One of the significant disadvantages of the ball mill method is its high energy consumption, which arises from factors such as wear of grinding balls and wall armor, friction, and material heating. This not only increases operational costs but also necessitates frequent maintenance due to equipment wear. Additionally, the process generates heat, which can cause thermal damage to materials, affecting their quality. The high-speed rotation of the mill also produces loud noise, making it less suitable for environments where noise pollution is a concern. These drawbacks make the ball mill method less efficient and more costly compared to some alternative grinding methods.
Key Points Explained:
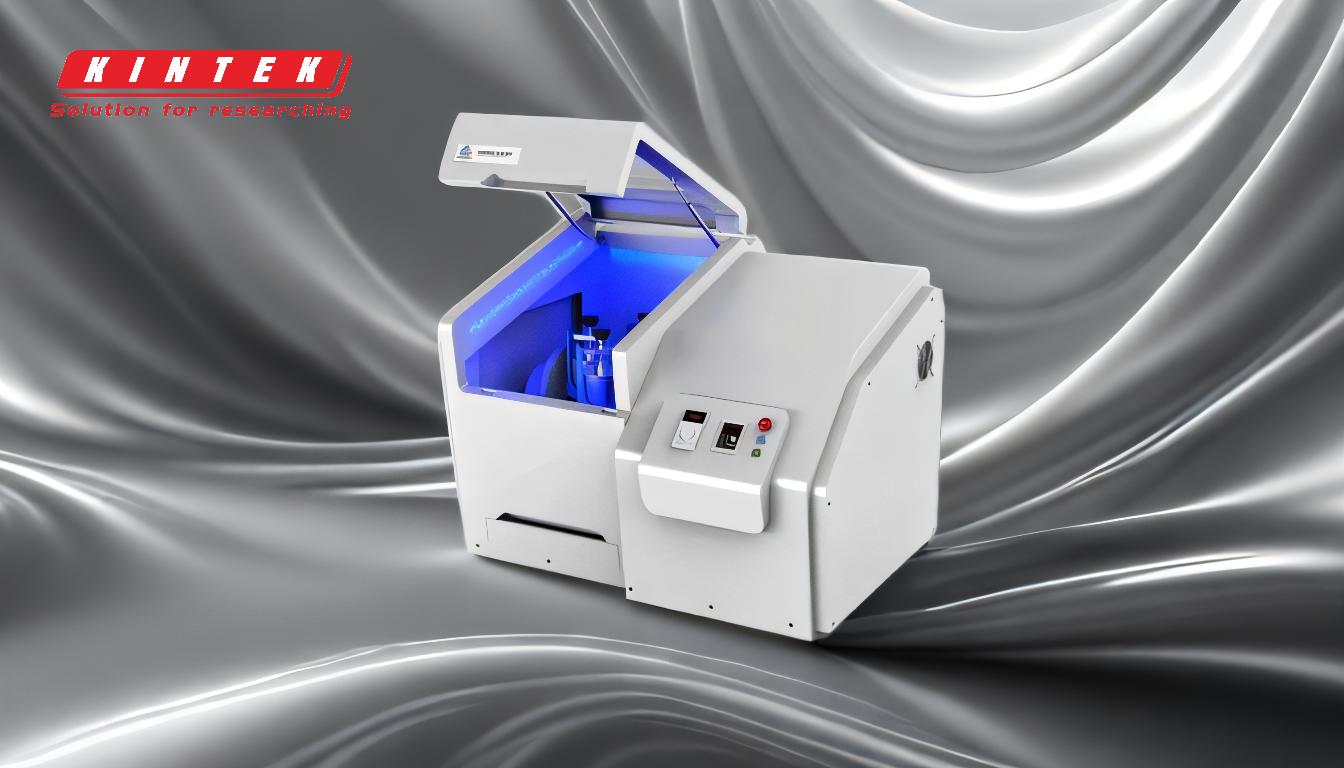
-
High Energy Consumption:
- The ball mill method requires a significant amount of energy to operate, primarily due to the wear of grinding balls and wall armor, friction between materials, and heat generation.
- This high energy demand increases operational costs, making the method less economical for large-scale or continuous use.
- Energy management becomes crucial, as inefficient energy use can further escalate costs.
-
Equipment Wear and Maintenance:
- The friction between the grinding medium (balls) and the material being processed leads to significant wear and tear on the equipment.
- This wear necessitates frequent replacement of parts, such as grinding balls and wall armor, increasing maintenance costs and downtime.
- The wear also raises the risk of contamination, as particles from the worn-out components can mix with the material being processed.
-
Thermal Damage to Materials:
- The heat generated during the grinding process can cause thermal damage to sensitive materials, altering their properties and reducing the quality of the final product.
- This is particularly problematic for materials that are heat-sensitive or require precise control over their thermal history.
-
Noise Pollution:
- The high-speed rotation of the ball mill generates loud noise during operation, which can be a significant drawback in environments where noise pollution is a concern.
- While the use of rubber balls can reduce noise to some extent, it does not eliminate the problem entirely.
-
Limited Capacity for Large Quantities:
- Ball mills have a limited capacity for handling large quantities of material, which can be a disadvantage in industrial settings where high throughput is required.
- This limitation can lead to inefficiencies and increased costs when scaling up production.
-
Inability to Process Certain Materials:
- Ball mills are not suitable for reducing soft, tacky, or fibrous materials, limiting their applicability in certain industries.
- This restricts the versatility of the ball mill method and may necessitate the use of alternative grinding methods for specific materials.
By understanding these key points, equipment and consumable purchasers can make more informed decisions about whether the ball mill method is suitable for their specific needs, considering factors such as material properties, operational costs, and environmental impact.
Summary Table:
Disadvantage | Description |
---|---|
High Energy Consumption | Significant energy use due to wear, friction, and heat generation. |
Equipment Wear and Maintenance | Frequent replacement of parts increases costs and downtime. |
Thermal Damage to Materials | Heat can alter material properties, reducing product quality. |
Noise Pollution | Loud operation makes it unsuitable for noise-sensitive environments. |
Limited Capacity | Inefficient for large-scale production, increasing operational costs. |
Inability to Process Certain Materials | Not suitable for soft, tacky, or fibrous materials, limiting versatility. |
Need a better grinding solution? Contact our experts today to explore alternatives tailored to your needs!