Ball mills and attritor mills are both used for grinding and mixing materials, but they differ significantly in their design, operation, and applications. A ball mill is a cylindrical device with horizontal or slightly inclined rotation, using grinding media like steel or ceramic balls to reduce particle size through impact and attrition. In contrast, an attritor mill is a high-energy, vertical grinding machine that uses smaller grinding media and relies on intense agitation to achieve finer particle sizes. While ball mills are better suited for large-scale, continuous operations, attritor mills excel in producing ultrafine particles and are often used for smaller batches or specialized applications. Both mills have unique advantages depending on the material properties and desired outcomes.
Key Points Explained:
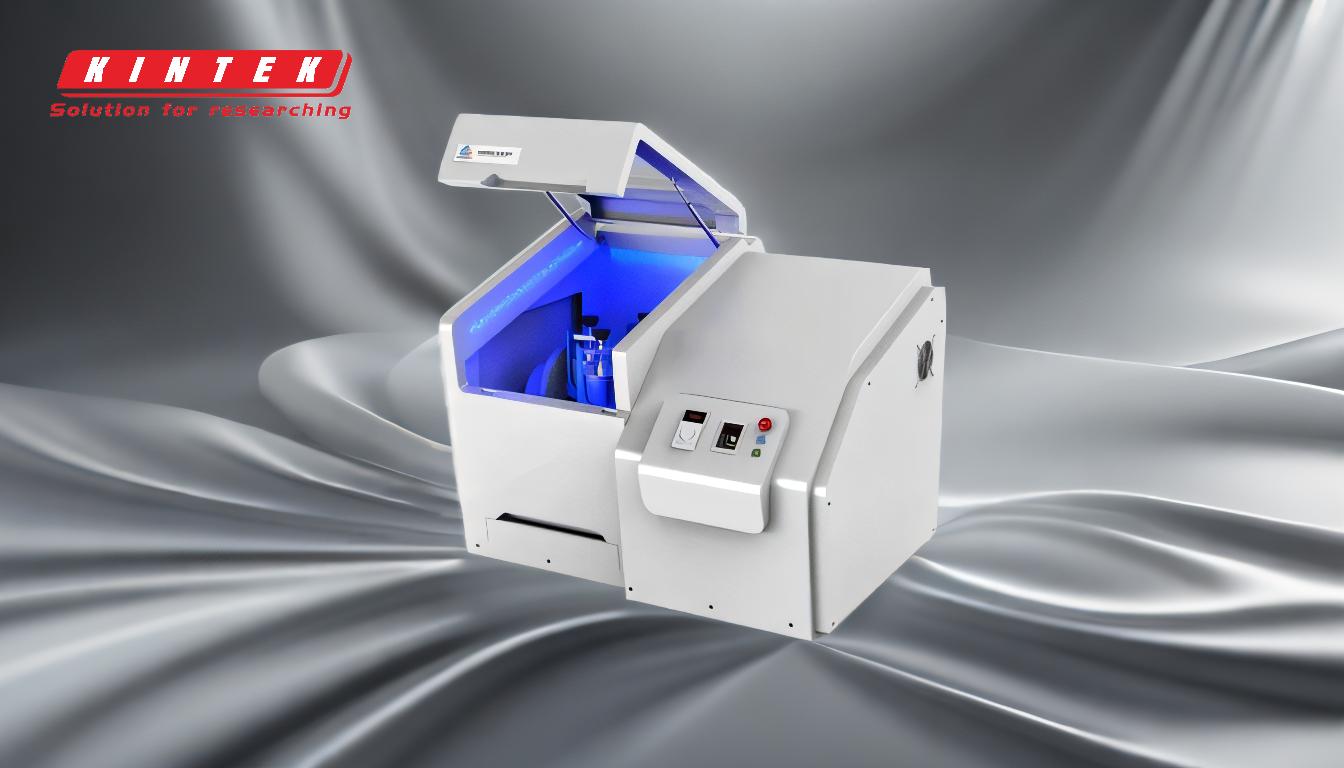
-
Design and Structure:
-
Ball Mill:
- Cylindrical in shape, typically horizontal or slightly inclined.
