The ball milling method offers numerous advantages, making it a widely used technique in various industries. Its primary benefits include cost-effectiveness, ease of operation, and the ability to produce fine powders with particle sizes as small as 10 microns. Additionally, it is suitable for both wet and dry grinding processes, maintains sterility through a closed container system, and is effective for milling toxic or abrasive materials. The method also supports continuous operation, has low energy consumption, and requires minimal maintenance and space. Furthermore, the creation of crystal defects during the process can be advantageous for specific applications.
Key Points Explained:
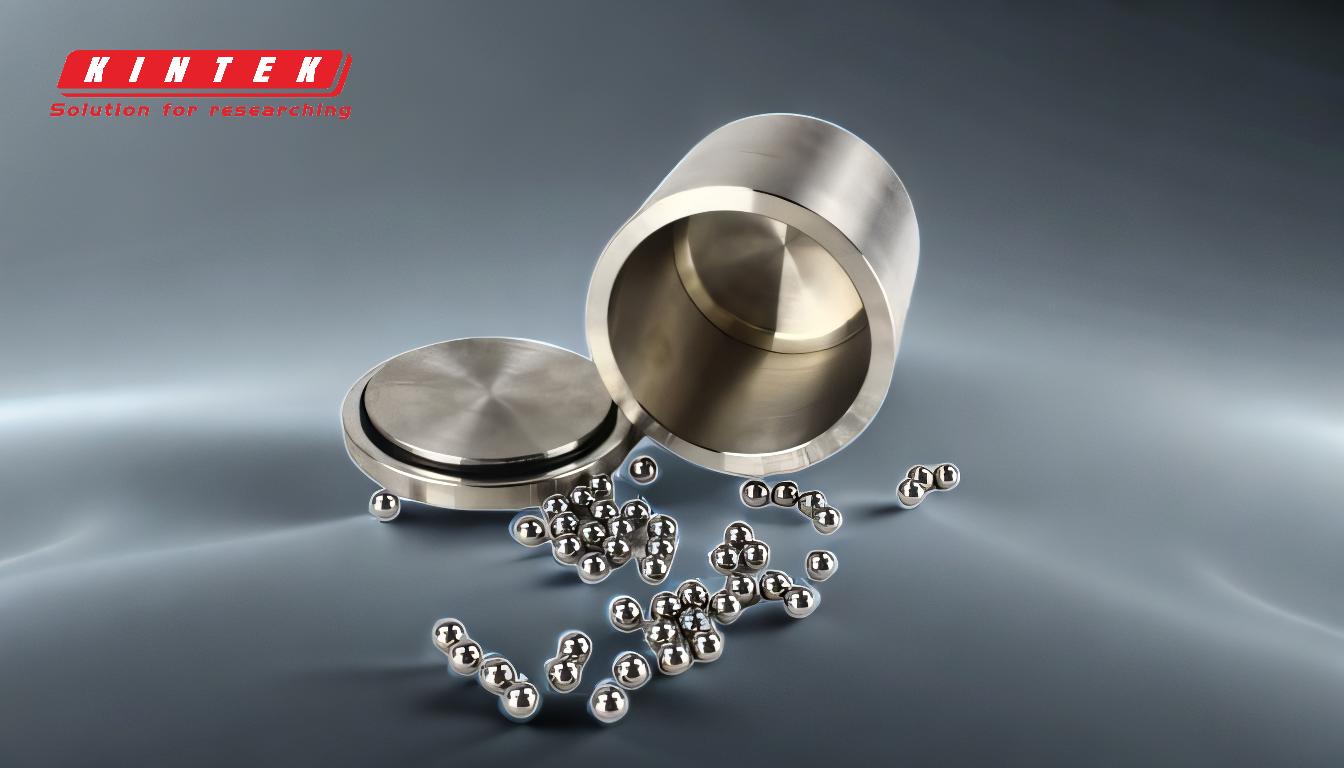
-
Cost-Effectiveness and Ease of Operation
- Ball milling is an inexpensive method compared to other grinding techniques, making it accessible for various applications.
- The process is straightforward and easy to perform, requiring minimal technical expertise.
- This combination of low cost and simplicity makes it a preferred choice for both small-scale and industrial applications.
-
Production of Fine Powders
- Ball mills can produce very fine powders with particle sizes less than or equal to 10 microns.
- This fine particle size is crucial for applications requiring high surface area or uniform particle distribution, such as in pharmaceuticals, ceramics, and nanomaterials.
-
Suitability for Wet and Dry Grinding
- Ball mills are versatile and can be used for both wet and dry grinding processes.
- Wet grinding is beneficial for materials that require a slurry form, while dry grinding is ideal for producing fine powders without added moisture.
-
Sterility Maintenance
- The closed container system of ball mills ensures sterility, which is essential for applications in the pharmaceutical and food industries.
- This feature prevents contamination and maintains the integrity of sensitive materials.
-
Low Energy Consumption
- Ball milling is energy-efficient, reducing operational costs and environmental impact.
- The process optimizes energy use by utilizing the kinetic energy of the grinding media (balls) to achieve particle size reduction.
-
Handling Toxic and Abrasive Materials
- Ball mills are suitable for milling toxic materials due to their enclosed design, which prevents exposure to harmful substances.
- They are also effective in milling abrasive materials, as the grinding media can withstand wear and tear.
-
Continuous Operation Capability
- Ball mills can operate continuously, making them ideal for large-scale production processes.
- This feature ensures consistent output and reduces downtime, enhancing productivity.
-
Low Maintenance and Space Requirements
- Ball mills require minimal maintenance, reducing long-term operational costs.
- Their compact design allows for installation in limited spaces, making them suitable for facilities with space constraints.
-
Creation of Crystal Defects
- The ball milling process can introduce crystal defects in materials, which can be advantageous for certain applications.
- These defects can enhance properties such as catalytic activity, mechanical strength, or electrical conductivity in materials.
-
Wide Range of Applications
- Ball milling is used across various industries, including pharmaceuticals, ceramics, metallurgy, and nanotechnology.
- Its versatility and adaptability make it a valuable tool for material processing and synthesis.
In summary, the ball milling method is a highly advantageous technique due to its cost-effectiveness, versatility, and ability to produce fine powders with specific properties. Its suitability for handling toxic and abrasive materials, low energy consumption, and minimal maintenance requirements further enhance its appeal for industrial and research applications.
Summary Table:
Advantage | Description |
---|---|
Cost-Effectiveness | Inexpensive compared to other grinding techniques, ideal for small and large-scale use. |
Fine Powder Production | Produces particles as small as 10 microns, essential for high surface area needs. |
Wet and Dry Grinding | Versatile for both wet and dry processes, suitable for diverse material types. |
Sterility Maintenance | Closed container system ensures contamination-free processing. |
Low Energy Consumption | Energy-efficient, reducing operational costs and environmental impact. |
Handles Toxic and Abrasive Materials | Enclosed design prevents exposure to harmful substances and withstands abrasion. |
Continuous Operation | Ideal for large-scale production with consistent output and minimal downtime. |
Low Maintenance and Space Needs | Minimal upkeep and compact design for space-constrained facilities. |
Creation of Crystal Defects | Enhances material properties like catalytic activity and mechanical strength. |
Wide Range of Applications | Used in pharmaceuticals, ceramics, metallurgy, and nanotechnology. |
Ready to enhance your material processing with ball milling? Contact us today to learn more!