Mold filling is a critical process in manufacturing, particularly in industries like plastics, rubber, and metal casting, where liquid or semi-liquid materials are injected into a mold cavity to form a specific shape. During this process, the material undergoes a chemical reaction, such as gelling or vulcanization, under controlled pressure and temperature. The injected material displaces the air within the mold, ensuring the final product is free of voids or defects. This process is essential for achieving precise dimensions, surface finish, and structural integrity in the manufactured part.
Key Points Explained:
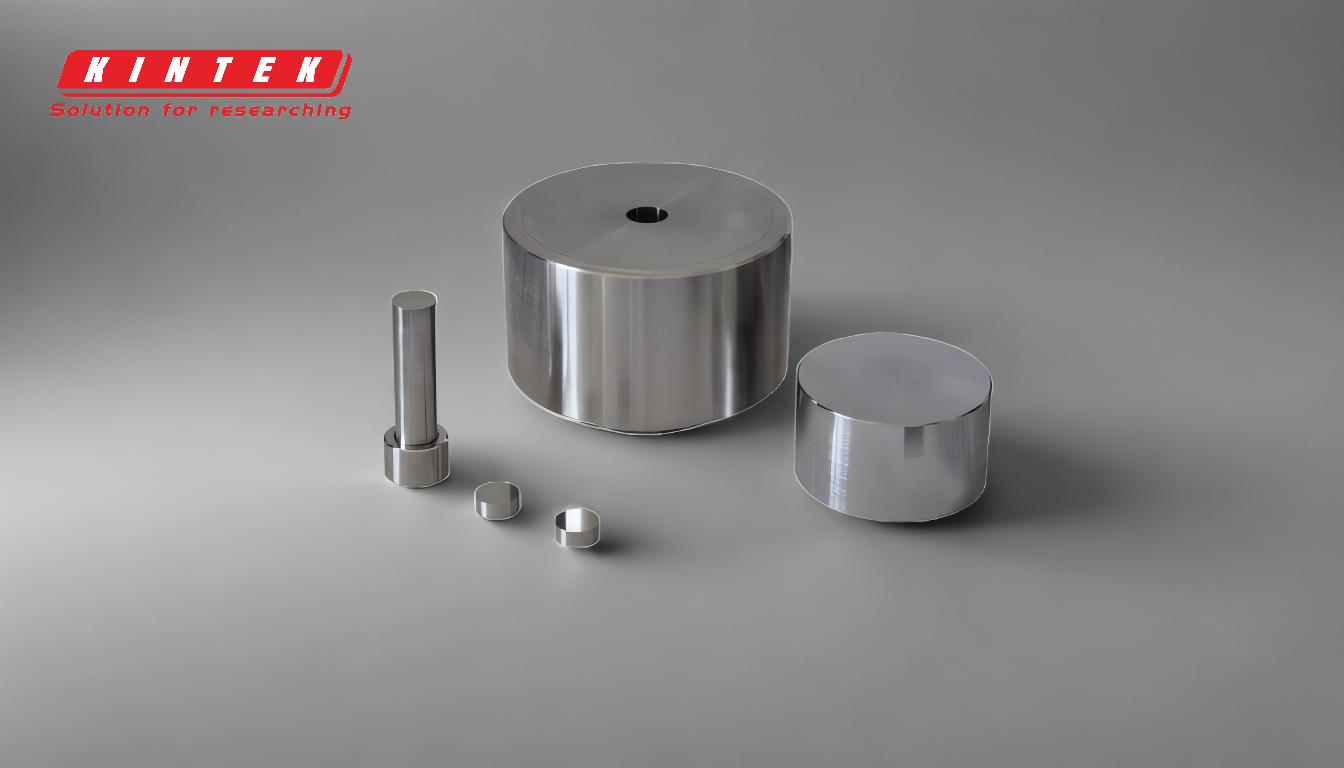
-
Definition of Mold Filling
- Mold filling refers to the process of injecting a liquid or semi-liquid material (such as molten plastic, rubber, or metal) into a mold cavity.
- The material takes the shape of the mold as it solidifies or cures, forming the desired product.
-
Chemical Reactions During Mold Filling
- The material undergoes a chemical reaction, such as gelling (for plastics) or vulcanization (for rubber), within the mold.
- These reactions are typically activated by heat and pressure, ensuring the material hardens or cures properly.
-
Role of Pressure and Temperature
- Pressure ensures the material fully fills the mold cavity, including intricate details and thin sections.
- Temperature controls the rate of the chemical reaction, ensuring the material cures uniformly and achieves the desired mechanical properties.
-
Displacement of Air
- As the material is injected, it displaces the air inside the mold cavity.
- Proper air displacement is crucial to prevent defects like air pockets, voids, or incomplete filling.
-
Applications of Mold Filling
- Widely used in industries such as automotive (for rubber seals, gaskets), consumer goods (plastic containers), and aerospace (composite materials).
- Enables the production of complex shapes with high precision and repeatability.
-
Importance of Mold Design
- The mold must be designed to facilitate smooth material flow and proper air evacuation.
- Features like vents or air channels are often incorporated to ensure complete filling and minimize defects.
-
Challenges in Mold Filling
- Incomplete filling can occur if the material viscosity is too high or if the injection pressure is insufficient.
- Air entrapment or uneven curing can lead to defects, requiring careful control of process parameters.
-
Advantages of Mold Filling
- High production efficiency and repeatability.
- Ability to produce complex geometries with tight tolerances.
- Suitable for a wide range of materials, including thermoplastics, thermosets, and elastomers.
By understanding these key aspects, equipment and consumable purchasers can make informed decisions about mold design, material selection, and process optimization to achieve high-quality manufactured parts.
Summary Table:
Key Aspect | Description |
---|---|
Definition | Injection of liquid/semi-liquid material into a mold cavity to form a shape. |
Chemical Reactions | Gelling (plastics) or vulcanization (rubber) under heat and pressure. |
Pressure & Temperature | Ensures complete filling and uniform curing for precise mechanical properties. |
Air Displacement | Prevents voids and defects by displacing air during injection. |
Applications | Automotive, consumer goods, aerospace, and more. |
Mold Design | Facilitates material flow and air evacuation for defect-free products. |
Challenges | Incomplete filling, air entrapment, and uneven curing. |
Advantages | High efficiency, repeatability, and ability to produce complex geometries. |
Optimize your manufacturing process with expert mold filling solutions—contact us today!