Ball mills and attrition mills are both used for grinding materials, but they differ significantly in their mechanisms, applications, and operational characteristics. A ball mill uses rotating balls to grind materials into fine powders, relying on impact and attrition forces. It is commonly used for materials like ore, ceramics, and paint. In contrast, an attrition mill employs a more direct grinding mechanism, often using rotating discs or plates to create friction and shear forces, making it suitable for finer grinding and materials that require precise particle size reduction. Below, the key differences are explained in detail.
Key Points Explained:
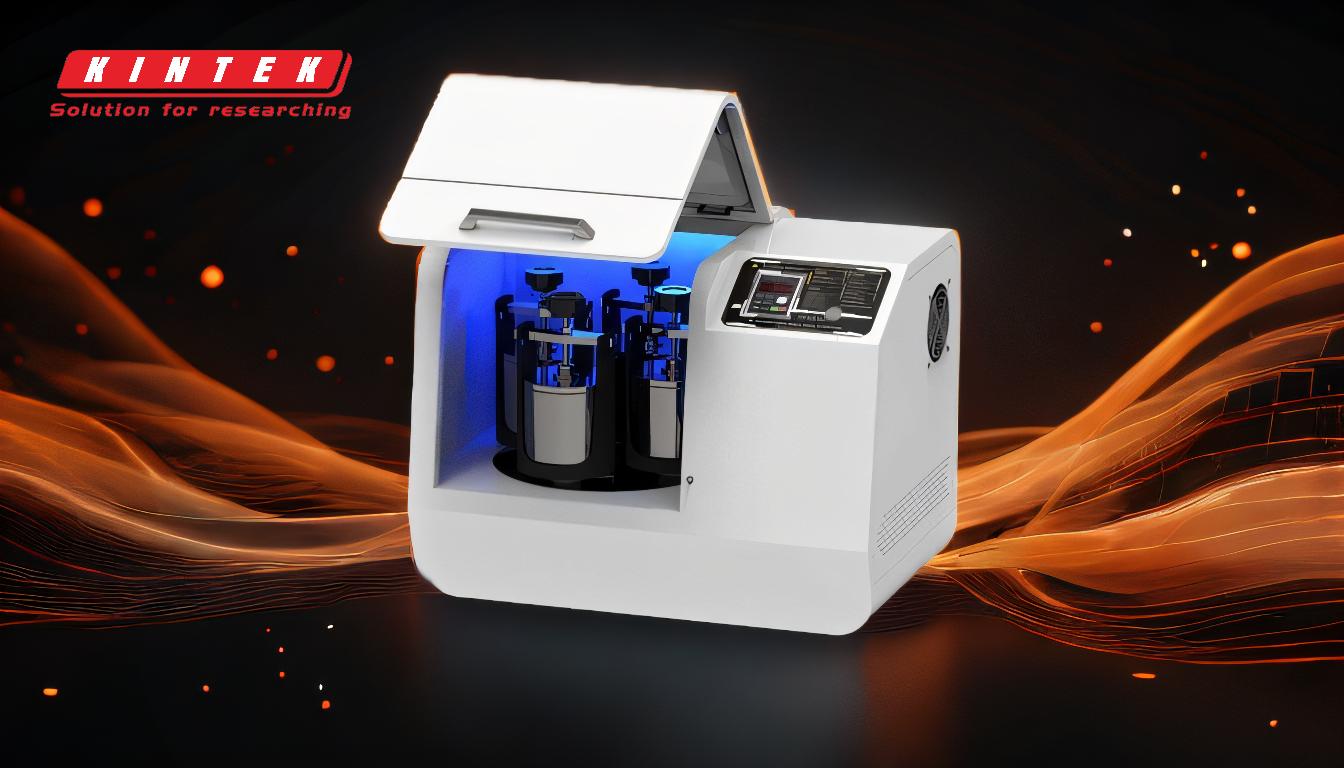
-
Mechanism of Grinding
-
Ball Mill:
- Uses rotating balls (usually made of steel or ceramic) to grind materials.
- The grinding action is a combination of impact (from the falling balls) and attrition (from the rubbing of balls against each other and the material).
- Suitable for coarse to medium-fine grinding.
-
Attrition Mill:
- Relies on rotating discs or plates to create friction and shear forces.
- The grinding action is more controlled and precise, focusing on attrition and shear rather than impact.
- Better suited for fine and ultra-fine grinding.
-
Ball Mill:
-
Design and Structure
-
Ball Mill:
- Typically consists of a cylindrical shell rotating around a horizontal axis.
- Contains grinding media (balls) that cascade and tumble within the shell.
- Often larger in size and requires more space.
-
Attrition Mill:
- Compact design with vertical or horizontal orientation.
- Features rotating discs or plates that grind the material between them.
- Generally smaller and more compact than ball mills.
-
Ball Mill:
-
Applications
-
Ball Mill:
- Ideal for grinding hard, brittle materials like ores, ceramics, and minerals.
- Commonly used in industries like mining, cement, and paint manufacturing.
-
Attrition Mill:
- Better suited for softer materials or those requiring finer particle sizes.
- Used in industries like food processing, pharmaceuticals, and chemical manufacturing.
-
Ball Mill:
-
Particle Size Control
-
Ball Mill:
- Produces a broader range of particle sizes, from coarse to fine.
- Less precise control over particle size distribution.
-
Attrition Mill:
- Offers more precise control over particle size, especially for fine and ultra-fine grinding.
- Produces a narrower and more consistent particle size distribution.
-
Ball Mill:
-
Energy Efficiency
-
Ball Mill:
- Generally consumes more energy due to the impact forces and the need to rotate a heavy cylindrical shell.
-
Attrition Mill:
- More energy-efficient for fine grinding, as it relies on friction and shear forces, which require less energy compared to impact grinding.
-
Ball Mill:
-
Maintenance and Wear
-
Ball Mill:
- Higher wear and tear on grinding media (balls) and the mill lining due to impact forces.
- Requires frequent maintenance and replacement of grinding media.
-
Attrition Mill:
- Lower wear and tear due to the absence of high-impact forces.
- Easier to maintain and has a longer operational lifespan.
-
Ball Mill:
-
Operational Flexibility
-
Ball Mill:
- Can handle a wide range of materials and grinding requirements.
- Less sensitive to changes in material properties.
-
Attrition Mill:
- More specialized and better suited for specific grinding tasks, particularly fine and ultra-fine grinding.
- Sensitive to material properties like hardness and moisture content.
-
Ball Mill:
In summary, the choice between a ball mill and an attrition mill depends on the specific grinding requirements, material properties, and desired particle size. Ball mills are versatile and suitable for coarse to medium-fine grinding, while attrition mills excel in fine and ultra-fine grinding with better energy efficiency and particle size control.
Summary Table:
Feature | Ball Mill | Attrition Mill |
---|---|---|
Mechanism | Impact & attrition forces | Friction & shear forces |
Particle Size | Coarse to medium-fine | Fine to ultra-fine |
Applications | Ores, ceramics, paint | Food, pharmaceuticals, chemicals |
Energy Efficiency | Less efficient for fine grinding | More efficient for fine grinding |
Maintenance | Higher wear, frequent maintenance | Lower wear, longer lifespan |
Flexibility | Versatile, less material-sensitive | Specialized, material-sensitive |
Need help choosing the right mill for your application? Contact our experts today!