RF and DC sputtering are two widely used physical vapor deposition (PVD) techniques, differing primarily in their power sources and applications. RF sputtering uses an alternating current (AC) power source, typically at 13.56 MHz, which prevents charge buildup on insulating targets, making it suitable for both conductive and non-conductive materials. In contrast, DC sputtering uses a direct current (DC) power source, making it ideal for conductive materials like pure metals due to its high deposition rates and cost-efficiency. While DC sputtering is limited by charge accumulation and arcing when used with dielectric materials, RF sputtering overcomes these limitations, albeit at a higher cost and lower deposition rate. Both methods involve directing a noble gas plasma at a substrate to deposit a thin film, but RF sputtering's alternating voltage enables more versatile material compatibility.
Key Points Explained:
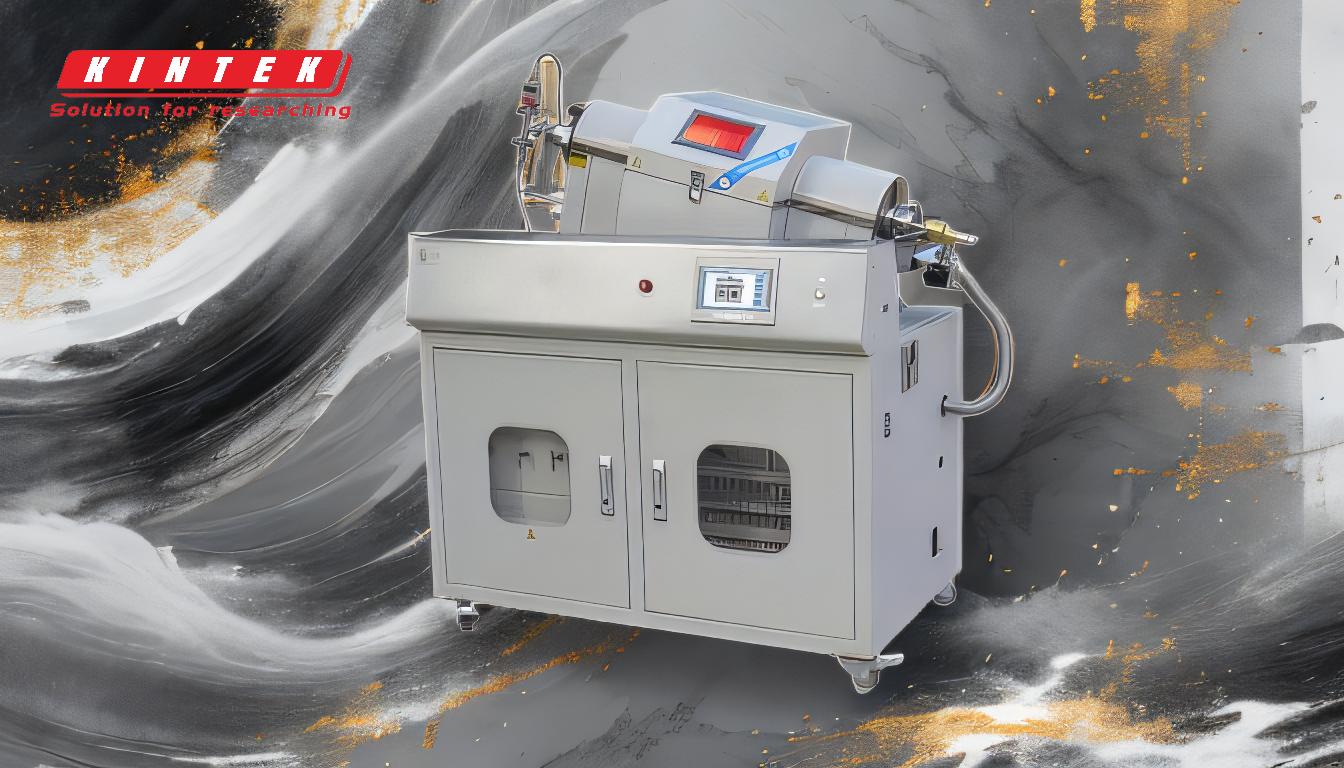
-
Power Source Differences:
- DC Sputtering: Uses a direct current (DC) power source, which accelerates positively charged gas ions toward the target material. This method is efficient for conductive materials like metals (e.g., Iron, Copper, Nickel) but struggles with insulating materials due to charge accumulation and arcing.
- RF Sputtering: Utilizes an alternating current (AC) power source, typically at 13.56 MHz. The alternating voltage prevents charge buildup on the target surface, making it suitable for both conductive and non-conductive (dielectric) materials.
-
Material Compatibility:
- DC Sputtering: Best suited for conductive materials. It cannot effectively sputter insulating materials due to charge accumulation, which can damage the power supply and cause arcing.
- RF Sputtering: Capable of sputtering both conductive and non-conductive materials. The alternating polarity neutralizes positive ions on the target surface, preventing surface charging and enabling the deposition of dielectric materials.
-
Deposition Rates and Costs:
- DC Sputtering: Offers high deposition rates, making it cost-effective for large substrates and industrial applications. It is generally less expensive to operate compared to RF sputtering.
- RF Sputtering: Has a lower deposition rate and higher operational costs due to the complexity of the AC power source and the need for specialized equipment. It is typically used for smaller substrates or applications requiring dielectric materials.
-
Process Mechanism:
- DC Sputtering: Involves a straightforward process where positively charged gas ions are accelerated toward the target material, physically knocking out atoms (adatoms) that are then deposited onto the substrate.
- RF Sputtering: Operates in a two-cycle process. In the first half-cycle, electrons neutralize positive ions on the target surface, preventing charge buildup. In the second half-cycle, target atoms are sputtered and deposited onto the substrate.
-
Applications:
- DC Sputtering: Commonly used in applications requiring high deposition rates and cost-efficiency, such as coating large metal surfaces or producing conductive thin films.
- RF Sputtering: Preferred for applications involving dielectric materials, such as insulating coatings, optical films, and semiconductor devices. It is also used when precise control over film properties is required.
-
Operational Challenges:
- DC Sputtering: Faces challenges with insulating materials due to charge accumulation, which can lead to arcing and damage the power supply. Pulsed DC sputtering is sometimes used to mitigate these issues.
- RF Sputtering: While it overcomes the limitations of DC sputtering with insulating materials, it is more complex and expensive to operate, making it less suitable for high-throughput industrial applications.
In summary, the choice between RF and DC sputtering depends on the specific requirements of the application, including the type of material to be deposited, the desired deposition rate, and budget constraints. DC sputtering is ideal for conductive materials and high-throughput applications, while RF sputtering is better suited for dielectric materials and applications requiring precise film properties.
Summary Table:
Aspect | DC Sputtering | RF Sputtering |
---|---|---|
Power Source | Direct Current (DC) | Alternating Current (AC) at 13.56 MHz |
Material Compatibility | Best for conductive materials (e.g., metals) | Suitable for both conductive and non-conductive (dielectric) materials |
Deposition Rate | High deposition rates, cost-effective for large substrates | Lower deposition rates, higher costs |
Applications | Ideal for conductive thin films and high-throughput industrial applications | Preferred for dielectric materials, optical films, and semiconductor devices |
Operational Challenges | Charge accumulation and arcing with insulating materials | Higher complexity and cost, less suitable for high-throughput applications |
Need help choosing the right sputtering method for your application? Contact our experts today!