A colloid mill is a versatile machine used across industries like pharmaceuticals, food and beverage, and chemicals for tasks such as particle size reduction, emulsification, homogenization, and dispersion. Its capacity varies depending on the model and application, but it is designed to handle small, medium, and large batches of production efficiently. The machine operates on the rotor-stator principle, creating high shear forces to break down materials into fine particles or suspensions. Its compact design ensures high-capacity output with minimal space requirements, making it suitable for diverse production scales. The capacity of a colloid mill is influenced by factors such as rotor-stator gap adjustment, material viscosity, and the specific application requirements.
Key Points Explained:
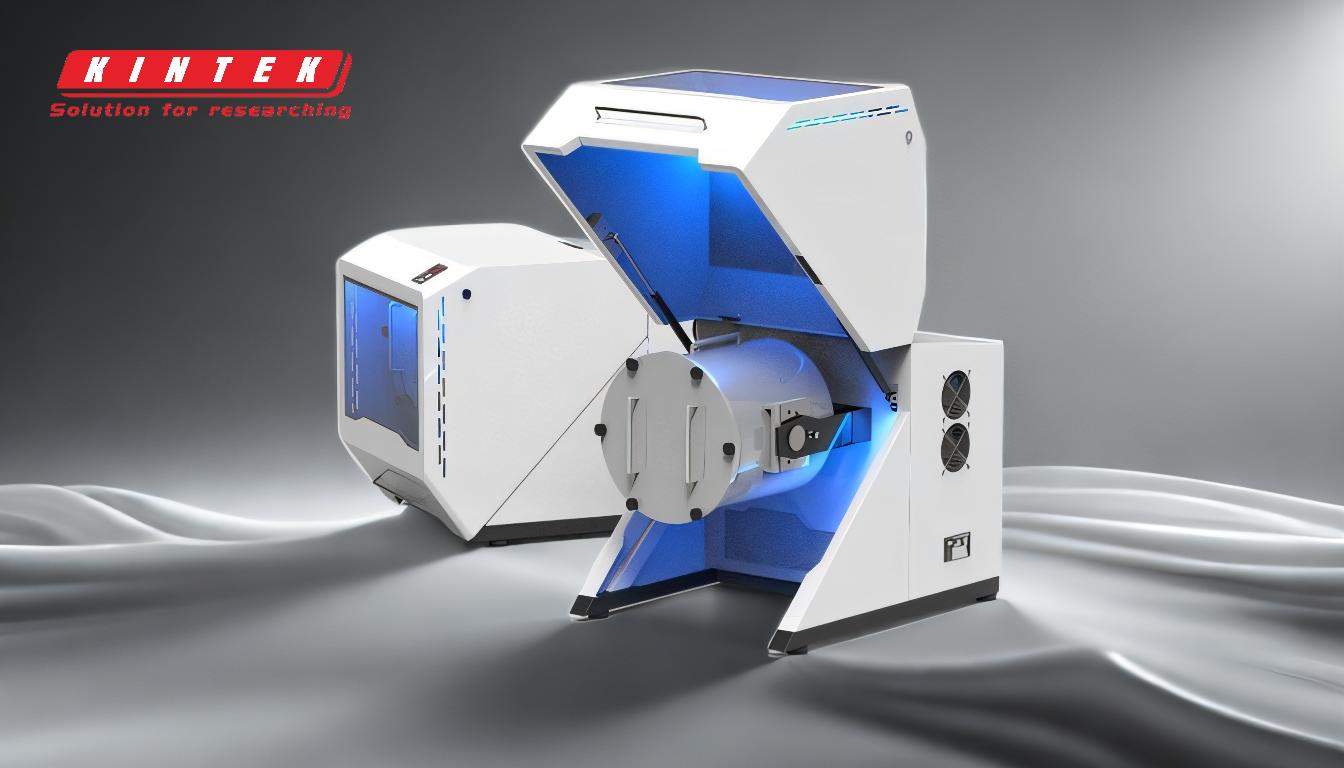
-
Rotor-Stator Principle:
- The colloid mill operates using a rapidly rotating rotor and a static stator, creating a small gap between them.
- This gap generates high shear forces, which break down solid materials into fine particles or disperse them into liquids.
- The adjustable rotor-stator gap allows for precise control over the particle size and consistency of the final product.
-
Batch Size Flexibility:
- Colloid mills are designed to handle small, medium, and large batches of production.
- This makes them suitable for a wide range of industries, from small-scale laboratory applications to large-scale industrial production.
-
High Capacity Output:
- Despite its compact design, a colloid mill delivers high-capacity output, making it efficient for various production needs.
- The machine's ability to process large volumes of material in a single cycle reduces processing time and increases productivity.
-
Material Versatility:
- Colloid mills are capable of processing highly viscous materials, suspensions, emulsions, and colloidal dispersions.
- They are ideal for applications requiring superfine grinding, emulsifying, homogenizing, and dispersing in a single process cycle.
-
Industry Applications:
- Pharmaceuticals: Used for preparing colloidal dispersions, suspensions, emulsions, and ointments.
- Food and Beverage: Ideal for creating smooth textures in products like sauces, dressings, and beverages.
- Chemicals: Suitable for dispersion and homogenization of raw materials in chemical formulations.
-
Design Features:
- Compact Footprint: The colloid mill requires minimal space, making it suitable for facilities with limited room.
- Ease of Use: Simple adjustment of the rotor-stator gap and optional overload pressure release mechanisms enhance usability.
- Low Maintenance: Constructed with durable materials like Stainless Steel 316 and 304, the machine is designed for long-term use with minimal upkeep.
- Contamination Prevention: Food-grade seals ensure that the processed materials remain free from contamination.
-
Factors Influencing Capacity:
- Rotor-Stator Gap: Adjusting the gap between the rotor and stator can increase or decrease the machine's throughput and the fineness of the processed material.
- Material Viscosity: Higher viscosity materials may require slower processing speeds or specialized configurations to maintain efficiency.
- Application Requirements: The specific needs of the application, such as particle size or dispersion quality, can influence the machine's effective capacity.
-
Advantages Over Other Machines:
- Colloid mills are more efficient than traditional grinding or mixing machines for tasks requiring simultaneous grinding, emulsifying, and homogenizing.
- Their ability to process materials in a single cycle reduces the need for multiple machines, saving time and space.
In summary, the capacity of a colloid mill is highly adaptable, catering to a wide range of production scales and material types. Its efficient design, combined with precise control over processing parameters, makes it a valuable tool in industries requiring fine particle size reduction and uniform dispersion.
Summary Table:
Feature | Details |
---|---|
Rotor-Stator Principle | High shear forces for fine particle size reduction and dispersion. |
Batch Size Flexibility | Handles small, medium, and large production batches efficiently. |
High Capacity Output | Compact design with high throughput for diverse production scales. |
Material Versatility | Processes viscous materials, suspensions, emulsions, and colloidal dispersions. |
Industry Applications | Pharmaceuticals, food and beverage, chemicals. |
Design Features | Compact footprint, low maintenance, contamination prevention. |
Capacity Influencers | Rotor-stator gap, material viscosity, application requirements. |
Looking for a colloid mill tailored to your needs? Contact us today for expert guidance!