Hammer mills and cutter mills are both used for size reduction in various industries, but they differ significantly in their design, working principles, and applications. A hammer mill uses high-speed rotating hammers to impact and break down materials, making it ideal for coarse grinding and fibrous materials. In contrast, a cutter mill employs sharp blades or cutters to shear and slice materials, making it more suitable for fine grinding and brittle materials. The choice between the two depends on the material properties, desired particle size, and specific application requirements.
Key Points Explained:
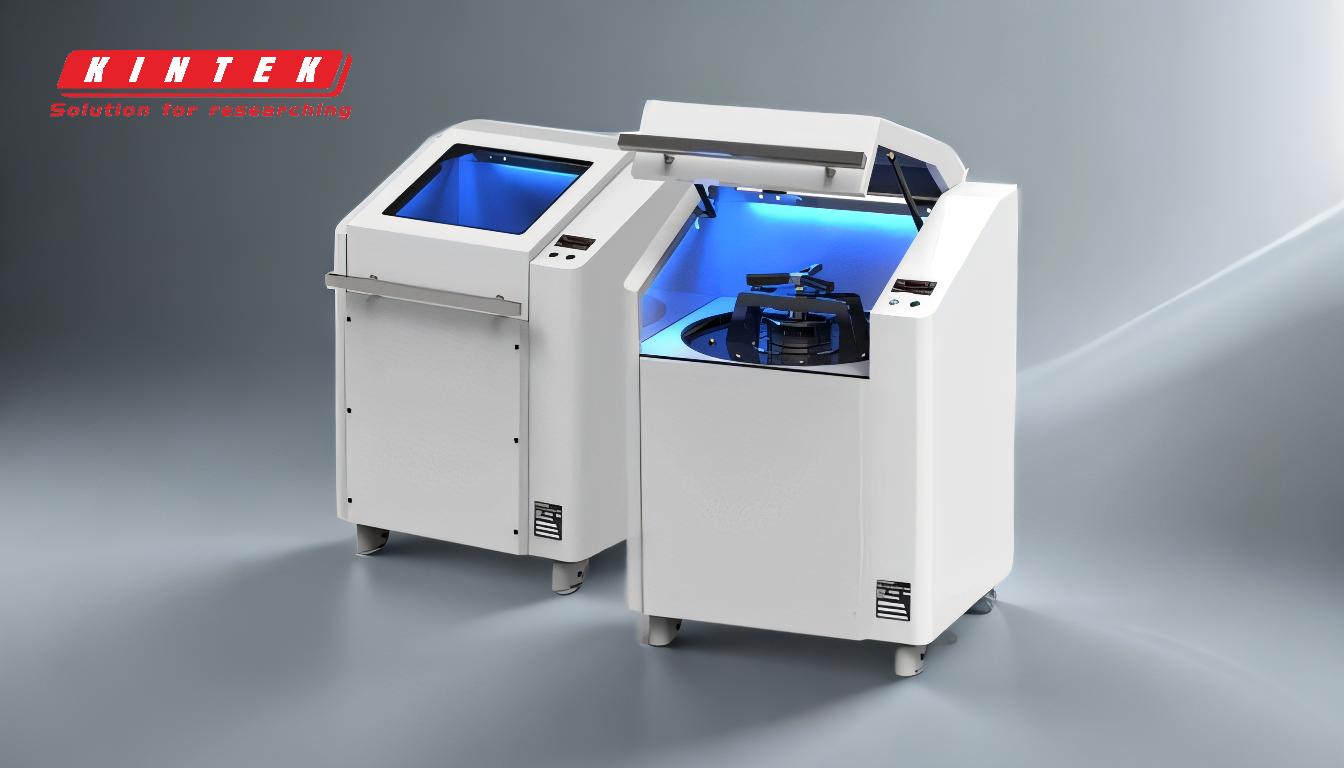
-
Design and Mechanism
-
Hammer Mill:
- Utilizes a series of hammers mounted on a rotating shaft.
- The hammers strike the material repeatedly until it is reduced to the desired size.
- Often includes a screen to control the final particle size.
