Sputtering, particularly RF (Radio Frequency) and DC (Direct Current) sputtering, is a versatile thin-film deposition technique widely used in industries such as electronics, semiconductors, optics, and materials science. RF sputtering is primarily employed for depositing non-conductive (dielectric) materials like oxides, which are essential in semiconductor manufacturing and optical device fabrication. DC sputtering, on the other hand, is cost-effective for conductive materials and is used to deposit metals and alloys with high uniformity and density. Both techniques are critical in creating thin films for applications like microchip circuitry, scratch-resistant coatings, optical waveguides, and solar cells. Their ability to produce precise, high-quality films at low temperatures makes them indispensable in advanced manufacturing processes.
Key Points Explained:
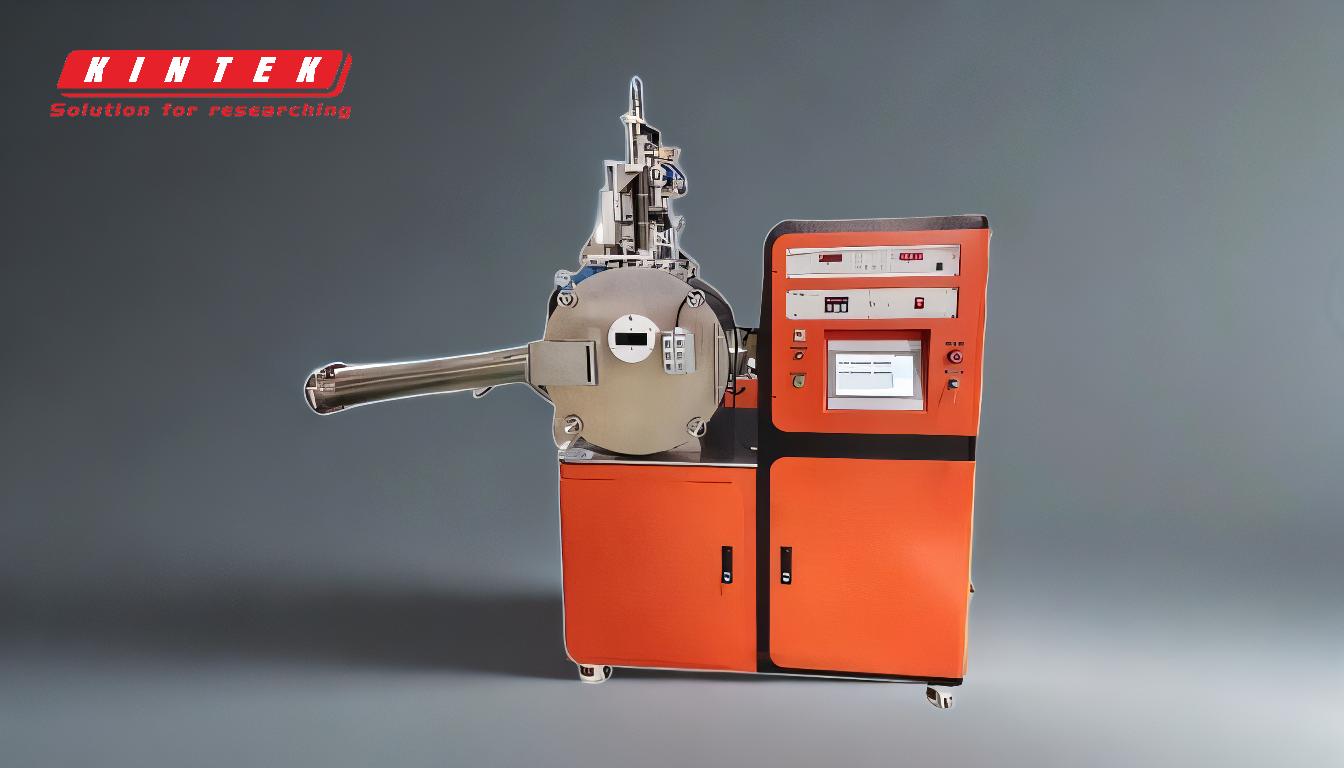
-
Overview of Sputtering:
- Sputtering is a physical vapor deposition (PVD) technique used to deposit thin films on substrates like glass, metals, and semiconductors.
- It involves bombarding a target material with high-energy particles, causing atoms to be ejected and deposited onto a substrate.
-
Applications of RF Sputtering:
- Semiconductor Industry: RF sputtering is crucial for depositing insulating oxide films (e.g., Aluminum Oxide, Silicon Oxide, Tantalum Oxide) used in microchip circuitry. These films act as insulating layers between conductive layers.
- Optical Devices: RF sputtering is used to fabricate optical planar waveguides, photonic microcavities, and 1-D photonic crystals. It allows for precise control of refractive index and thickness, making it ideal for applications in the visible and near-infrared (NIR) regions.
- Dielectric Materials: RF sputtering is specifically designed for non-conductive materials, overcoming the limitations of DC sputtering, which cannot effectively deposit dielectric films due to surface charging issues.
-
Applications of DC Sputtering:
- Conductive Materials: DC sputtering is cost-effective and efficient for depositing conductive metals and alloys, such as molybdenum, tantalum, and niobium-based films. These films are used in applications requiring high density, uniformity, and low roughness.
- Scratch-Resistant Coatings: For example, molybdenum thin films deposited via DC sputtering can enhance the scratch resistance of nickel-titanium shape memory alloys.
- General Thin-Film Deposition: DC sputtering is widely used in industries requiring thin films for electronics, wear-resistant coatings, and decorative finishes.
-
Advantages of RF and DC Sputtering:
-
RF Sputtering:
- Suitable for non-conductive materials.
- Enables high-quality film deposition at low substrate temperatures.
- Ideal for applications requiring precise control over film properties, such as optical devices and semiconductor layers.
-
DC Sputtering:
- Cost-effective for conductive materials.
- Produces films with high density, uniformity, and low surface roughness.
- Widely used in industrial applications requiring durable and functional coatings.
-
RF Sputtering:
-
Comparison of RF and DC Sputtering:
- Material Suitability: RF sputtering is used for dielectric materials, while DC sputtering is used for conductive materials.
- Power Source: RF sputtering uses an AC power source to prevent surface charging, whereas DC sputtering uses a DC power source.
- Applications: RF sputtering is more common in semiconductor and optical industries, while DC sputtering is prevalent in general thin-film deposition and industrial coatings.
-
Industrial Relevance:
- Both RF and DC sputtering are critical in advanced manufacturing processes, enabling the production of high-performance materials and devices.
- Their ability to deposit thin films with precise control over thickness, composition, and properties makes them indispensable in modern technology.
In summary, RF and DC sputtering are complementary techniques with distinct applications. RF sputtering excels in depositing non-conductive materials for semiconductors and optical devices, while DC sputtering is ideal for conductive materials in industrial and functional coatings. Together, they play a vital role in advancing technology across multiple industries.
Summary Table:
Aspect | RF Sputtering | DC Sputtering |
---|---|---|
Material Suitability | Non-conductive (dielectric) materials (e.g., oxides) | Conductive materials (e.g., metals, alloys) |
Applications | Semiconductor layers, optical devices, dielectric films | Scratch-resistant coatings, industrial coatings, general thin-film deposition |
Advantages | Precise control, low-temperature deposition, ideal for optical and semiconductor | Cost-effective, high density, uniformity, low surface roughness |
Power Source | AC power source (prevents surface charging) | DC power source |
Learn how RF and DC sputtering can enhance your manufacturing processes—contact our experts today!