Rotary extraction is a process used in various industries to separate components from a mixture using rotational force. It is commonly employed in applications such as oil extraction, chemical processing, and environmental remediation. The technique involves rotating a mixture at high speeds, which creates centrifugal force, causing denser components to move outward while lighter components remain closer to the center. This separation allows for efficient extraction of desired materials. Rotary extraction is valued for its ability to handle large volumes, achieve high purity levels, and operate continuously, making it a versatile and effective method for industrial and scientific applications.
Key Points Explained:
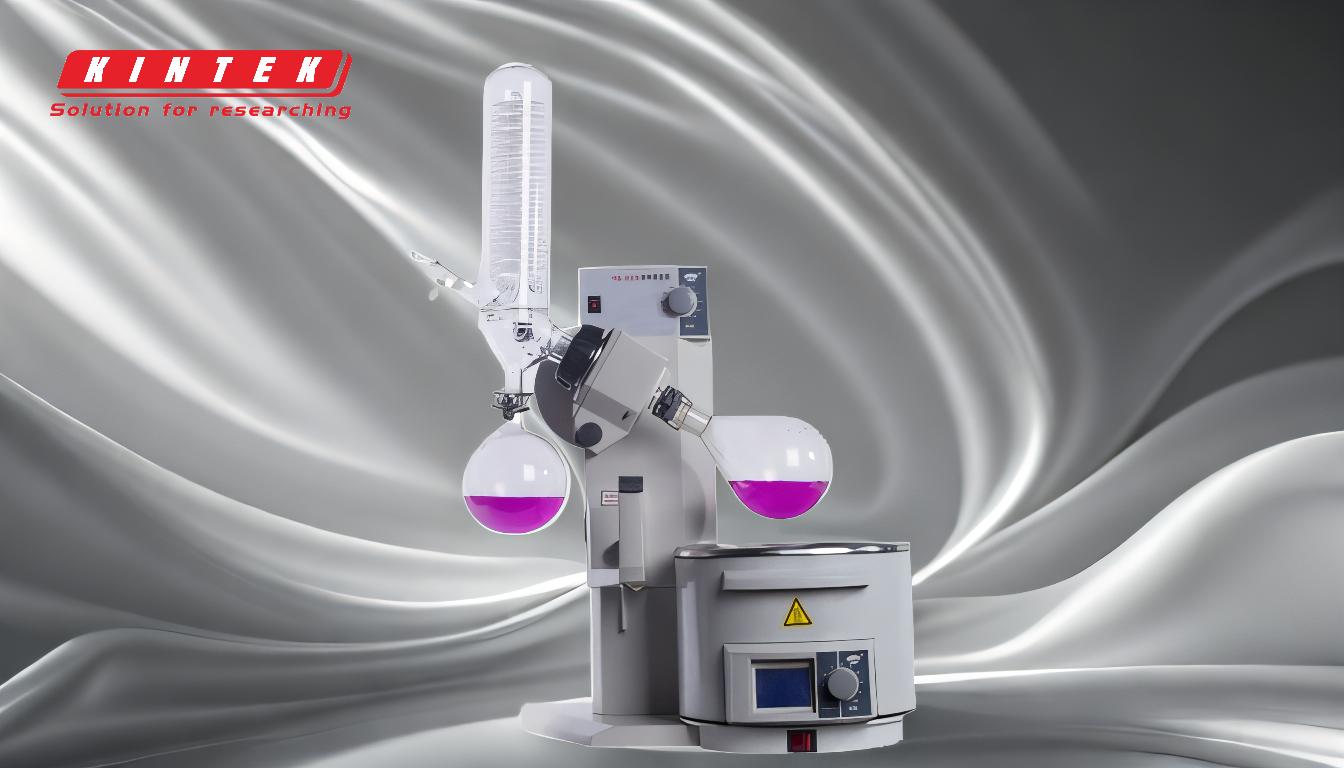
-
Definition of Rotary Extraction:
- Rotary extraction is a mechanical separation process that uses centrifugal force to separate components of a mixture based on their densities. The process involves rotating the mixture at high speeds, which forces denser materials to the outer edges while lighter materials remain near the center.
-
Mechanism of Rotary Extraction:
- The core mechanism relies on centrifugal force, which is generated by the rotational motion of the mixture. This force acts outward from the center of rotation, causing denser particles or liquids to migrate to the periphery, while less dense components stay closer to the axis of rotation. This separation is facilitated by the design of the rotary extractor, which often includes specialized chambers or discs to enhance the process.
-
Applications of Rotary Extraction:
- Oil and Gas Industry: Used for separating crude oil from water and other impurities.
- Chemical Processing: Employed to isolate specific chemicals or compounds from mixtures.
- Environmental Remediation: Utilized to remove contaminants from soil or water.
- Food and Beverage Industry: Applied in processes like juice extraction or oil separation from seeds.
-
Advantages of Rotary Extraction:
- High Efficiency: Capable of processing large volumes of material quickly.
- Continuous Operation: Suitable for industrial applications requiring non-stop processing.
- High Purity Levels: Achieves effective separation, resulting in high-purity end products.
- Versatility: Can be adapted for various materials and industries.
-
Types of Rotary Extractors:
- Centrifugal Extractors: Use high-speed rotation to separate liquids of different densities.
- Rotary Drum Filters: Employ rotating drums to filter solids from liquids.
- Decanter Centrifuges: Combine rotation and sedimentation to separate solids from liquids.
-
Considerations for Equipment Selection:
- Material Compatibility: Ensure the extractor materials are compatible with the substances being processed.
- Speed and Force Requirements: Select equipment that can generate the necessary centrifugal force for effective separation.
- Capacity and Throughput: Choose a system that matches the volume and flow rate requirements of the application.
- Maintenance and Durability: Consider the ease of maintenance and the durability of the equipment for long-term use.
-
Challenges and Limitations:
- Energy Consumption: High-speed rotation can be energy-intensive.
- Equipment Cost: Advanced rotary extraction systems may require significant investment.
- Complexity: Some applications may require specialized knowledge to operate and maintain the equipment effectively.
-
Future Trends in Rotary Extraction:
- Automation: Increasing use of automated systems for better control and efficiency.
- Sustainability: Development of energy-efficient and environmentally friendly extraction methods.
- Advanced Materials: Use of new materials to improve the durability and performance of rotary extractors.
By understanding these key points, equipment and consumable purchasers can make informed decisions about the suitability of rotary extraction for their specific needs, ensuring optimal performance and cost-effectiveness.
Summary Table:
Key Aspect | Details |
---|---|
Definition | Mechanical separation using centrifugal force based on material densities. |
Mechanism | High-speed rotation forces denser materials outward, lighter ones inward. |
Applications | Oil extraction, chemical processing, environmental remediation, food industry. |
Advantages | High efficiency, continuous operation, high purity, versatility. |
Types of Extractors | Centrifugal extractors, rotary drum filters, decanter centrifuges. |
Equipment Selection | Material compatibility, speed, capacity, maintenance, and durability. |
Challenges | Energy consumption, equipment cost, operational complexity. |
Future Trends | Automation, sustainability, advanced materials for improved performance. |
Discover how rotary extraction can optimize your industrial processes—contact us today for expert guidance!