Pre-sintered zirconia is a partially sintered form of zirconia ceramic used in dental and industrial applications. It is created by pressing a slurry of zirconium oxide, yttrium oxide, and other compounds into blocks or disks at room temperature, resulting in a soft and malleable material with 40-50% of its theoretical maximum density. Pre-sintered zirconia is easier to mill and shape than fully sintered zirconia but requires a subsequent sintering process to achieve maximum strength and durability. During sintering, the material undergoes significant shrinkage, reducing porosity and improving density, which enhances its mechanical properties. This intermediate state allows for easier machining while still enabling the final product to achieve the high strength and resistance to hydrothermal aging characteristic of fully sintered zirconia.
Key Points Explained:
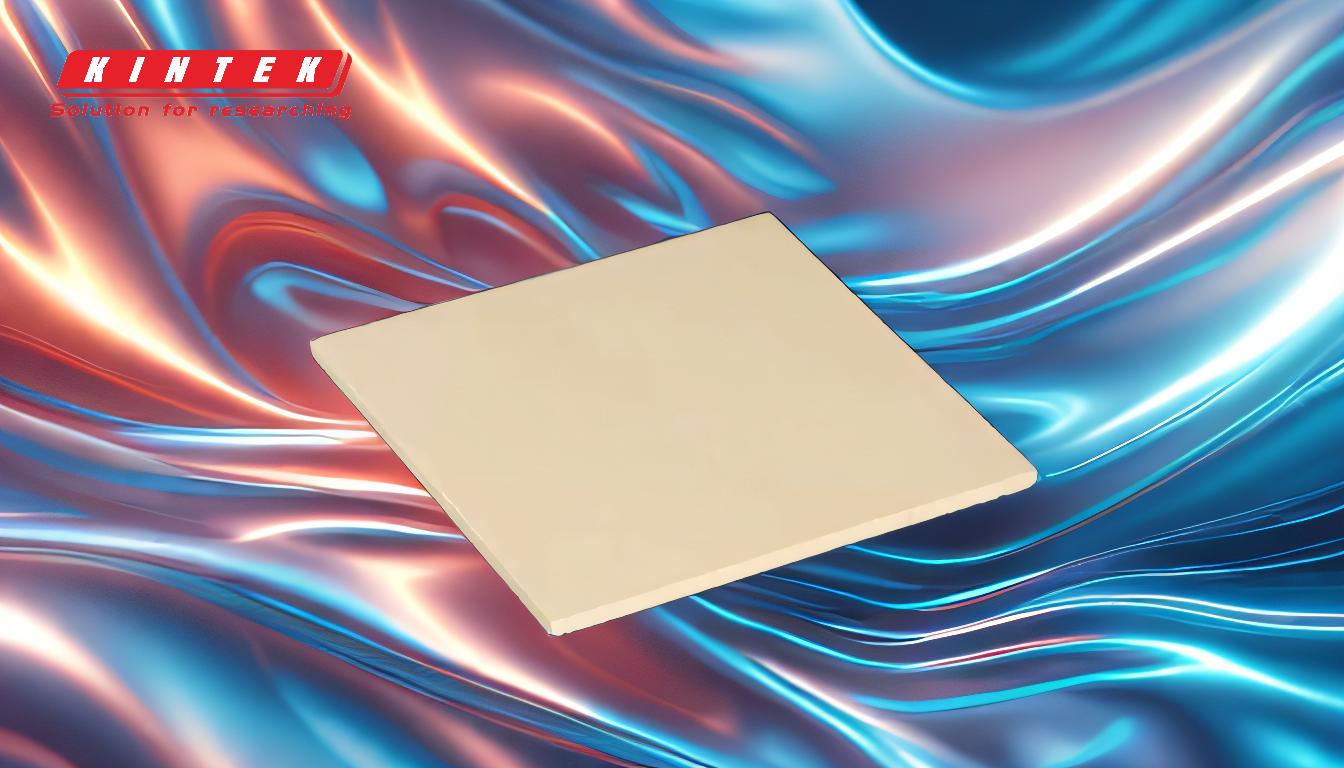
-
Definition and Composition of Pre-Sintered Zirconia:
- Pre-sintered zirconia is a partially sintered ceramic material made from a slurry of zirconium oxide, yttrium oxide, hafnium oxide, aluminum oxide, and trace compounds.
- It is pressed into blocks, cylinders, or disks at room temperature, resulting in a soft and malleable form with a density of 40-50% of its theoretical maximum.
-
Ease of Machining:
- Pre-sintered zirconia is easier to mill and shape compared to fully sintered zirconia due to its lower density and softer structure.
- This property makes it more suitable for complex dental restorations or industrial components that require precise shaping.
-
Sintering Process:
- After milling, pre-sintered zirconia must undergo a sintering process to achieve its final properties.
- Sintering involves heating the material to high temperatures (1,100°C to 1,200°C), often with applied pressure, to reduce porosity and increase density.
- During sintering, zirconia transforms from a monoclinic to a polytetragonal crystalline structure, becoming extremely hard and dense.
-
Shrinkage During Sintering:
- Pre-sintered zirconia undergoes significant shrinkage during sintering, which must be accounted for during the design and milling stages.
- This shrinkage ensures the final product achieves its desired dimensions and mechanical properties.
-
Advantages Over Fully Sintered Zirconia:
- Pre-sintered zirconia is easier to machine, reducing wear on milling tools and shortening processing times.
- It allows for more intricate designs and adjustments before the final sintering stage.
-
Limitations of Pre-Sintered Zirconia:
- Pre-sintered zirconia lacks the full strength and hydrothermal aging resistance of fully sintered zirconia until it undergoes the sintering process.
- The need for a high-temperature sintering furnace adds an extra step to the production process.
-
Applications:
- Pre-sintered zirconia is widely used in dental restorations, such as crowns, bridges, and implants, due to its biocompatibility and ease of shaping.
- It is also used in industrial applications requiring high-strength ceramic components.
-
Comparison with Fully Sintered Zirconia:
- Fully sintered zirconia has greater strength, lower porosity, and better resistance to hydrothermal aging but is harder to machine and causes rapid tool wear.
- Pre-sintered zirconia offers a balance between machinability and final performance, making it a preferred choice for many applications.
By understanding these key points, purchasers and users of pre-sintered zirconia can make informed decisions about its suitability for specific applications and the necessary processing steps to achieve optimal results.
Summary Table:
Aspect | Details |
---|---|
Composition | Zirconium oxide, yttrium oxide, hafnium oxide, aluminum oxide, trace compounds |
Density | 40-50% of theoretical maximum |
Machining Ease | Easier to mill and shape than fully sintered zirconia |
Sintering Temperature | 1,100°C to 1,200°C |
Shrinkage | Significant shrinkage during sintering |
Applications | Dental restorations (crowns, bridges, implants), industrial components |
Advantages | Easier machining, intricate designs, balance of machinability and strength |
Limitations | Requires sintering for full strength, extra production step |
Discover how pre-sintered zirconia can enhance your dental or industrial projects—contact us today for expert guidance!