A small pilot-scale pyrolysis reactor is a compact, often batch-operated system designed for the thermal decomposition of organic materials at elevated temperatures in the absence of oxygen. It is used for research, development, and small-scale production, allowing for the testing of pyrolysis processes on a manageable scale. The reactor typically processes materials like biomass, tires, rubber, plastic, and oil sludge, converting them into valuable products such as liquid oil, combustible gas, and biochar. These reactors are smaller in size, have lower energy consumption, and are ideal for intermittent operation, making them suitable for laboratories, pilot projects, and small-scale industrial applications.
Key Points Explained:
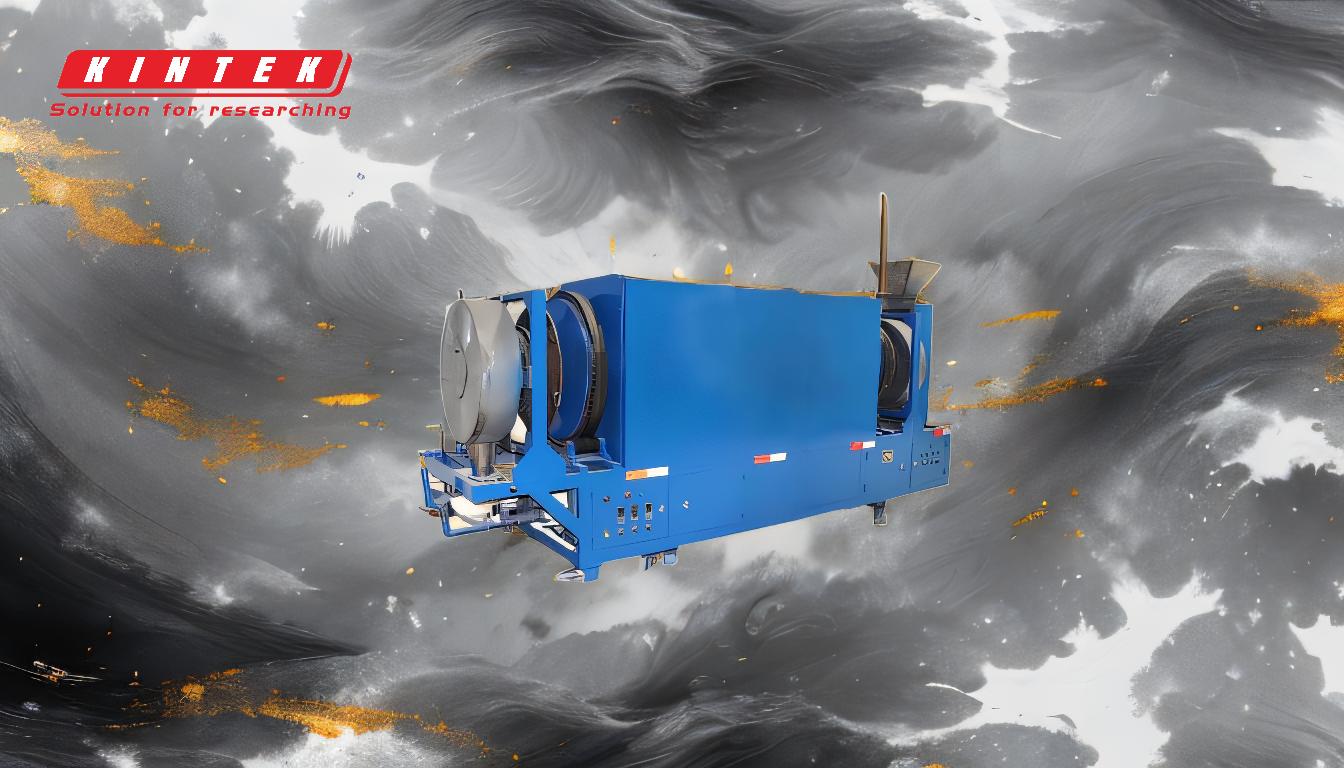
-
Definition and Purpose of a Small Pilot-Scale Pyrolysis Reactor:
- A small pilot-scale pyrolysis reactor is a scaled-down version of industrial pyrolysis systems, designed for research, development, and small-scale production.
