Sputtering is a widely used physical vapor deposition (PVD) technique for depositing thin films onto substrates. It involves creating a plasma of inert gas (typically argon) in a vacuum chamber, where gas ions are accelerated toward a target material (cathode) made of the desired film material. Upon collision, atoms or molecules are ejected from the target and deposited onto a substrate, forming a thin, uniform film. Sputtering is favored for its ability to produce high-purity, adherent, and uniform coatings, making it suitable for applications in semiconductors, optics, and decorative coatings. The process is highly controllable, allowing for precise film thickness and composition.
Key Points Explained:
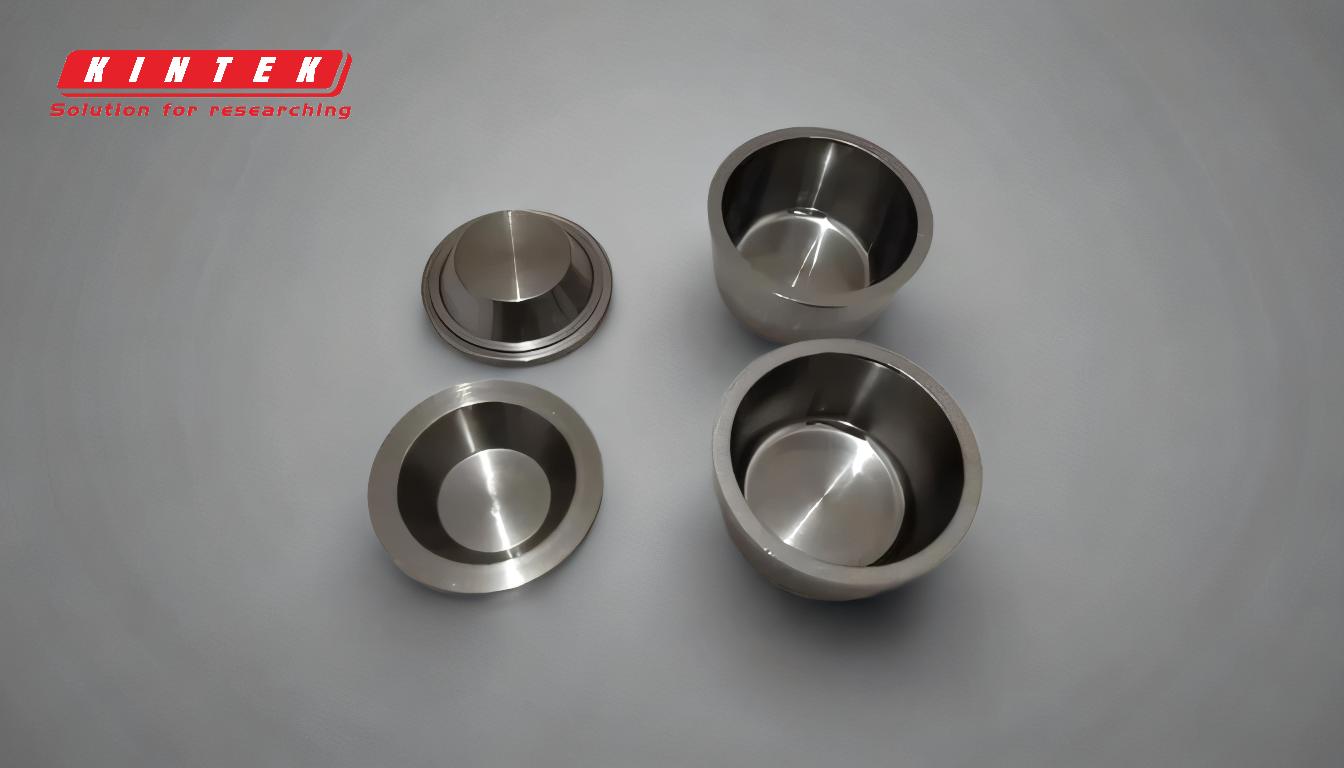
-
Definition and Overview of Sputtering:
- Sputtering is a physical vapor deposition (PVD) technique used to deposit thin films onto substrates.
