The best material for a pyrolysis reactor depends on factors such as the type of raw material being processed, the operating conditions (temperature, pressure, and corrosive environment), and the desired durability of the reactor. Common materials include Q245R and Q345R boiler plates, which are cost-effective and suitable for high-temperature environments, and 304 and 306 stainless steel, which offer excellent corrosion resistance and durability. The choice of material should align with the specific requirements of the pyrolysis process, such as resistance to thermal stress, chemical corrosion, and mechanical wear. Additionally, the reactor's design and components, including the driving device, base, main furnace, and casing, must be carefully selected to ensure efficient and safe operation.
Key Points Explained:
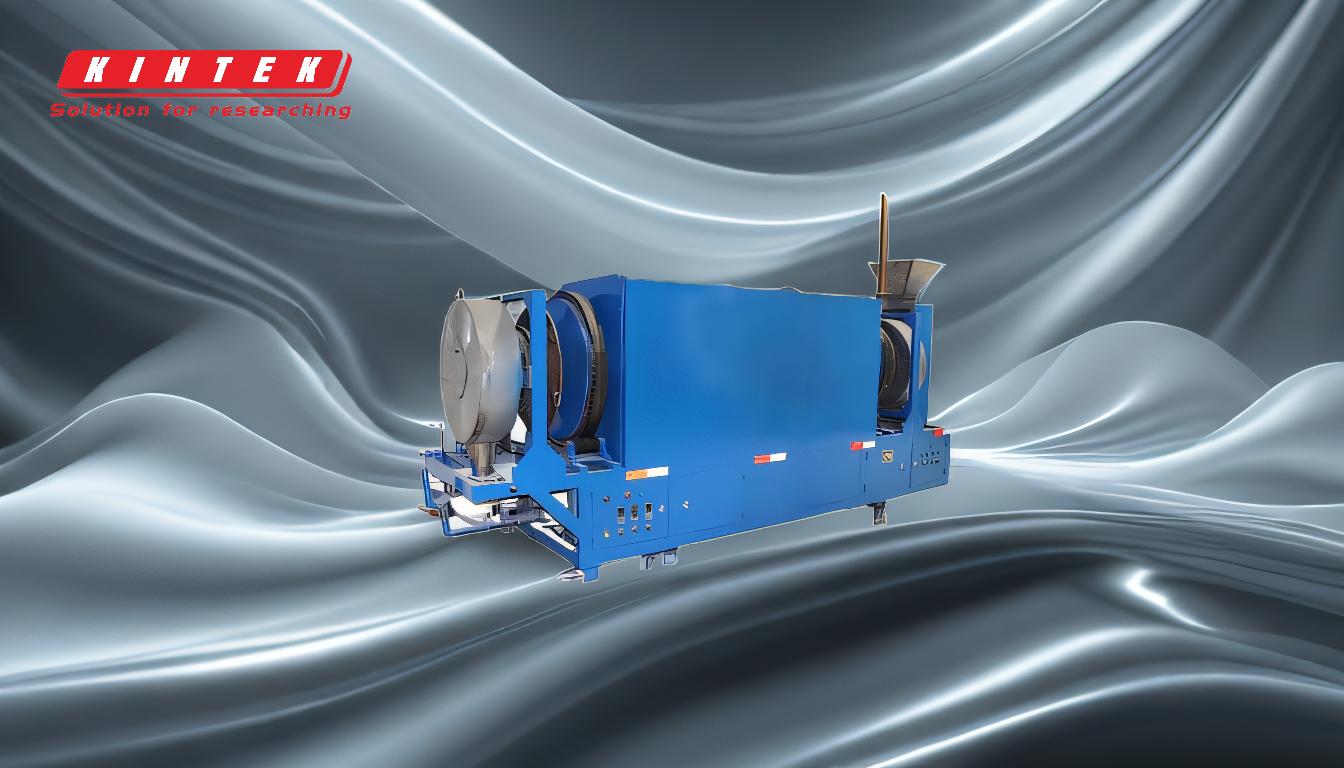
-
Material Options for Pyrolysis Reactors:
- Q245R and Q345R Boiler Plates: These materials are commonly used in high-temperature applications due to their strength and thermal resistance. They are cost-effective and suitable for pyrolysis reactors operating under moderate conditions. However, they may not be ideal for highly corrosive environments.
- 304 and 306 Stainless Steel: These stainless steel grades are preferred for their excellent corrosion resistance, making them suitable for pyrolysis processes involving corrosive materials or byproducts. They are more durable and can withstand higher temperatures and pressures compared to boiler plates.
-
Factors Influencing Material Selection:
- Temperature and Pressure: Pyrolysis reactors operate at high temperatures (typically 400°C to 800°C) and sometimes under pressure. Materials must have high thermal stability and mechanical strength to withstand these conditions.
- Corrosion Resistance: The reactor material must resist chemical corrosion from the raw materials (e.g., waste tires, plastics, oil sludge) and the byproducts (e.g., acidic gases) generated during pyrolysis.
- Durability and Maintenance: Stainless steel reactors generally require less maintenance and have a longer lifespan compared to boiler plate reactors, but they are more expensive.
-
Reactor Design and Components:
- Driving Device: Ensures the proper rotation or movement of the reactor, which is critical for uniform heating and efficient pyrolysis.
- Base: Provides structural support and stability to the reactor system.
- Main Furnace: The core component where pyrolysis occurs. It must be made from materials that can withstand high temperatures and corrosive environments.
- Casing: Protects the reactor and helps maintain the internal temperature, improving energy efficiency.
-
Raw Materials and Their Impact:
- Waste Tires/Rubber: Yield oil at rates of 30% to 52%, depending on the type. These materials can produce corrosive byproducts, necessitating the use of corrosion-resistant materials like stainless steel.
- Waste Plastics: Materials like PP, PE, and PS yield over 90% oil, while others like ABS yield 20% to 50%. The high oil yield and potential for corrosive byproducts make stainless steel a preferred choice.
- Oil Sludge: The oil content varies, influencing the choice of reactor material based on the expected corrosive nature of the sludge.
-
Batch vs. Continuous Reactors:
- Batch Reactors: Simple, sealed vessels suitable for small-scale operations. They are cost-effective and easy to maintain but may have limitations in terms of scalability and efficiency.
- Continuous Reactors: Designed for large-scale operations, offering higher efficiency and better control over the pyrolysis process. The material selection for continuous reactors must account for prolonged exposure to high temperatures and corrosive environments.
By considering these factors, the best material for a pyrolysis reactor can be chosen to ensure optimal performance, durability, and cost-effectiveness. Stainless steel is generally the preferred choice for its superior corrosion resistance and durability, while boiler plates are suitable for less demanding applications.
Summary Table:
Material | Advantages | Best For |
---|---|---|
Q245R/Q345R | Cost-effective, high thermal resistance | Moderate-temperature, non-corrosive environments |
304/306 Stainless | Excellent corrosion resistance, durable, high-temperature stability | Corrosive environments, high-temperature and high-pressure applications |
Need help selecting the best material for your pyrolysis reactor? Contact our experts today for personalized advice!