Muffle furnaces are widely used in laboratories and industries for high-temperature processes such as ashing, sintering, and heat treatment. However, there are several alternatives to traditional muffle furnaces that offer unique advantages, such as improved efficiency, uniform heating, and versatility. These alternatives include microwave muffle furnace systems, tube furnaces, vacuum furnaces, and box furnaces. Each alternative is designed to meet specific temperature requirements and applications, making them suitable for various industries and laboratory settings. Understanding the features and benefits of these alternatives can help users select the most appropriate equipment for their needs.
Key Points Explained:
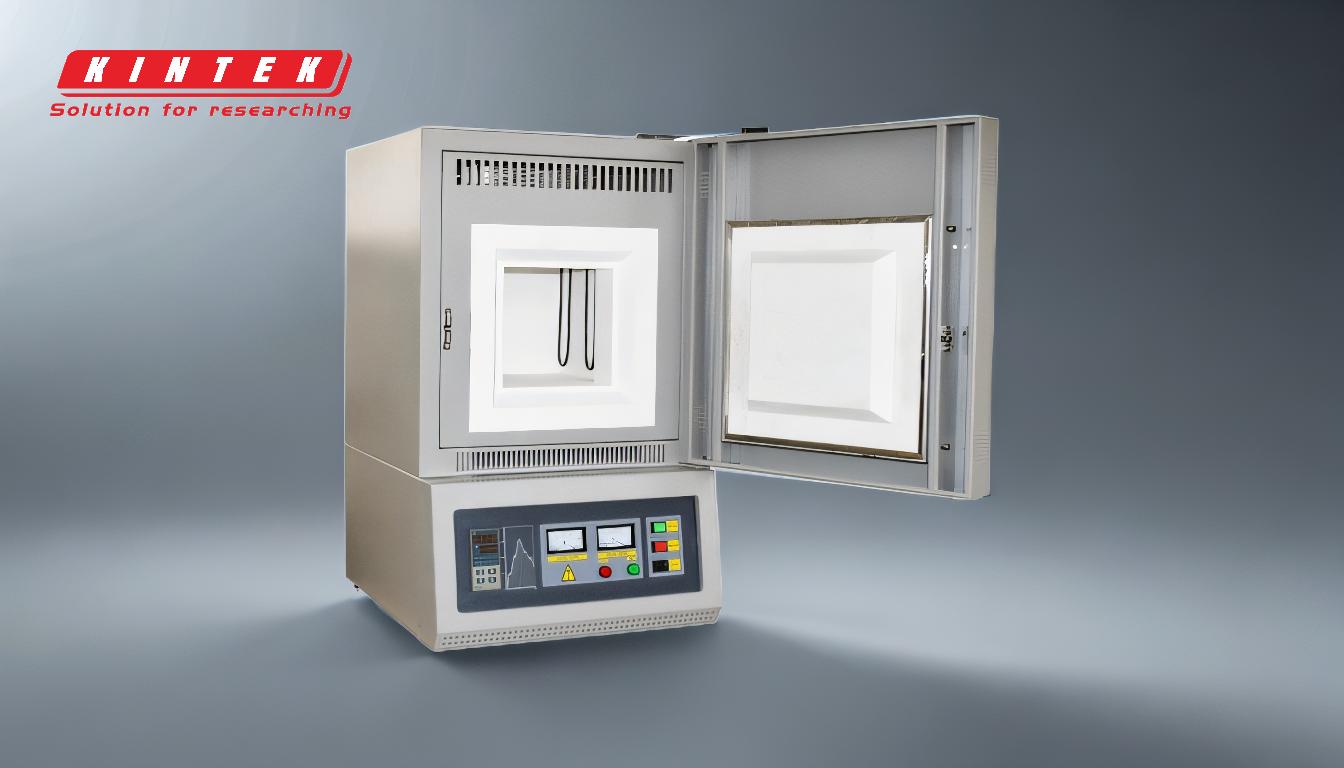
-
Microwave Muffle Furnace Systems
- Description: Microwave muffle furnace systems, such as Milestone's PYRO Microwave Muffle Furnace Ashing System, are advanced alternatives to conventional muffle furnaces.
-
Advantages:
- Improved efficiency due to faster heating and cooling times.
- Energy savings compared to traditional muffle furnaces.
- Suitable for ashing and other high-temperature applications.
- Applications: Laboratories in industries such as pharmaceuticals, food, and materials science.
-
Tube Furnaces
- Description: Tube furnaces are cylindrical furnaces that can replace muffle furnaces in many applications.
-
Advantages:
- Uniform heating, especially when using a metal tubular insert.
- Versatility in handling small samples or continuous processes.
- Available in various configurations, including horizontal and vertical setups.
- Applications: High-temperature processes like sintering, annealing, and material testing.
-
Vacuum Furnaces
- Description: Vacuum furnaces operate in a controlled atmosphere, often under vacuum or inert gas conditions.
-
Advantages:
- Prevents oxidation and contamination of samples.
- Suitable for heat-treating sensitive materials.
- Ensures precise temperature control and uniformity.
- Applications: Aerospace, metallurgy, and semiconductor industries.
-
Box Furnaces
- Description: Box furnaces are versatile alternatives with a box-shaped chamber for heating.
-
Advantages:
- Larger chamber capacity compared to muffle furnaces.
- Suitable for batch processing of larger samples.
- Available in both electric and gas-powered models.
- Applications: Heat treatment, ceramics, and glass manufacturing.
-
Drying Ovens and Laboratory Incubators
- Description: While not direct replacements for high-temperature muffle furnaces, drying ovens and incubators are used for lower-temperature applications.
-
Advantages:
- Cost-effective for specific applications like drying or incubation.
- Precise temperature control for sensitive materials.
- Applications: Food processing, pharmaceuticals, and biological research.
-
Factors to Consider When Choosing an Alternative
- Temperature Range: Ensure the alternative can achieve the required temperatures for your application.
- Heating Uniformity: Look for furnaces with strategically positioned heating elements for consistent results.
- Energy Efficiency: Consider systems like microwave muffle furnaces for reduced energy consumption.
- Sample Size and Throughput: Choose equipment that accommodates your sample size and processing volume.
- Atmosphere Control: For sensitive materials, opt for vacuum or inert gas furnaces.
By evaluating these alternatives based on your specific needs, you can find a suitable replacement for a traditional muffle furnace that enhances efficiency and meets your application requirements.
Summary Table:
Alternative | Key Advantages | Applications |
---|---|---|
Microwave Muffle Furnace | Faster heating/cooling, energy-efficient, suitable for ashing | Pharmaceuticals, food, materials science labs |
Tube Furnace | Uniform heating, versatile, horizontal/vertical configurations | Sintering, annealing, material testing |
Vacuum Furnace | Oxidation prevention, precise temperature control, inert atmosphere | Aerospace, metallurgy, semiconductor industries |
Box Furnace | Larger chamber capacity, batch processing, electric/gas-powered | Heat treatment, ceramics, glass manufacturing |
Drying Ovens/Incubators | Cost-effective, precise temperature control for lower-temperature applications | Food processing, pharmaceuticals, biological research |
Need help choosing the right furnace for your lab? Contact our experts today to find the perfect solution!