The Chemical Vapor Deposition (CVD) process for silicon carbide (SiC) involves the deposition of gaseous reactants onto a substrate to form a thin film of silicon carbide. This process is widely used in the semiconductor industry due to its ability to produce high-purity, high-performance materials. The CVD process for SiC typically involves several key steps: the introduction of gaseous precursors into a reaction chamber, activation of these precursors through heat or other means, surface reactions that lead to the deposition of SiC on the substrate, and the removal of byproducts from the chamber. The process is highly dependent on factors such as temperature, pressure, and the nature of the precursors used.
Key Points Explained:
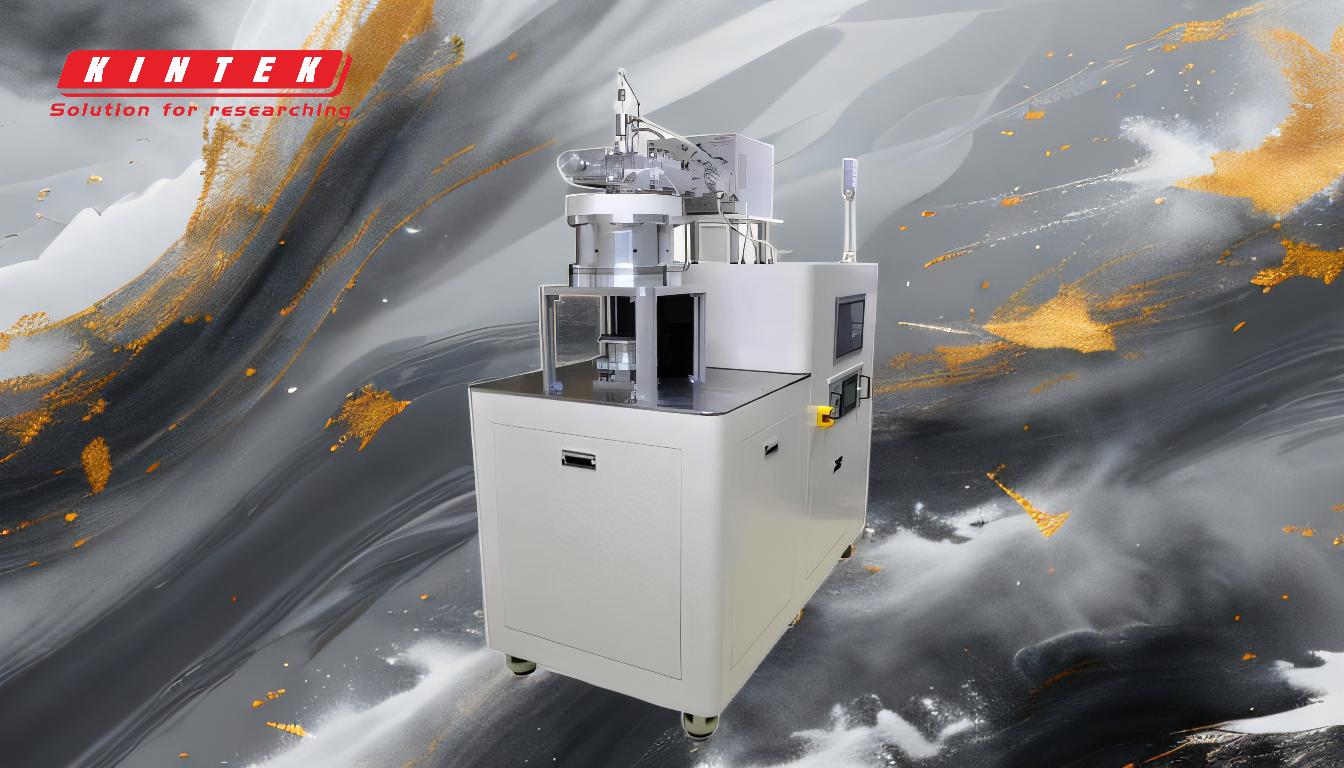
-
Introduction of Reactants:
- Gaseous precursors, such as silane (SiH₄) and methane (CH₄), are introduced into a reaction chamber containing the substrate. These precursors are often mixed with carrier gases like hydrogen (H₂) or argon (Ar) to facilitate their transport into the chamber.
- The substrate is typically heated to high temperatures (900-1400 °C) to promote the chemical reactions necessary for deposition.
-
Activation of Reactants:
- The precursors are activated through thermal energy, plasma, or catalysts. In the case of SiC deposition, thermal activation is most common, where the high temperature causes the precursors to decompose or react.
- This step is crucial as it determines the type of reaction that will occur and the quality of the deposited film.
-
Surface Reaction and Deposition:
- Activated precursors react at the substrate surface to form silicon carbide. The reaction typically involves the decomposition of silane and methane, leading to the formation of SiC and the release of hydrogen gas as a byproduct.
- The deposition process begins with the formation of small islands of SiC on the substrate surface, which then grow and merge to form a continuous film.
-
Removal of Byproducts:
- Volatile byproducts, such as hydrogen gas, are removed from the reaction chamber. This is typically done using a vacuum pump or by flowing an inert gas through the chamber to carry away the byproducts.
- The removal of byproducts is essential to prevent contamination of the deposited film and to maintain the desired properties of the SiC coating.
-
Heat Transfer and Gas Flow:
- Heat transfer plays a critical role in the CVD process, as the substrate must be maintained at a high temperature to ensure proper deposition. The reaction chamber is designed to optimize heat conduction and gas flow to ensure uniform deposition across the substrate.
- The flow of gases through the chamber must be carefully controlled to ensure even distribution of the precursors and to prevent the formation of defects in the deposited film.
-
Applications and Versatility:
- The CVD process for SiC is highly versatile and can be used to produce a wide range of materials, including coatings, powders, fibers, and monolithic components. It is particularly valuable in the production of semiconductors, where high-purity SiC is required for high-performance electronic devices.
- The ability to control the deposition process at the atomic level makes CVD an essential technique for the fabrication of advanced materials with tailored properties.
In summary, the CVD process for silicon carbide is a complex but highly effective method for depositing high-quality SiC films on various substrates. The process involves multiple steps, each of which must be carefully controlled to ensure the desired outcome. The versatility and precision of the CVD process make it an indispensable tool in the production of advanced materials for a wide range of applications.
Summary Table:
Step | Description |
---|---|
Introduction of Reactants | Gaseous precursors (e.g., SiH₄, CH₄) are introduced into a reaction chamber with carrier gases. |
Activation of Reactants | Precursors are activated via thermal energy, plasma, or catalysts to initiate reactions. |
Surface Reaction & Deposition | Activated precursors form SiC on the substrate, creating a continuous film. |
Removal of Byproducts | Volatile byproducts (e.g., H₂) are removed to prevent contamination and maintain film quality. |
Heat Transfer & Gas Flow | Optimized heat conduction and gas flow ensure uniform deposition across the substrate. |
Applications | Used in semiconductors, coatings, powders, fibers, and monolithic components for advanced materials. |
Discover how the CVD process can enhance your semiconductor production—contact our experts today!