PVD (Physical Vapor Deposition) coatings are generally considered safe once applied, as the particles are firmly bonded to the substrate and do not pose a risk of becoming airborne. However, during the application process, the particles can be harmful if inhaled, necessitating proper safety precautions. PVD coatings are known for their durability, corrosion resistance, and environmental friendliness compared to traditional coating methods. They are widely used in industries such as automotive, aerospace, and medical due to their high hardness, wear resistance, and low friction properties. Below, we explore the toxicity concerns, safety measures, and environmental benefits of PVD coatings in detail.
Key Points Explained:
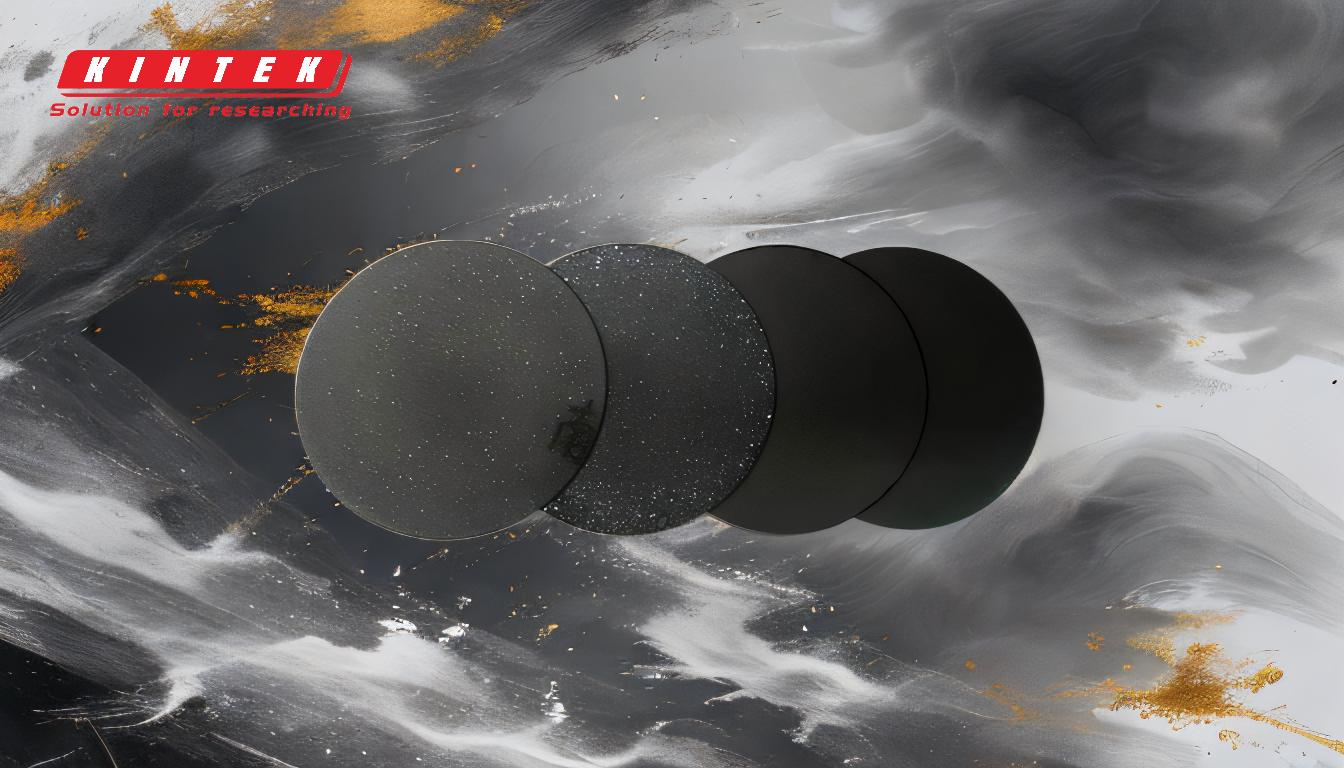
-
Toxicity During Application:
- Risk of Inhalation: During the PVD coating process, fine particles or vapors of the coating material (e.g., titanium, chromium, or aluminum) are generated. Inhaling these particles can be harmful to human health, potentially causing respiratory issues or other complications.
- Safety Precautions: To mitigate risks, proper ventilation, personal protective equipment (PPE) such as masks, and adherence to safety protocols are essential during the application phase.
-
Safety Post-Application:
- Firm Bonding: Once the PVD coating is applied, the particles are firmly bonded to the substrate material, making them stable and non-toxic. The coatings are extremely thin (0.5 to 5 microns) and do not flake or become airborne under normal conditions.
- No Inhalation Risk: After application, the coatings pose no risk of inhalation or exposure, making them safe for use in various applications, including medical implants and consumer products.
-
Environmental Friendliness:
- Reduced Toxic Substances: PVD is considered environmentally friendly compared to traditional "wet" coating processes, as it minimizes the use of toxic chemicals and solvents.
- Clean and Durable Coatings: PVD coatings are pure, clean, and durable, making them ideal for industries requiring high standards of hygiene and performance, such as the medical and surgical implant industry.
-
Applications and Benefits:
- Wear and Corrosion Resistance: PVD coatings are highly resistant to wear, corrosion, and oxidation, making them suitable for demanding applications in automotive, aerospace, and industrial machinery.
- Aesthetic and Functional Properties: These coatings enhance the aesthetic appearance of materials while improving functional properties like hardness and friction reduction.
-
Comparison with Other Coating Methods:
- Advantages Over Wet Processes: Unlike traditional electroplating or chemical vapor deposition (CVD), PVD does not involve hazardous chemicals or produce toxic byproducts, making it a cleaner and safer alternative.
- Precision and Thinness: PVD coatings are extremely thin and precise, allowing for replication of original finishes with minimal material usage.
In summary, while PVD coatings are not inherently toxic, precautions must be taken during the application process to prevent inhalation of particles. Once applied, the coatings are safe, durable, and environmentally friendly, making them a preferred choice for high-performance and medical applications.
Summary Table:
Aspect | Details |
---|---|
Toxicity During Application | Inhalation risks exist; PPE and ventilation are essential. |
Safety Post-Application | Coatings are non-toxic and firmly bonded; no inhalation risk. |
Environmental Friendliness | Minimizes toxic chemicals; cleaner than traditional methods. |
Applications | Automotive, aerospace, medical, and industrial machinery. |
Benefits | High wear resistance, corrosion resistance, and low friction. |
Discover how PVD coatings can enhance your projects—contact us today for expert advice!