The difference between single-stage and two-stage vacuum pumps lies primarily in their design, performance, and applications. Single-stage pumps have one compression stage, making them simpler and more cost-effective but less efficient at achieving high vacuum levels. Two-stage pumps, on the other hand, feature two compression stages, allowing them to achieve deeper vacuums and handle higher workloads, making them suitable for more demanding applications. Both types are used in various industries, but the choice depends on the required vacuum level, operational efficiency, and specific use cases.
Key Points Explained:
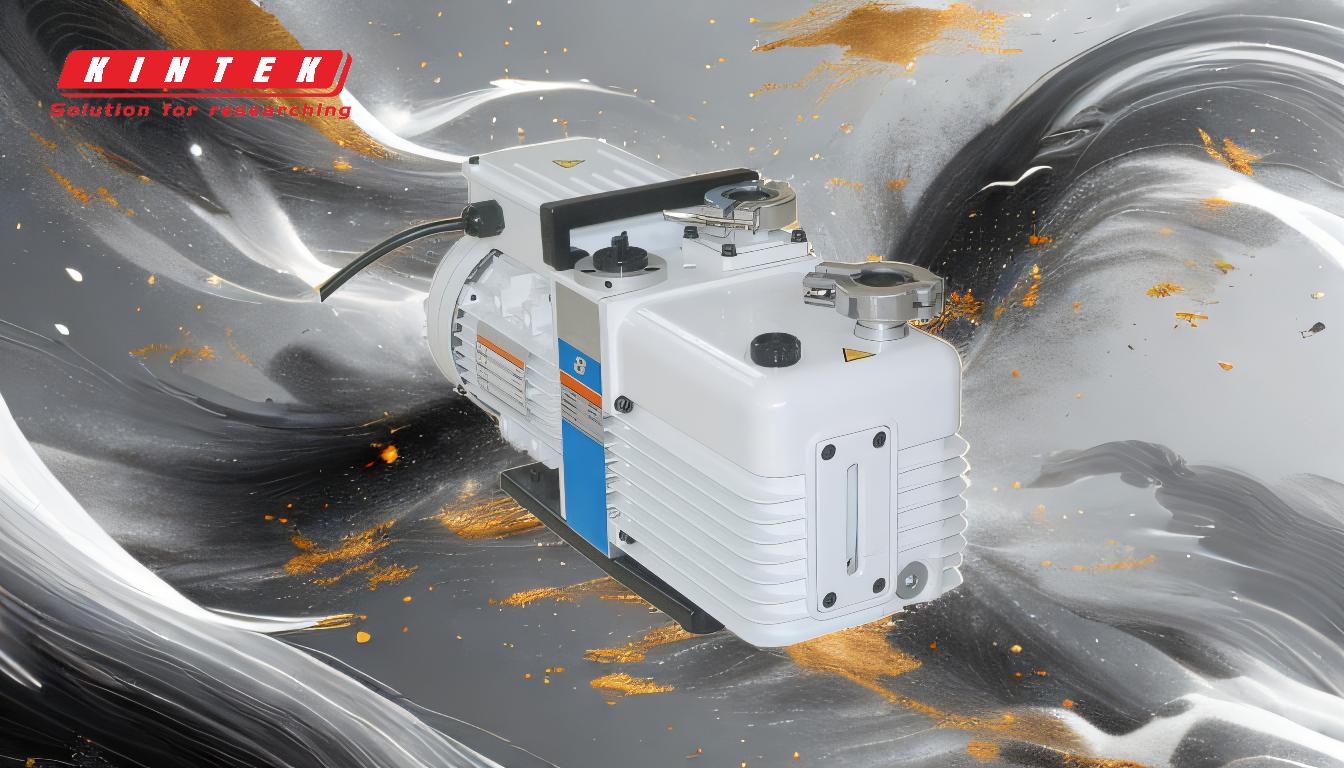
-
Design and Mechanism:
- Single-Stage Pumps: These pumps have a single compression stage, where air or gas is compressed once before being expelled. This design is simpler and less expensive to manufacture.
- Two-Stage Pumps: These pumps feature two compression stages. The gas is compressed in the first stage and then further compressed in the second stage, allowing for a deeper vacuum. This design is more complex but offers better performance.
-
Vacuum Level:
- Single-Stage Pumps: Typically achieve a vacuum level of around 10^-2 to 10^-3 Torr. They are suitable for applications where a moderate vacuum is sufficient.
- Two-Stage Pumps: Can achieve a vacuum level of 10^-4 Torr or lower. They are ideal for applications requiring a deeper vacuum.
-
Efficiency and Performance:
- Single-Stage Pumps: Generally less efficient in terms of energy consumption and vacuum depth. They are suitable for less demanding applications.
- Two-Stage Pumps: More efficient, especially in achieving higher vacuum levels and handling larger volumes of gas. They are better suited for high-performance applications.
-
Applications:
- Single-Stage Pumps: Commonly used in applications like vacuum packaging, degassing, and simple laboratory tasks where a high vacuum is not required.
- Two-Stage Pumps: Used in more demanding applications such as vacuum furnaces, high-vacuum systems, and processes requiring a consistent and deep vacuum.
-
Cost and Maintenance:
- Single-Stage Pumps: Generally cheaper to purchase and maintain due to their simpler design.
- Two-Stage Pumps: More expensive initially and may require more maintenance due to their complex design, but they offer better long-term performance and efficiency.
-
Operational Considerations:
- Single-Stage Pumps: Easier to operate and maintain, making them a good choice for routine tasks.
- Two-Stage Pumps: Require more careful operation and maintenance but provide superior performance for critical applications.
In summary, the choice between single-stage and two-stage vacuum pumps depends on the specific requirements of the application, including the desired vacuum level, operational efficiency, and budget constraints. Single-stage pumps are suitable for simpler tasks, while two-stage pumps are better for more demanding applications requiring deeper vacuums and higher performance.
Summary Table:
Aspect | Single-Stage Pumps | Two-Stage Pumps |
---|---|---|
Design | Single compression stage; simpler and cost-effective | Two compression stages; more complex but offers better performance |
Vacuum Level | 10^-2 to 10^-3 Torr; moderate vacuum | 10^-4 Torr or lower; deeper vacuum |
Efficiency | Less efficient; suitable for less demanding tasks | More efficient; ideal for high-performance applications |
Applications | Vacuum packaging, degassing, simple lab tasks | Vacuum furnaces, high-vacuum systems, critical processes |
Cost & Maintenance | Cheaper to purchase and maintain | More expensive initially; higher maintenance but better long-term performance |
Operational Ease | Easier to operate and maintain | Requires careful operation and maintenance |
Need help choosing the right vacuum pump for your application? Contact our experts today for personalized advice!