-
Cutter Mill:
- Equipped with sharp blades or cutters that shear and slice the material.
- The blades rotate at high speeds, cutting the material into smaller pieces.
- Typically does not use a screen, relying on the cutting action for size reduction.
-
Hammer Mill:
-
Working Principle
-
Hammer Mill:
- Operates on the principle of impact and attrition.
- High-speed hammers collide with the material, breaking it down through repeated impacts.
- Suitable for materials that are tough, fibrous, or require coarse grinding.
-
Cutter Mill:
- Works on the principle of shearing and slicing.
- Sharp blades cut the material into smaller pieces, resulting in a finer grind.
- Ideal for brittle or soft materials that can be easily sliced.
-
Hammer Mill:
-
Applications
-
Hammer Mill:
- Commonly used in industries like agriculture, food processing, and recycling.
- Effective for grinding grains, wood chips, and other fibrous materials.
-
Cutter Mill:
- Often used in pharmaceuticals, chemicals, and food industries.
- Suitable for grinding brittle materials like spices, herbs, and certain chemicals.
-
Hammer Mill:
-
Particle Size and Output
-
Hammer Mill:
- Produces a wide range of particle sizes, from coarse to medium.
- The final particle size can be adjusted by changing the screen size.
-
Cutter Mill:
- Typically produces finer and more uniform particles.
- The particle size is controlled by the speed of the blades and the gap between them.
-
Hammer Mill:
-
Material Compatibility
-
Hammer Mill:
- Better suited for tough, fibrous, or hard materials.
- Can handle materials with high moisture content.
-
Cutter Mill:
- More effective for brittle, soft, or easily sliceable materials.
- May struggle with fibrous or tough materials.
-
Hammer Mill:
-
Maintenance and Wear
-
Hammer Mill:
- Hammers and screens are subject to wear and may require frequent replacement.
- Regular maintenance is needed to ensure optimal performance.
-
Cutter Mill:
- Blades may need sharpening or replacement over time.
- Generally requires less maintenance compared to hammer mills.
-
Hammer Mill:
-
Energy Efficiency
-
Hammer Mill:
- Can be less energy-efficient due to the high-speed impact mechanism.
- Energy consumption increases with tougher materials.
-
Cutter Mill:
- More energy-efficient for fine grinding of brittle materials.
- Lower energy consumption for materials that are easily sliced.
-
Hammer Mill:
-
Noise and Vibration
-
Hammer Mill:
- Tends to produce more noise and vibration due to the impact mechanism.
- May require additional noise-dampening measures.
-
Cutter Mill:
- Generally quieter and produces less vibration.
- More suitable for environments where noise is a concern.
-
Hammer Mill:
By understanding these key differences, you can make an informed decision on whether a hammer mill or a cutter mill is more suitable for your specific application.
Summary Table:
Feature | Hammer Mill | Cutter Mill |
---|---|---|
Design | Uses high-speed rotating hammers for impact grinding. | Employs sharp blades for shearing and slicing. |
Working Principle | Operates on impact and attrition; suitable for tough, fibrous materials. | Works on shearing and slicing; ideal for brittle, soft materials. |
Applications | Agriculture, food processing, recycling (e.g., grains, wood chips). | Pharmaceuticals, chemicals, food industries (e.g., spices, herbs). |
Particle Size | Coarse to medium; adjustable via screen size. | Finer, more uniform particles; controlled by blade speed and gap. |
Material Compatibility | Tough, fibrous, or hard materials; handles high moisture content. | Brittle, soft, or easily sliceable materials; struggles with fibrous materials. |
Maintenance | Frequent replacement of hammers and screens; regular maintenance required. | Blades may need sharpening; generally lower maintenance. |
Energy Efficiency | Less efficient for tough materials; higher energy consumption. | More efficient for fine grinding of brittle materials. |
Noise and Vibration | Produces more noise and vibration; may require noise-dampening measures. | Quieter and produces less vibration; suitable for noise-sensitive environments. |
Still unsure which mill is right for your needs? Contact our experts today for personalized advice!