Sputtering is a widely used thin film deposition technique within the Physical Vapor Deposition (PVD) category. It involves bombarding a target material with high-energy ions in a vacuum chamber filled with an inert gas, typically argon. The ions dislodge atoms from the target, which then travel through the chamber and deposit onto a substrate, forming a thin film. This process is utilized in various industries, including semiconductors, optical devices, and solar panels, due to its precision and ability to create uniform coatings. Below, the key aspects of sputtering are explained in detail.
Key Points Explained:
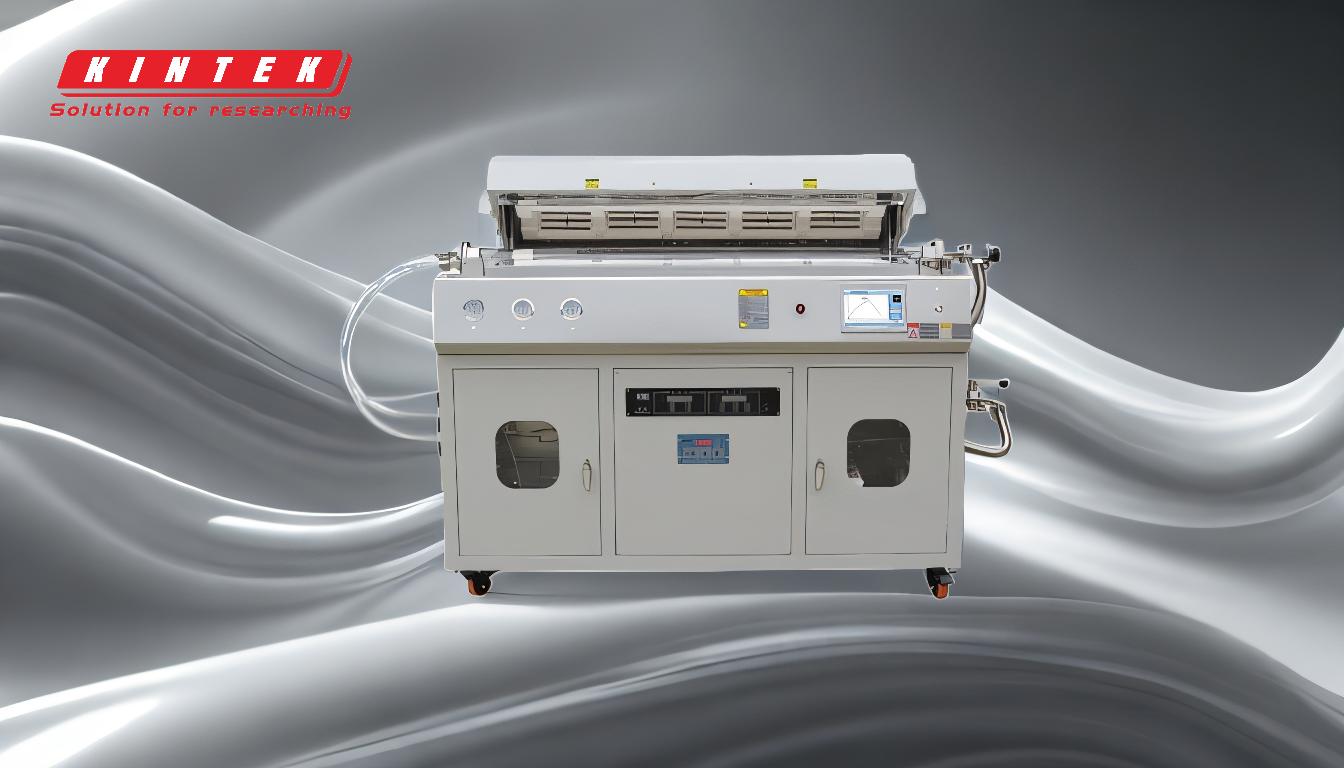
-
Definition and Mechanism of Sputtering
- Sputtering is a PVD process where atoms are ejected from a solid target material due to bombardment by high-energy ions.
