Wet pumps and dry pumps are two distinct types of vacuum pumps, differing primarily in their use of lubrication and sealing mechanisms. Wet pumps rely on fluids like oil or water for lubrication and sealing, which can introduce contamination and require regular maintenance. Dry pumps, on the other hand, operate without any fluid in the pumping chamber, relying on tight mechanical tolerances to function effectively. Dry pumps are cleaner, require less maintenance, and are suitable for applications where contamination must be minimized. However, they tend to have a higher initial cost compared to wet pumps. The choice between the two depends on the specific application, budget, and maintenance considerations.
Key Points Explained:
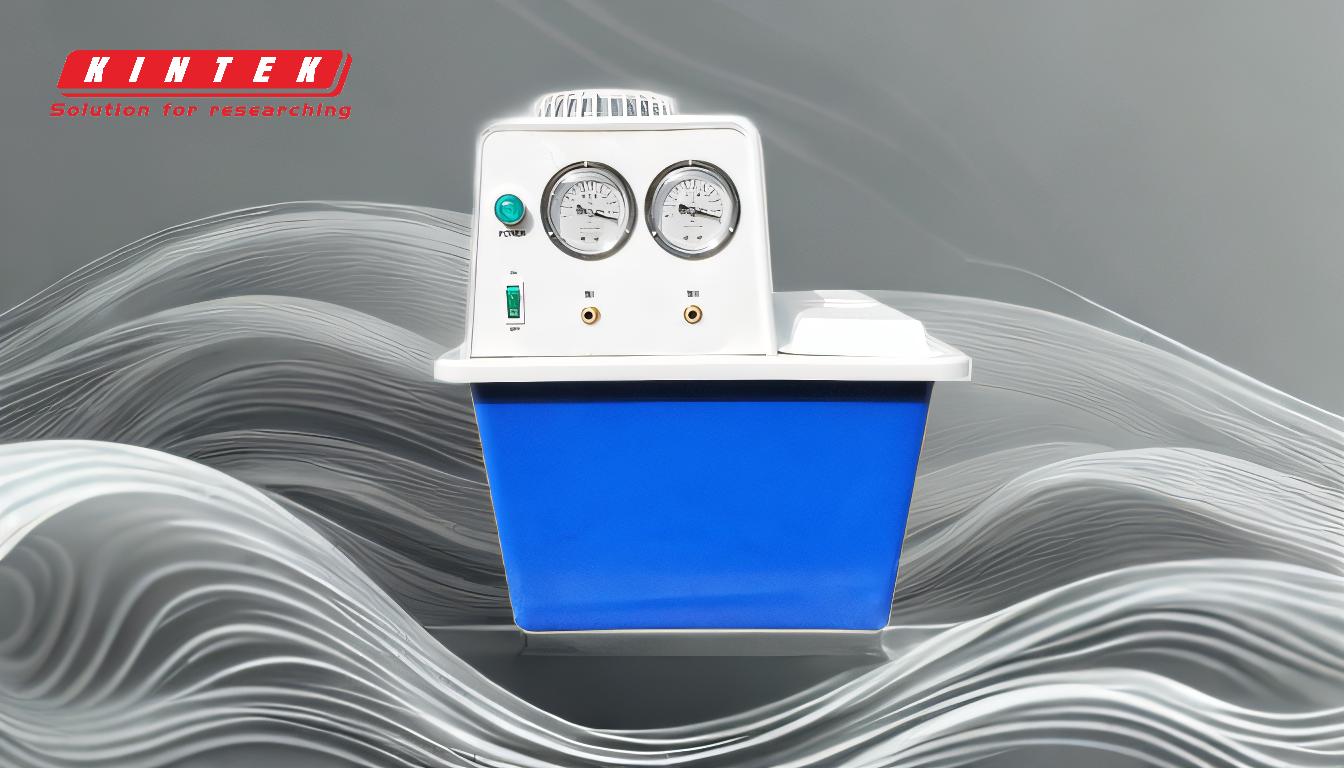
-
Lubrication and Sealing Mechanisms:
- Wet Pumps: These pumps use fluids such as oil or water for lubrication and sealing. The fluid reduces friction between moving parts and helps maintain a vacuum seal. However, this introduces the risk of contamination, especially in sensitive applications like semiconductor manufacturing or food processing.
- Dry Pumps: Dry pumps do not use any fluid in the pumping chamber. Instead, they rely on precise mechanical tolerances between components to minimize friction and maintain a vacuum seal. This design eliminates the risk of contamination from lubricants.
-
Maintenance Requirements:
- Wet Pumps: Require regular maintenance to replace or replenish the lubricating fluid, which can degrade over time. Additionally, the fluid can trap contaminants, necessitating periodic cleaning or replacement of components.
- Dry Pumps: Have minimal maintenance needs since there is no fluid to degrade or contaminate. This makes them ideal for applications where downtime must be minimized.
-
Contamination and Cleanliness:
- Wet Pumps: The presence of oil or water can lead to contamination of the vacuum environment, making them unsuitable for cleanroom applications or processes that require a pristine vacuum.
- Dry Pumps: Provide a clean vacuum environment, free from fluid contamination. This makes them suitable for industries like pharmaceuticals, electronics, and research laboratories.
-
Initial Cost and Long-Term Value:
- Wet Pumps: Generally have a lower initial cost, making them an attractive option for budget-conscious buyers. However, the ongoing maintenance and potential for contamination can increase long-term costs.
- Dry Pumps: Have a higher upfront cost due to their precision engineering and advanced materials. However, their lower maintenance requirements and clean operation can result in cost savings over time.
-
Common Types of Pumps:
- Wet Pumps: Include rotary vane pumps, liquid ring pumps, and oil-sealed pumps. These are widely used in industrial applications where contamination is not a critical concern.
- Dry Pumps: Include diaphragm pumps, piston pumps, scroll pumps, and turbomolecular pumps. These are preferred in high-tech industries and applications requiring a clean vacuum.
-
Application Suitability:
- Wet Pumps: Best suited for applications where contamination is not a concern, such as general industrial processes, HVAC systems, and automotive applications.
- Dry Pumps: Ideal for sensitive applications like semiconductor manufacturing, analytical instrumentation, and food processing, where contamination must be avoided.
By understanding these key differences, purchasers can make informed decisions based on their specific needs, balancing factors like cost, maintenance, and application requirements.
Summary Table:
Feature | Wet Pumps | Dry Pumps |
---|---|---|
Lubrication | Use oil or water for lubrication and sealing. | Operate without fluids, relying on precise mechanical tolerances. |
Maintenance | Require regular fluid replacement and cleaning. | Minimal maintenance due to no fluid use. |
Contamination Risk | Higher risk of contamination from lubricants. | No contamination risk, ideal for cleanroom applications. |
Initial Cost | Lower upfront cost. | Higher upfront cost due to precision engineering. |
Long-Term Value | Higher maintenance costs over time. | Lower maintenance costs and long-term savings. |
Common Types | Rotary vane, liquid ring, oil-sealed pumps. | Diaphragm, piston, scroll, turbomolecular pumps. |
Applications | General industrial, HVAC, automotive. | Semiconductor, pharmaceuticals, food processing, research labs. |
Need help choosing the right vacuum pump for your application? Contact our experts today for personalized advice!