Sieving is a fundamental method used to separate particles of different sizes within a sample. It operates on the principle of relative motion between the sieve and the particles, enabling smaller particles to pass through the sieve mesh while larger particles are retained on the surface. This process is widely used in industries such as pharmaceuticals, food processing, and construction for quality control and material classification. By understanding the mechanics of sieving, one can optimize the process for efficiency and accuracy in particle separation.
Key Points Explained:
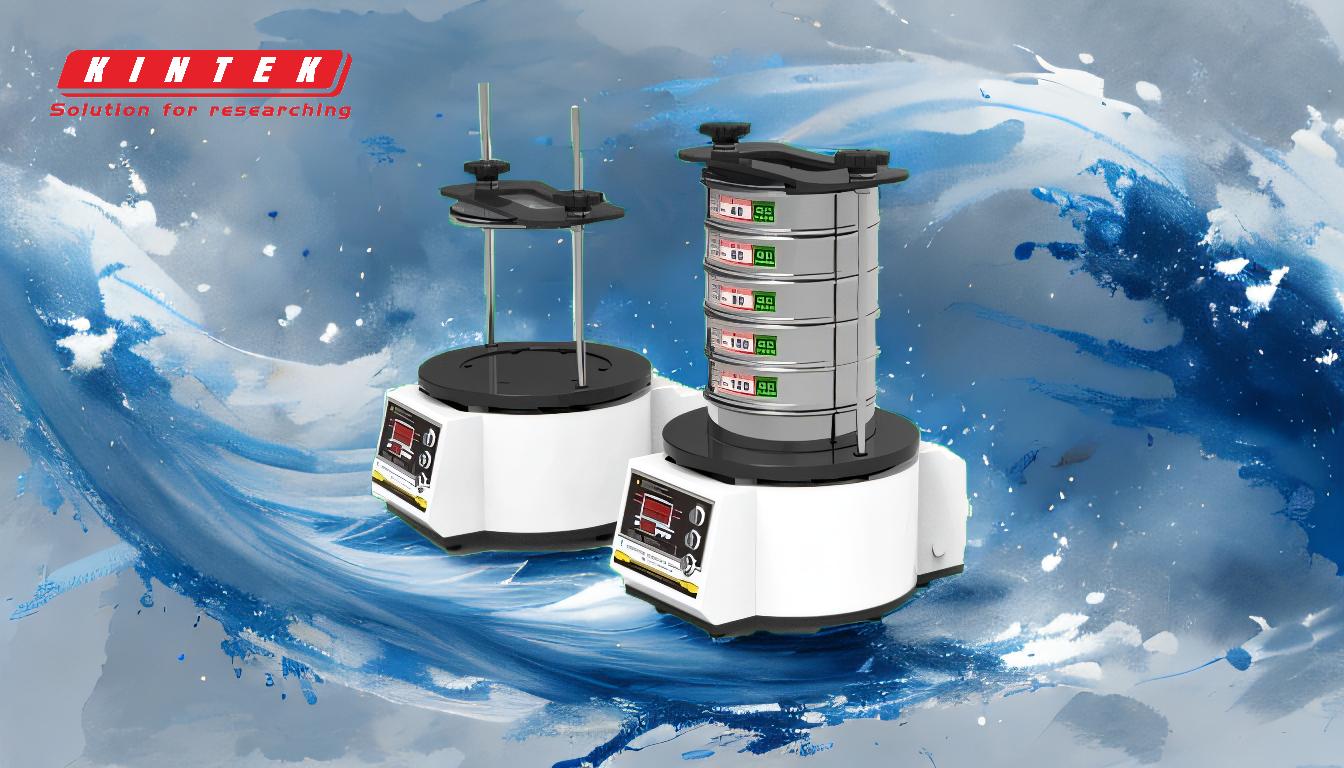
-
Definition of Sieving:
- Sieving is a physical separation technique used to classify particles based on their size.
- It involves passing a sample through a mesh or sieve with specific-sized openings.
-
Principle of Sieving:
- The sample is kept in motion (vertical or horizontal) during the process.
- This motion creates relative movement between the sieve and the particles.
- Smaller particles pass through the sieve mesh, while larger particles remain on the surface.
-
Components of a Sieving System:
- Sieve Mesh: The primary component with openings of a defined size.
- Sample Holder: A container or frame that holds the sieve and sample.
- Motion Mechanism: A device that provides the necessary motion (e.g., shaking, tapping, or vibrating).
-
Types of Sieving:
- Dry Sieving: Used for free-flowing, dry materials.
- Wet Sieving: Involves the use of water or other liquids to aid in the separation of fine particles.
- Air Jet Sieving: Utilizes air to assist in the separation of fine particles that may clog the mesh.
-
Applications of Sieving:
- Quality Control: Ensuring particle size distribution meets specifications.
- Material Classification: Separating materials into different size fractions for further processing.
- Research and Development: Analyzing particle size for product development.
-
Factors Affecting Sieving Efficiency:
- Mesh Size: The size of the openings in the sieve determines the size of particles that can pass through.
- Sample Characteristics: Particle shape, density, and moisture content can influence the sieving process.
- Motion Type and Intensity: The type and intensity of motion affect the rate and efficiency of particle separation.
-
Advantages of Sieving:
- Simple and cost-effective method for particle size analysis.
- Can be used for a wide range of materials and particle sizes.
- Provides quick results, making it suitable for routine quality control.
-
Limitations of Sieving:
- Limited to particles larger than the mesh size.
- May not be effective for materials with high moisture content or those that tend to agglomerate.
- Requires careful handling to avoid damage to the sieve mesh.
By understanding these key points, one can effectively utilize sieving as a tool for particle size analysis and material separation, ensuring optimal results in various applications.
Summary Table:
Aspect | Details |
---|---|
Definition | Physical separation technique to classify particles by size. |
Principle | Relative motion between sieve and particles; smaller particles pass through. |
Components | Sieve mesh, sample holder, motion mechanism. |
Types | Dry sieving, wet sieving, air jet sieving. |
Applications | Quality control, material classification, R&D. |
Efficiency Factors | Mesh size, sample characteristics, motion type and intensity. |
Advantages | Simple, cost-effective, quick results. |
Limitations | Limited to larger particles, ineffective for moist or agglomerated materials. |
Optimize your sieving process today—contact our experts for tailored solutions!