- The process occurs in a vacuum chamber filled with an inert gas (usually argon).
- A high voltage is applied to create a plasma, which energizes the gas ions. These ions collide with the target, causing atoms to be "sputtered" off and deposited onto a substrate.
-
Components of the Sputtering Process
- Target Material: The material to be deposited, often made of metals, alloys, or compounds.
- Substrate: The surface to be coated, such as silicon wafers, solar panels, or optical devices.
- Inert Gas: Typically argon, which is ionized to create the plasma.
- Vacuum Chamber: Ensures a controlled environment free from contaminants.
- Power Supply: Provides the high voltage needed to ionize the gas and create the plasma.
-
How Sputtering Works
- A negative charge is applied to the target material, turning it into a cathode.
- The inert gas is ionized, creating positively charged ions that are attracted to the negatively charged target.
- The ions collide with the target, ejecting atoms through a process called momentum transfer.
- The ejected atoms travel through the vacuum and deposit onto the substrate, forming a thin film.
-
Applications of Sputtering
- Semiconductors: Used to deposit thin films of metals and dielectrics in integrated circuits.
- Optical Devices: Creates anti-reflective and reflective coatings for lenses and mirrors.
- Solar Panels: Deposits conductive and protective layers to enhance efficiency.
- Data Storage: Used in manufacturing hard disk drives and CDs.
- Automotive and Consumer Goods: Applied in anodizing processes for decorative and functional coatings.
-
Advantages of Sputtering
- Uniform Coatings: Produces highly uniform and dense thin films.
- Versatility: Can deposit a wide range of materials, including metals, alloys, and ceramics.
- Precision: Allows for precise control over film thickness and composition.
- Adhesion: Provides excellent adhesion between the film and the substrate.
- Scalability: Suitable for both small-scale research and large-scale industrial production.
-
Challenges and Considerations
- Cost: Requires specialized equipment and high vacuum conditions, which can be expensive.
- Complexity: The process involves precise control of parameters like gas pressure, voltage, and target-substrate distance.
- Material Limitations: Some materials may be difficult to sputter due to low sputtering yields or reactivity with the gas.
- Contamination: Ensuring a clean vacuum environment is critical to avoid impurities in the film.
-
Historical Context and Innovations
- Sputtering was first used commercially by Thomas Edison in 1904 to coat wax phonograph recordings with metal.
- Over time, advancements in vacuum technology and plasma physics have made sputtering more efficient and versatile.
- Modern variations, such as magnetron sputtering, have further improved deposition rates and film quality.
-
Comparison with Other Thin Film Deposition Methods
- Evaporation: Involves heating the target material until it vaporizes, but lacks the precision and uniformity of sputtering.
- Chemical Vapor Deposition (CVD): Relies on chemical reactions to deposit films, which can introduce impurities compared to the physical process of sputtering.
- Pulsed Laser Deposition (PLD): Uses laser pulses to ablate the target, but is less scalable than sputtering.
In summary, sputtering is a highly versatile and precise method for depositing thin films, with applications ranging from semiconductors to consumer goods. Its ability to produce uniform, high-quality coatings makes it a cornerstone of modern manufacturing and technology. However, it requires careful control of process parameters and specialized equipment, which can be a barrier for some applications.
Summary Table:
Aspect | Details |
---|---|
Definition | A PVD process where high-energy ions eject atoms from a target material. |
Key Components | Target material, substrate, inert gas (argon), vacuum chamber, power supply. |
How It Works | Ions bombard the target, ejecting atoms that deposit onto a substrate. |
Applications | Semiconductors, optical devices, solar panels, data storage, automotive. |
Advantages | Uniform coatings, versatility, precision, excellent adhesion, scalability. |
Challenges | High cost, process complexity, material limitations, contamination risks. |
Comparison with Others | More precise and uniform than evaporation, CVD, and PLD. |
Discover how sputtering can enhance your manufacturing process—contact our experts today!