- It involves the ejection of atoms or molecules from a solid target material due to bombardment by energetic ions, typically from an inert gas like argon.
- The ejected particles form a vapor stream that deposits onto a substrate, creating a thin film.
-
Components of the Sputtering Process:
- Vacuum Chamber: A controlled environment where the sputtering process occurs, ensuring minimal contamination and precise deposition.
- Target Material: The solid material (cathode) from which atoms or molecules are ejected. It is made of the desired film material.
- Inert Gas (Argon): Introduced into the vacuum chamber, it is ionized to form a plasma.
- Substrate: The surface onto which the ejected particles are deposited to form the thin film.
-
Mechanism of Sputtering:
- A voltage is applied between the target (cathode) and the vacuum chamber, creating an electric field.
- Inert gas atoms are ionized, forming positively charged ions (e.g., Ar⁺).
- These ions are accelerated toward the target material due to the electric field.
- Upon collision, atoms or molecules are ejected from the target through a process called "sputtering."
- The ejected particles travel through the vacuum and deposit onto the substrate, forming a thin film.
-
Types of Sputtering:
- DC Sputtering: Uses a direct current (DC) power source to generate the plasma. Suitable for conductive target materials.
- RF Sputtering: Uses radio frequency (RF) power to ionize the gas. Ideal for insulating or non-conductive target materials.
- Magnetron Sputtering: Incorporates magnetic fields to enhance plasma density and deposition rates, improving efficiency and film quality.
- Ion Beam Sputtering: Uses a focused ion beam to sputter the target, offering precise control over film properties.
-
Advantages of Sputtering:
- High Purity: The vacuum environment and inert gas minimize contamination, resulting in high-purity films.
- Uniformity: Sputtering produces highly uniform coatings, even on complex geometries.
- Adhesion: The energetic nature of the process ensures strong adhesion between the film and substrate.
- Versatility: Suitable for a wide range of materials, including metals, alloys, ceramics, and semiconductors.
- Controllability: Precise control over film thickness, composition, and properties.
-
Applications of Sputtering:
- Semiconductors: Used for depositing conductive and insulating layers in integrated circuits.
- Optics: Applied in the production of anti-reflective coatings, mirrors, and optical filters.
- Decorative Coatings: Used for depositing thin films on jewelry, watches, and consumer electronics.
- Wear-Resistant Coatings: Applied to tools and industrial components to enhance durability.
- Energy: Used in the fabrication of solar cells and fuel cell components.
-
Comparison with Other Thin Film Deposition Methods:
- Chemical Vapor Deposition (CVD): Involves chemical reactions to deposit films. CVD offers high precision but requires higher temperatures and more complex setups.
- Thermal Evaporation: Involves heating the target material to its vaporization point. It is simpler but less suitable for high-melting-point materials.
- Electron Beam Evaporation: Uses an electron beam to vaporize the target material. It offers high deposition rates but may lack uniformity.
- Pulsed Laser Deposition (PLD): Uses a laser to ablate the target material. It is highly precise but limited to small-scale applications.
-
Challenges and Limitations:
- Cost: Sputtering equipment can be expensive due to the need for vacuum systems and precise controls.
- Deposition Rate: Sputtering rates may be slower compared to other methods like thermal evaporation.
- Target Utilization: The target material may not be fully utilized, leading to waste.
- Complexity: Requires careful control of parameters such as gas pressure, voltage, and substrate temperature.
By understanding the principles, advantages, and applications of sputtering, purchasers of equipment and consumables can make informed decisions about its suitability for their specific needs.
Summary Table:
Aspect | Details |
---|---|
Definition | Physical vapor deposition (PVD) technique for thin film deposition. |
Key Components | Vacuum chamber, target material, inert gas (argon), substrate. |
Mechanism | Gas ions bombard target, ejecting atoms that deposit onto a substrate. |
Types | DC, RF, Magnetron, Ion Beam Sputtering. |
Advantages | High purity, uniformity, strong adhesion, versatility, precise control. |
Applications | Semiconductors, optics, decorative coatings, wear-resistant coatings, energy. |
Challenges | High cost, slower deposition rates, target utilization, process complexity. |
Discover how sputtering can enhance your applications—contact us today for expert guidance!