- It allows for the testing and optimization of pyrolysis processes before scaling up to larger, continuous systems.
- Common applications include converting waste materials (e.g., tires, plastics, biomass) into useful products like liquid oil, syngas, and biochar.
-
Operating Principles:
- Pyrolysis involves heating organic materials in the absence of oxygen to break them down into smaller molecules.
- The process occurs at temperatures above 430 °C (800 °F) and relies on thermodynamic principles to ensure efficient decomposition.
- The reactor operates as a closed system, preventing oxygen from entering and ensuring the process is irreversible.
-
Types of Reactors:
- Drum Pyrolysis Reactor: A rotating drum-shaped vessel that circulates heat internally, ideal for slow pyrolysis of biomass. It produces syngas and biochar.
- Rotary Pyrolysis Reactor: Operates in a horizontal 360-degree rotation mode, ensuring even heating and higher oil yield. Suitable for semi-continuous and small-scale operations.
- Batch Pyrolysis Reactor: Processes waste materials intermittently, with a daily capacity of up to 10 tons. It is compact, energy-efficient, and ideal for small-scale applications.
-
Key Features of Small Pilot-Scale Reactors:
- Compact Size: Designed to occupy less space, making them suitable for laboratories and small facilities.
- Energy Efficiency: Lower energy consumption compared to full-scale industrial systems.
- Intermittent Operation: Operates in batches, allowing for flexibility in processing smaller quantities of material.
- Versatility: Can process a variety of feedstocks, including biomass, plastics, rubber, and oil sludge.
-
Applications and Products:
- Liquid Oil: Used as fuel or further refined into other products.
- Syngas: A combustible gas that can be used for heat and electricity generation.
- Biochar: A solid product used as a soil amendment or for carbon sequestration.
- Research and Development: Enables testing of new feedstocks, optimization of process parameters, and scaling studies.
-
Advantages of Small Pilot-Scale Systems:
- Cost-Effective: Lower capital and operational costs compared to large-scale systems.
- Scalability: Provides a pathway for scaling up processes based on pilot-scale results.
- Flexibility: Can handle a wide range of materials and process conditions.
- Environmental Benefits: Converts waste into valuable resources, reducing landfill use and greenhouse gas emissions.
-
Considerations for Equipment Purchasers:
- Feedstock Compatibility: Ensure the reactor can handle the specific materials you plan to process.
- Process Control: Look for systems with precise temperature and pressure controls for consistent results.
- Maintenance and Durability: Evaluate the ease of maintenance and the expected lifespan of the reactor.
- Safety Features: Check for safety mechanisms to handle high temperatures and prevent oxygen ingress.
- Output Quality: Assess the quality and yield of the products (oil, gas, biochar) to ensure they meet your requirements.
By understanding these key points, purchasers can make informed decisions when selecting a small pilot-scale pyrolysis reactor, ensuring it meets their specific needs for research, development, or small-scale production.
Summary Table:
Key Aspect | Details |
---|---|
Purpose | Research, development, and small-scale waste-to-resource conversion. |
Operating Temperature | Above 430 °C (800 °F) in an oxygen-free environment. |
Types | Drum, Rotary, and Batch reactors, each suited for specific applications. |
Key Features | Compact size, energy efficiency, intermittent operation, and versatility. |
Applications | Biomass, plastics, rubber, and oil sludge conversion into oil, gas, biochar. |
Advantages | Cost-effective, scalable, flexible, and environmentally beneficial. |
Buyer Considerations | Feedstock compatibility, process control, maintenance, safety, and output. |
Ready to explore small pilot-scale pyrolysis reactors for your needs? Contact us today to get started!