Radio Frequency (RF) sputtering is a thin-film deposition technique widely used in industries such as semiconductors and computing. It involves the use of radio frequency power, typically at 13.56 MHz, to create a plasma in a vacuum chamber filled with an inert gas. The process alternates the electrical potential between the target material (cathode) and the substrate holder (anode), allowing for the deposition of both conductive and insulating materials. The alternating potential prevents charge buildup on the target, which is particularly useful for sputtering non-conductive materials. During the positive cycle, electrons are attracted to the target, creating a negative bias, while in the negative cycle, ion bombardment continues, ejecting target atoms that form a thin film on the substrate.
Key Points Explained:
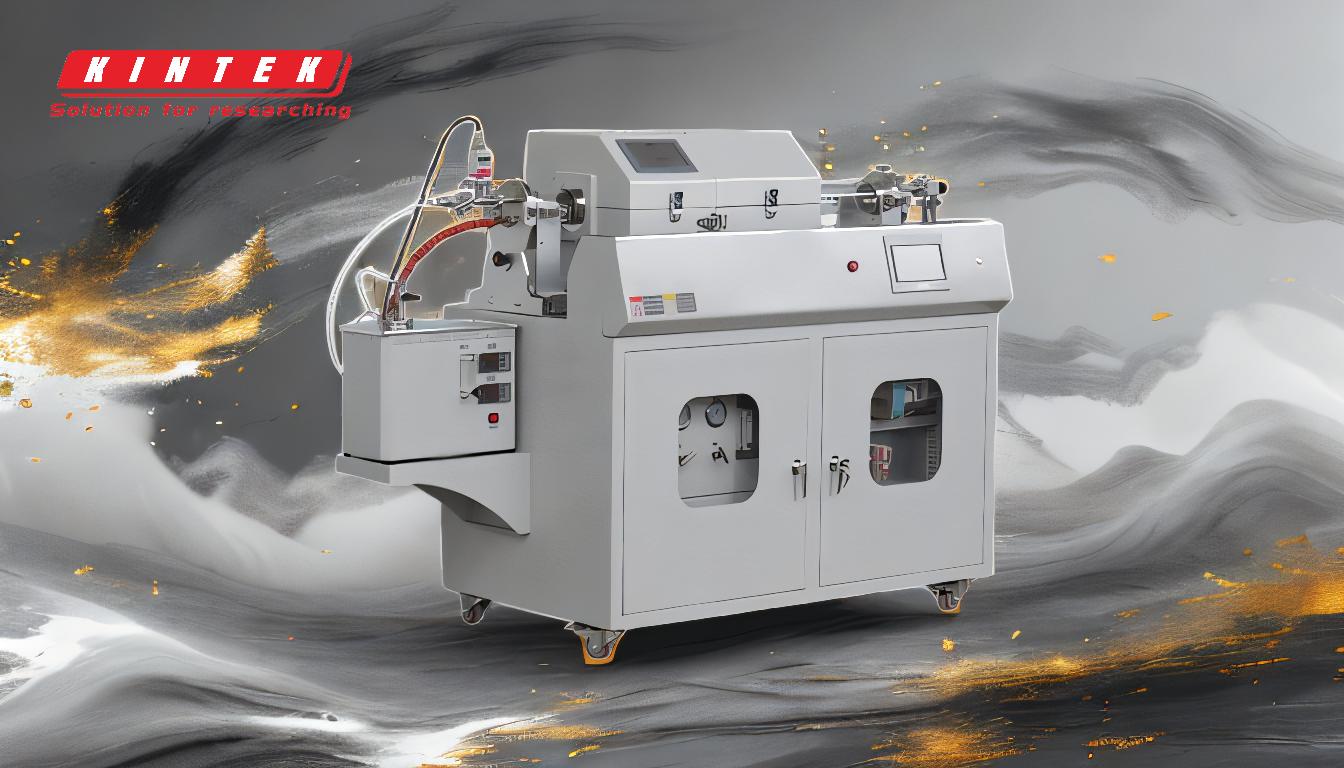
-
Basic Principle of RF Sputtering:
- RF sputtering uses radio frequency power to create a plasma in a vacuum chamber filled with an inert gas.
- The target material and substrate holder act as electrodes, with the electrical potential alternating between them.
- This alternating potential prevents charge buildup on the target, which is crucial for sputtering insulating materials.
-
Cycles in RF Sputtering:
- Positive Cycle: Electrons are attracted to the target, giving it a negative bias. This helps to clean the target surface of any charge buildup.
- Negative Cycle: Ion bombardment of the target continues, ejecting atoms from the target material. These atoms then form a thin film on the substrate.
-
Advantages of RF Sputtering:
- Deposition of Insulating Materials: RF sputtering is particularly effective for depositing non-conductive materials, as the alternating potential prevents charge buildup that could otherwise stop the sputtering process.
- Prevention of Arcing: By avoiding a constant negative voltage on the cathode, RF sputtering prevents arcing into the plasma, which can cause quality control issues in thin films.
-
Role of Inert Gas and Plasma:
- An inert gas, such as argon, is introduced into the vacuum chamber.
- The radio frequency power ionizes the gas, creating a plasma. High-energy ions from the plasma bombard the target material, sputtering off atoms that form a fine spray covering the substrate.
-
RF Magnetron Sputtering:
- A variant of RF sputtering, RF magnetron sputtering uses magnets to trap electrons over the target material.
- This increases the ionization of the gas and allows for faster deposition rates, making it more efficient for certain applications.
-
Applications of RF Sputtering:
- Semiconductor Industry: RF sputtering is used to deposit thin films of insulating materials in the production of semiconductors.
- Computing Industry: It is also used in the manufacturing of computer components, where thin films are essential for device performance.
-
Technical Considerations:
- Frequency: The typical frequency used in RF sputtering is 13.56 MHz, which is a standard frequency for industrial, scientific, and medical (ISM) applications.
- Matching Network: A matching network is used to ensure efficient power transfer from the RF generator to the plasma, optimizing the sputtering process.
By understanding these key points, one can appreciate the complexity and utility of RF sputtering in modern manufacturing and research. The technique's ability to handle both conductive and insulating materials makes it a versatile tool in the creation of thin films for various high-tech applications.
Summary Table:
Key Aspect | Details |
---|---|
Basic Principle | Uses RF power to create plasma; alternates electrical potential to prevent charge buildup. |
Cycles | Positive cycle: cleans target surface. Negative cycle: ejects atoms for deposition. |
Advantages | Deposits insulating materials; prevents arcing for high-quality thin films. |
Role of Inert Gas & Plasma | Argon gas ionized by RF power creates plasma for sputtering target atoms. |
RF Magnetron Sputtering | Uses magnets to trap electrons, increasing ionization and deposition rates. |
Applications | Semiconductors, computing, and other high-tech industries. |
Technical Considerations | Operates at 13.56 MHz; uses a matching network for efficient power transfer. |
Ready to enhance your thin-film deposition process? Contact our experts today to learn more about RF sputtering solutions!