Sputtering is a physical vapor deposition (PVD) technique used to deposit thin films onto substrates. It involves the ejection of atoms from a solid target material due to bombardment by high-energy ions, typically from an inert gas like argon. These ejected atoms form a vapor stream that deposits onto a substrate, creating a thin film. Sputtering is widely used in industries such as semiconductor manufacturing, optics, and decorative coatings due to its ability to produce high-quality, uniform films. The process can be categorized into several types, including DC, RF, pulsed DC, and HiPIMS, each suited for specific applications. Sputtering operates in a vacuum chamber, where controlled conditions ensure precise film deposition.
Key Points Explained:
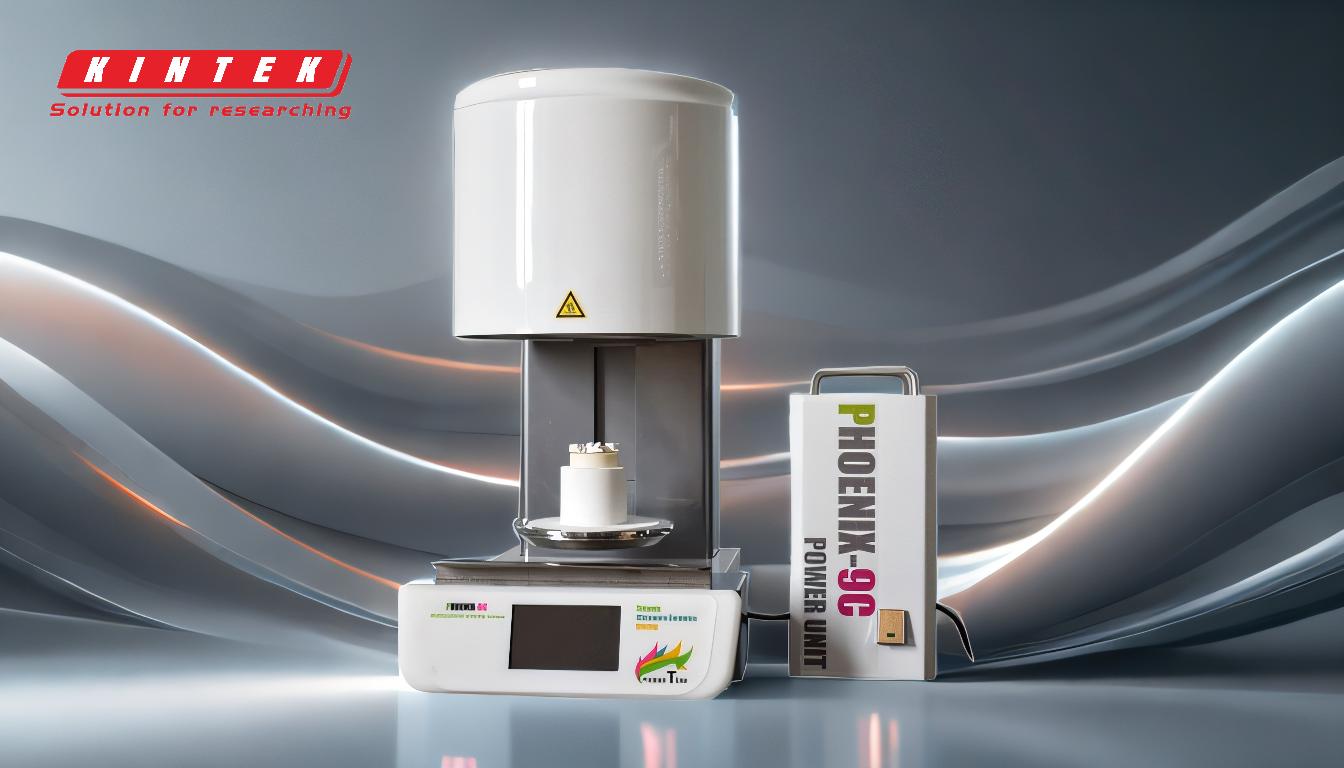
-
Definition and Basic Mechanism of Sputtering:
- Sputtering is a thin film deposition technique where atoms are ejected from a solid target material due to bombardment by high-energy ions.
- The process occurs in a vacuum chamber, where a controlled gas (usually argon) is introduced and ionized to form a plasma.
- The ions are accelerated toward the target material, causing atoms to be ejected and subsequently deposited onto a substrate.
-
Steps Involved in the Sputtering Process:
- Ion Generation: A plasma is created by applying a high voltage to an inert gas (e.g., argon) in a vacuum chamber.
- Target Bombardment: The positively charged ions collide with the target material, transferring momentum and ejecting atoms.
- Transport of Sputtered Atoms: The ejected atoms travel through the vacuum chamber and deposit onto the substrate.
- Film Formation: The sputtered atoms condense on the substrate, forming a thin, uniform film.
-
Types of Sputtering Techniques:
- DC Sputtering: Uses direct current to generate plasma, suitable for conductive materials.
- RF Sputtering: Uses radio frequency to generate plasma, ideal for insulating materials.
- Pulsed DC Sputtering: Combines DC and RF techniques, reducing arcing and improving film quality.
- HiPIMS (High-Power Impulse Magnetron Sputtering): Delivers high-power pulses, resulting in dense, high-quality films.
- Mid-Frequency Sputtering: Operates at frequencies between DC and RF, offering a balance of performance and cost.
-
Role of Plasma in Sputtering:
- Plasma is a partially ionized gas containing free electrons, ions, and neutral atoms.
- In sputtering, plasma is used to ionize the inert gas, creating high-energy ions that bombard the target material.
- The momentum transfer between the ions and target atoms is crucial for ejecting atoms and forming the vapor stream.
-
Applications of Sputtering:
- Semiconductor Industry: Used for depositing thin films in integrated circuits and microelectronics.
- Optics: Produces anti-reflective and reflective coatings for lenses and mirrors.
- Decorative Coatings: Creates durable and aesthetically pleasing finishes on consumer products.
- Magnetic Storage: Deposits thin films for hard drives and other storage devices.
-
Advantages of Sputtering:
- High-quality, uniform films with excellent adhesion.
- Ability to deposit a wide range of materials, including metals, alloys, and ceramics.
- Suitable for complex geometries and large-area substrates.
- Environmentally friendly, as it does not involve hazardous chemicals.
-
Challenges and Considerations:
- Requires a high vacuum environment, which can be costly to maintain.
- Target materials must be carefully selected to avoid contamination.
- Process parameters (e.g., gas pressure, voltage, and target-substrate distance) must be optimized for specific applications.
-
Re-Sputtering and Momentum Transfer:
- Re-sputtering refers to the removal of deposited material due to subsequent ion bombardment.
- Momentum transfer between ions and target atoms is a key factor in determining the efficiency and quality of the sputtering process.
By understanding these key points, equipment and consumable purchasers can make informed decisions about the appropriate sputtering techniques and materials for their specific applications.
Summary Table:
Aspect | Details |
---|---|
Definition | Sputtering is a PVD technique where atoms are ejected from a target material by high-energy ions. |
Key Steps | 1. Ion Generation 2. Target Bombardment 3. Transport of Atoms 4. Film Formation |
Types | DC, RF, Pulsed DC, HiPIMS, Mid-Frequency |
Applications | Semiconductors, Optics, Decorative Coatings, Magnetic Storage |
Advantages | High-quality films, wide material range, environmentally friendly |
Challenges | High vacuum requirements, target material selection, parameter optimization |
Discover the best sputtering solutions for your needs—contact our experts today!