Ball mills and planetary mills are both grinding devices used to reduce materials into fine powders, but they differ significantly in their design, operation, and applications. A ball mill is a cylindrical device that rotates around a horizontal axis, using the impact and attrition forces of grinding balls to break down materials. In contrast, a planetary mill features multiple grinding jars that rotate around their own axes while also revolving around a central axis, creating higher energy impacts for more efficient grinding. Planetary mills are more advanced, offering features like programmable controls, low noise, and customizable power options, making them suitable for high-precision tasks. Ball mills, on the other hand, are simpler and more cost-effective, often used for grinding materials like ores, ceramics, and paints.
Key Points Explained:
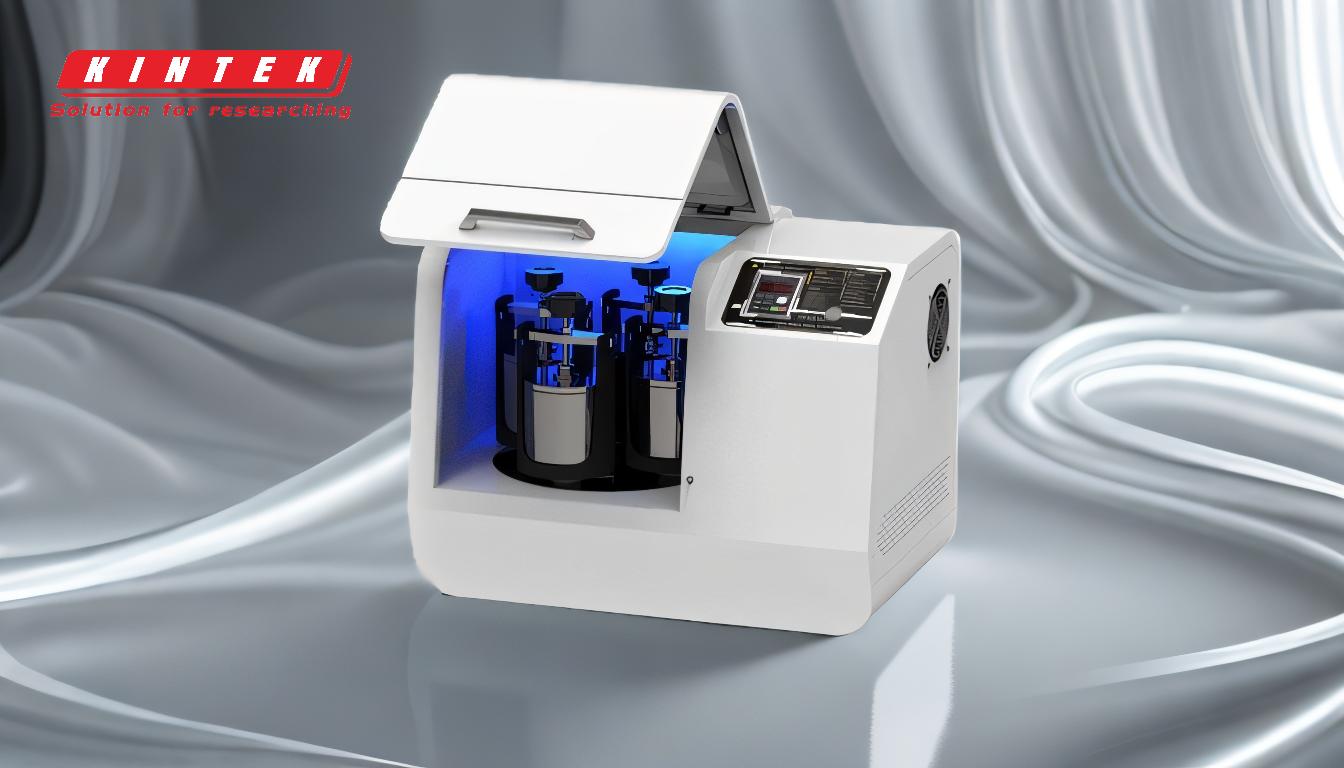
-
Design and Mechanism:
-
Ball Mill:
- Consists of a cylindrical container rotating around a horizontal axis.
- Uses grinding balls (often made of steel or ceramic) to crush and grind materials through impact and attrition.
- Operates at relatively lower speeds compared to planetary mills.
-
Planetary Mill:
- Features multiple grinding jars that rotate around their own axes while also revolving around a central axis.
- This dual rotation creates higher energy impacts, leading to more efficient grinding.
- Designed for higher precision and advanced applications.
-
Ball Mill:
-
Grinding Efficiency:
-
Ball Mill:
- Effective for grinding materials into fine powders but may require longer processing times.
- Suitable for medium to coarse grinding tasks.
-
Planetary Mill:
- Offers significantly higher grinding efficiency due to the dual rotation mechanism.
- Capable of producing ultra-fine powders in shorter time frames.
- Ideal for tasks requiring high precision and fine particle sizes.
-
Ball Mill:
-
Applications:
-
Ball Mill:
- Commonly used in industries like mining, ceramics, and paint production.
- Suitable for grinding materials such as ores, ceramics, and pigments.
-
Planetary Mill:
- Used in advanced applications like nanotechnology, pharmaceuticals, and materials science.
- Preferred for tasks requiring high-energy grinding and fine particle sizes.
-
Ball Mill:
-
Operational Features:
-
Ball Mill:
- Simpler design with fewer moving parts.
- Generally more cost-effective and easier to maintain.
-
Planetary Mill:
- Equipped with advanced features like programmable controls, LCD panels, and safety mechanisms.
- Offers customizable power supply options (110V, 220V, or 380V) and low-noise operation.
- Designed for stable rotation speeds and reliable performance in heavy-duty applications.
-
Ball Mill:
-
Energy and Noise Levels:
-
Ball Mill:
- Typically operates at lower energy levels, resulting in less noise and vibration.
- Suitable for environments where noise and vibration are not major concerns.
-
Planetary Mill:
- Designed with special gear mechanisms to minimize noise and vibration.
- More energy-intensive but offers higher grinding efficiency and precision.
-
Ball Mill:
-
Cost and Maintenance:
-
Ball Mill:
- Generally more affordable both in terms of initial investment and maintenance costs.
- Simpler design makes it easier to repair and maintain.
-
Planetary Mill:
- Higher initial cost due to advanced features and complex design.
- Requires more specialized maintenance but offers greater precision and efficiency.
-
Ball Mill:
In summary, while both ball mills and planetary mills are used for grinding materials into fine powders, they cater to different needs and applications. Ball mills are simpler, more cost-effective, and suitable for medium to coarse grinding tasks, whereas planetary mills offer higher precision, efficiency, and advanced features, making them ideal for high-precision and high-energy grinding applications.
Summary Table:
Feature | Ball Mill | Planetary Mill |
---|---|---|
Design | Cylindrical container rotating horizontally; uses grinding balls for impact. | Multiple grinding jars rotating on own axes and around a central axis. |
Grinding Efficiency | Medium to coarse grinding; longer processing times. | High efficiency; ultra-fine powders in shorter time frames. |
Applications | Mining, ceramics, paint production. | Nanotechnology, pharmaceuticals, materials science. |
Operational Features | Simpler design; cost-effective; easier maintenance. | Advanced features like programmable controls, LCD panels, low-noise operation. |
Energy & Noise | Lower energy levels; less noise and vibration. | High energy; special gear mechanisms minimize noise and vibration. |
Cost & Maintenance | Affordable; easier to repair. | Higher initial cost; specialized maintenance for precision and efficiency. |
Need help choosing the right grinding solution? Contact our experts today for personalized advice!