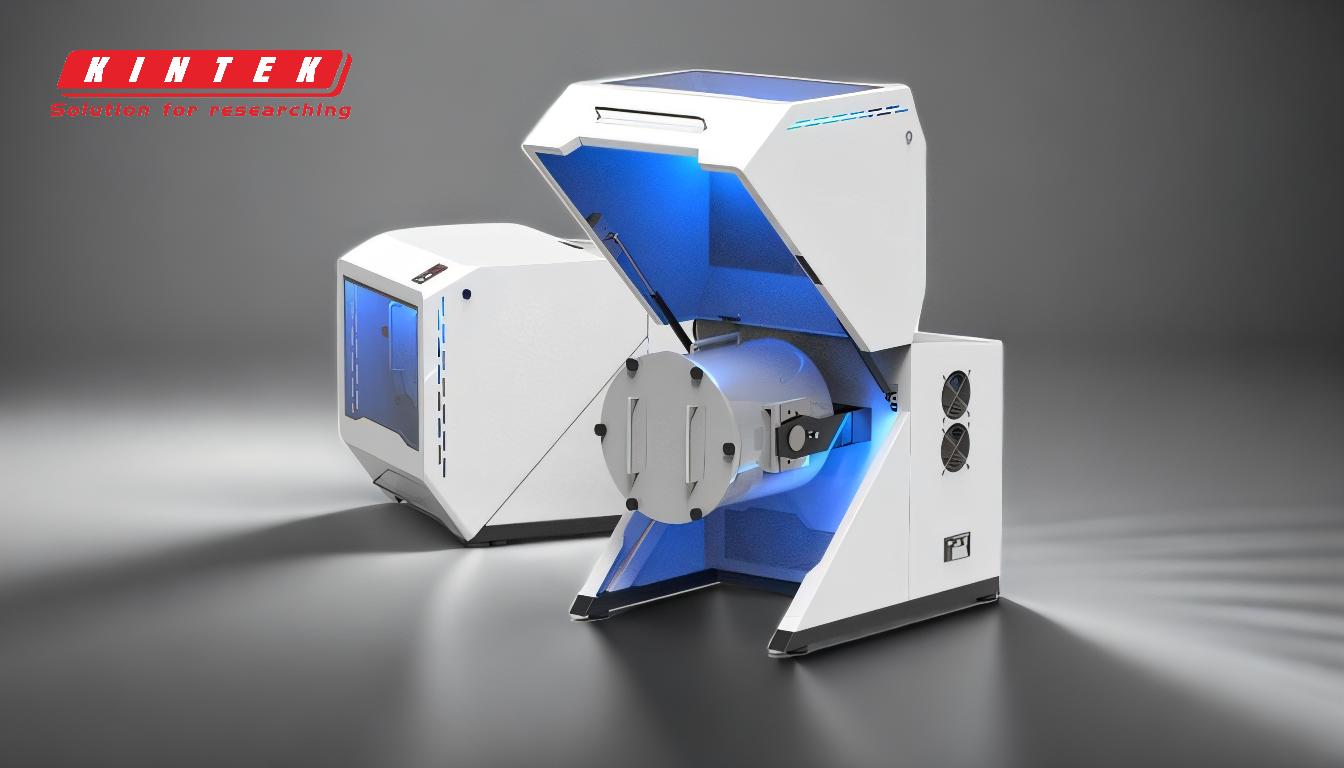
-
Function and Principle of Operation:
- The colloidal mill operates on the rotor-stator principle, where a high-speed rotor and a stationary stator create a narrow gap. This gap generates intense shear forces that grind, disperse, and homogenize materials.
- It is designed for particle size reduction of solid materials into a liquid state, making it ideal for processing highly viscous materials.
- The mill achieves superfine grinding, emulsification, and homogenization in a single process cycle, ensuring efficient and uniform results.
-
Applications in the Pharmaceutical Industry:
- The colloidal mill is primarily used for preparing colloidal dispersions, suspensions, emulsions, and ointments. These formulations are essential for drug delivery systems, ensuring consistent particle size and stability.
- It is also used in tablet batching systems for small, medium, and large-scale production, making it a versatile tool for pharmaceutical manufacturing.
- The mill is suitable for processing materials that are not easily moistened by the dispersion medium, which is critical for creating stable pharmaceutical suspensions.
-
Versatility Across Industries:
- Beyond pharmaceuticals, the colloidal mill is used in the food and beverage industry for homogenizing and emulsifying products like sauces, dressings, and dairy items.
- It is also employed in the chemical industry for creating stable dispersions and emulsions of various chemical compounds.
- Its ability to handle highly viscous materials makes it a valuable tool across multiple sectors.
-
Laboratory Use and Research:
- The Lab Colloid Mill is a smaller, compact version designed for research and development (R&D) purposes. It is also known as the R&D Colloid Mill, Mini Colloid Mill, or Compact Colloid Mill.
- It is used in laboratories to develop new formulations, test material properties, and optimize processes before scaling up to industrial production.
-
Advantages of Colloidal Mills:
- Efficiency: The colloidal mill is highly efficient, capable of achieving superfine grinding and simultaneous emulsification in a single process cycle.
- Scalability: It is suitable for small, medium, and large-scale production, making it a versatile choice for pharmaceutical manufacturers.
- Uniformity: The mill ensures consistent particle size and dispersion, which is critical for the stability and efficacy of pharmaceutical formulations.
- Ease of Use: The design of the colloidal mill allows for easy operation and maintenance, reducing downtime and improving productivity.
-
Key Components and Design Features:
- Rotor and Stator: The core components of the colloidal mill, the rotor and stator, are designed to create a narrow gap that generates shear forces for grinding and dispersion.
- Material of Construction: Colloidal mills are typically made from stainless steel or other corrosion-resistant materials to ensure durability and compliance with pharmaceutical standards.
- Adjustable Gap: Some models feature an adjustable gap between the rotor and stator, allowing for precise control over the grinding and dispersion process.
-
Considerations for Equipment Purchasers:
- Scale of Production: Purchasers should consider whether they need a lab-scale mill for R&D or an industrial-scale mill for large-scale production.
- Material Compatibility: The mill should be compatible with the types of materials being processed, including highly viscous or abrasive substances.
- Ease of Cleaning and Maintenance: Pharmaceutical-grade mills should be easy to clean and maintain to ensure compliance with hygiene and safety standards.
- Regulatory Compliance: The mill should meet industry standards and regulations, such as those set by the FDA or other regulatory bodies.
In summary, the colloidal mill is a critical piece of equipment in the pharmaceutical industry, offering efficient particle size reduction, dispersion, and homogenization. Its versatility, scalability, and ability to handle a wide range of materials make it an indispensable tool for pharmaceutical manufacturers and researchers alike.
Summary Table:
Aspect | Details |
---|---|
Function | Particle size reduction, dispersion, and homogenization of materials. |
Principle | Rotor-stator mechanism generating intense shear forces. |
Applications | Colloidal dispersions, suspensions, emulsions, ointments, tablet batching. |
Industries | Pharmaceuticals, food and beverage, chemical industries. |
Advantages | Efficiency, scalability, uniformity, ease of use. |
Key Components | Rotor, stator, adjustable gap, corrosion-resistant materials. |
Considerations | Scale of production, material compatibility, ease of cleaning, compliance. |
Ready to enhance your pharmaceutical processes? Contact us today to find the perfect colloidal mill for your needs!