The critical speed of a ball mill is a fundamental concept in grinding operations, representing the speed at which the grinding medium (typically steel balls) begins to rotate along the inner walls of the mill, resulting in no effective grinding action. For efficient grinding, the ball mill must operate above this critical speed to ensure the grinding medium tumbles and impacts the material. The critical speed is influenced by factors such as the diameter of the mill and the gravitational force. Understanding and controlling the critical speed is essential for optimizing grinding efficiency and achieving desired material fineness.
Key Points Explained:
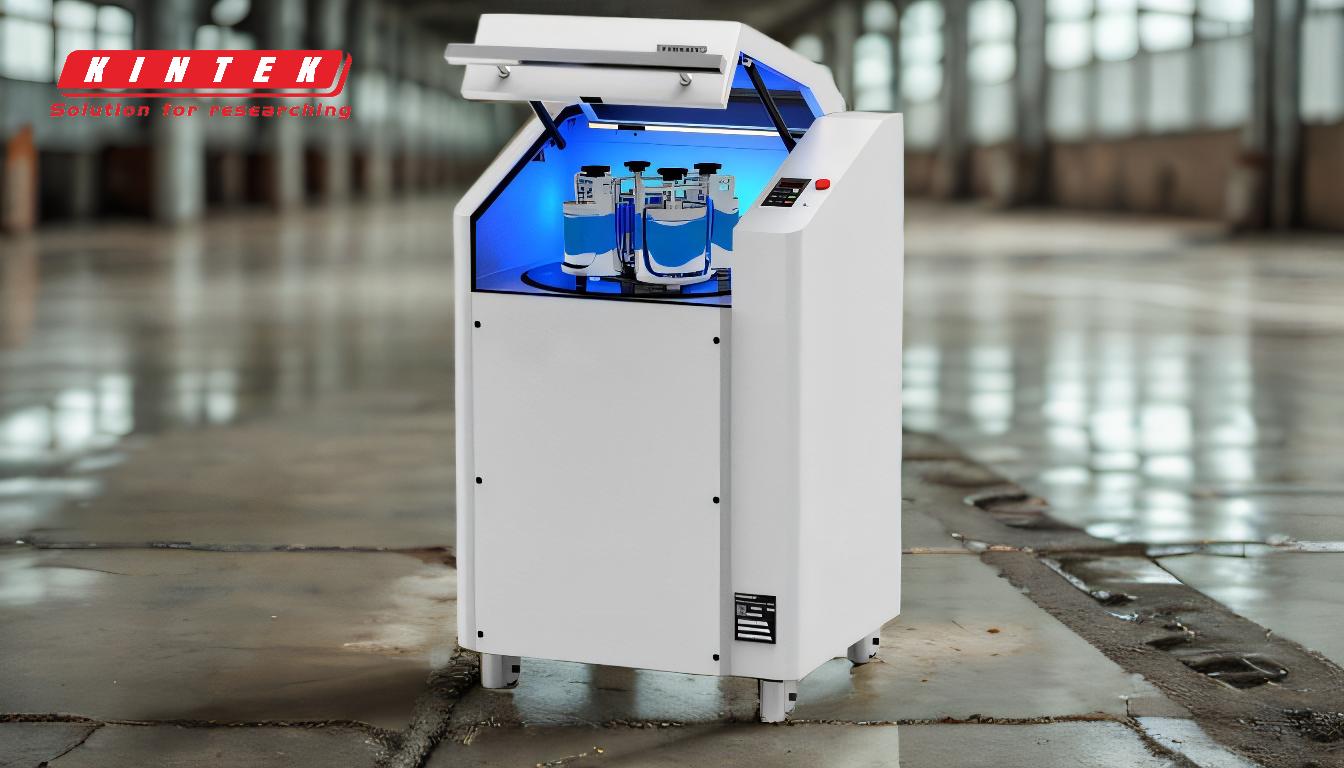
-
Definition of Critical Speed:
- The critical speed of a ball mill is the rotational speed at which the grinding medium (e.g., steel balls) adheres to the inner wall of the mill due to centrifugal force. At this speed, the balls rotate with the mill shell, and no grinding action occurs because the balls are not tumbling or impacting the material.
-
Importance of Operating Above Critical Speed:
- For effective grinding, the ball mill must operate above its critical speed. This ensures that the grinding medium is in constant motion, tumbling and impacting the material, which is essential for breaking down particles to the desired size.
-
Factors Influencing Critical Speed:
- The critical speed is primarily determined by the diameter of the mill. The larger the diameter, the lower the critical speed. This relationship is due to the balance between centrifugal force and gravitational force acting on the grinding medium.
-
Mathematical Relationship:
- The critical speed (Nc) can be calculated using the formula: [ N_c = \frac{42.3}{\sqrt{D}} ] where ( D ) is the internal diameter of the mill in meters. This formula provides a theoretical value, but practical operating speeds may vary based on specific conditions and requirements.
-
Practical Implications:
- Operating a ball mill at or below the critical speed results in inefficient grinding, as the grinding medium does not tumble or impact the material. Conversely, operating significantly above the critical speed can lead to excessive wear and energy consumption. Therefore, finding the optimal operating speed is crucial for balancing grinding efficiency and operational costs.
-
Average Critical Speed:
- The average critical speed for most industrial ball mills typically ranges between 65% to 80% of the theoretical critical speed. This range ensures that the mill operates efficiently without excessive wear or energy consumption. For example, if the theoretical critical speed is 100 rpm, the practical operating speed would be between 65 rpm and 80 rpm.
-
Impact on Grinding Efficiency:
- The critical speed directly impacts the grinding efficiency of the ball mill. Operating above the critical speed ensures that the grinding medium is actively tumbling and impacting the material, leading to effective particle size reduction. This is crucial for achieving the desired fineness and quality of the ground material.
-
Considerations for Equipment Purchasers:
- When purchasing a ball mill, it is essential to consider the critical speed in relation to the mill's diameter and intended application. Understanding the critical speed helps in selecting a mill that operates efficiently and meets the specific grinding requirements. Additionally, buyers should consider the mill's design, material of construction, and energy consumption to ensure optimal performance and cost-effectiveness.
By understanding and applying these key points, equipment purchasers can make informed decisions when selecting and operating ball mills, ensuring efficient and effective grinding operations.
Summary Table:
Key Aspect | Description |
---|---|
Definition | Rotational speed where grinding medium adheres to the mill wall, halting grinding action. |
Optimal Operation | Operate above critical speed for effective tumbling and material impact. |
Influencing Factors | Mill diameter and gravitational force. Larger diameter = lower critical speed. |
Formula | ( N_c = \frac{42.3}{\sqrt{D}} ) (D = mill diameter in meters). |
Practical Speed Range | 65% to 80% of theoretical critical speed for industrial ball mills. |
Impact on Efficiency | Ensures effective particle size reduction and desired material fineness. |
Purchasing Considerations | Evaluate mill diameter, design, material, and energy consumption for optimal performance. |
Need help selecting or optimizing a ball mill? Contact our experts today for tailored solutions!