- Uses large grinding media (e.g., steel or ceramic balls) that tumble and impact the material.
- Operates at relatively low speeds, relying on gravity to move the grinding media.
-
Attritor Mill:
- Vertical design with a stationary tank and rotating agitator arms.
- Uses smaller grinding media (e.g., beads or balls) that are agitated at high speeds.
- Operates at higher energy levels due to the intense agitation of the media.
-
Ball Mill:
-
Grinding Mechanism:
-
Ball Mill:
- Relies on impact and attrition forces as the grinding media cascade and tumble within the rotating drum.
- Suitable for coarse to medium grinding, producing particles in the range of tens to hundreds of microns.
-
Attritor Mill:
- Utilizes high-energy agitation to create intense collisions between the grinding media and the material.
- Capable of producing ultrafine particles, often in the sub-micron range, due to the higher energy input.
-
Ball Mill:
-
Operational Efficiency:
-
Ball Mill:
- More energy-efficient for large-scale, continuous grinding operations.
- Requires less maintenance due to its simpler design and slower operating speeds.
-
Attritor Mill:
- More efficient for fine and ultrafine grinding, especially for materials that are difficult to grind.
- Higher energy consumption per unit of material processed, but achieves finer particle sizes in shorter times.
-
Ball Mill:
-
Applications:
-
Ball Mill:
- Commonly used in industries like mining, cement, and ceramics for large-scale grinding of ores, clinker, and raw materials.
- Suitable for both dry and wet grinding processes.
-
Attritor Mill:
- Preferred for applications requiring ultrafine particles, such as in pharmaceuticals, paints, and advanced materials.
- Often used for batch processing or when precise control over particle size distribution is needed.
-
Ball Mill:
-
Advantages and Limitations:
-
Ball Mill:
- Advantages: Simple design, low maintenance, and cost-effective for large-scale operations.
- Limitations: Limited ability to produce ultrafine particles; may require longer grinding times for finer materials.
-
Attritor Mill:
- Advantages: High efficiency in producing ultrafine particles; suitable for heat-sensitive materials due to shorter processing times.
- Limitations: Higher energy consumption; more complex design and maintenance requirements.
-
Ball Mill:
-
Material Compatibility:
-
Ball Mill:
- Works well with a wide range of materials, including hard and abrasive substances.
- Less effective for materials that require very fine grinding or are prone to agglomeration.
-
Attritor Mill:
- Ideal for grinding soft, brittle, or heat-sensitive materials.
- Can handle materials that require uniform particle size distribution and minimal contamination.
-
Ball Mill:
In summary, the choice between a ball mill and an attritor mill depends on the specific requirements of the grinding process, including the desired particle size, material properties, and scale of operation. Ball mills are better suited for large-scale, coarse grinding, while attritor mills excel in producing ultrafine particles and are ideal for specialized applications.
Summary Table:
Feature | Ball Mill | Attritor Mill |
---|---|---|
Design | Cylindrical, horizontal/slightly inclined | Vertical, stationary tank with rotating agitator arms |
Grinding Media | Large steel/ceramic balls | Smaller beads/balls |
Grinding Mechanism | Impact and attrition forces | High-energy agitation |
Particle Size | Coarse to medium (tens to hundreds of microns) | Ultrafine (sub-micron range) |
Energy Efficiency | More efficient for large-scale operations | Higher energy consumption, but faster for fine grinding |
Applications | Mining, cement, ceramics (large-scale) | Pharmaceuticals, paints, advanced materials (small batches, ultrafine grinding) |
Advantages | Simple design, low maintenance, cost-effective | High efficiency for ultrafine particles, shorter processing times |
Limitations | Limited ultrafine grinding, longer grinding times | Higher energy use, complex design, and maintenance |
Need help choosing the right mill for your grinding process? Contact our experts today for personalized advice!