The difference between VAR (Vacuum Arc Remelting) and ESR (Electroslag Remelting) lies in their processes, applications, and the quality of the final product. VAR is a refining process used primarily for high-performance alloys, where the metal is melted in a vacuum to remove impurities and gases. ESR, on the other hand, uses a molten slag layer to refine the metal, improving its purity and homogeneity. Both methods are used to produce high-quality metals, but VAR is often preferred for critical aerospace and medical applications due to its ability to produce ultra-clean metals with minimal inclusions. ESR is more cost-effective and widely used for industrial applications requiring good mechanical properties.
Key Points Explained:
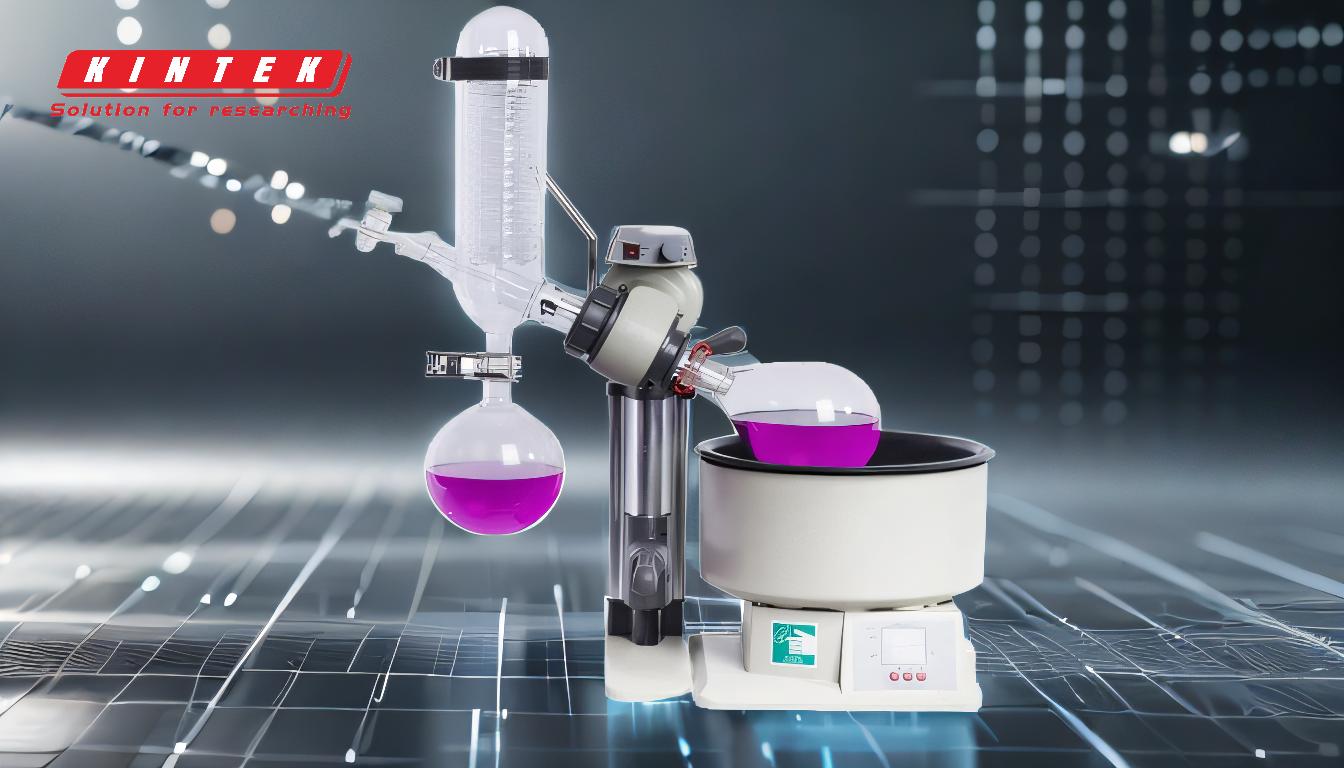
-
Process Differences:
-
VAR (Vacuum Arc Remelting):
- Involves melting the metal in a vacuum environment, which eliminates gases like hydrogen and oxygen.
- Uses an electric arc to melt the electrode, which then solidifies in a water-cooled mold.
- Ideal for producing ultra-high-purity metals with minimal inclusions.
-
ESR (Electroslag Remelting):
- Uses a molten slag layer (often calcium fluoride-based) to refine the metal.
- The electrode is melted by electrical resistance heating through the slag, which acts as a filter to remove impurities.
- Produces a refined metal with improved homogeneity and reduced segregation.
-
VAR (Vacuum Arc Remelting):
-
Applications:
-
VAR:
- Commonly used for aerospace, medical, and nuclear industries where material purity and performance are critical.
- Suitable for superalloys, titanium alloys, and other high-performance materials.
-
ESR:
- Widely used in industrial applications such as tool steels, stainless steels, and other alloys requiring good mechanical properties.
- More cost-effective for large-scale production compared to VAR.
-
VAR:
-
Quality of Final Product:
-
VAR:
- Produces metals with extremely low levels of impurities and gases, making them suitable for high-stress environments.
- Results in a finer grain structure and improved mechanical properties.
-
ESR:
- Provides a refined metal with reduced segregation and improved surface quality.
- While not as pure as VAR-processed metals, ESR metals are still of high quality and suitable for many demanding applications.
-
VAR:
-
Equipment and Operational Costs:
-
VAR:
- Requires a vacuum chamber and sophisticated control systems, making it more expensive to operate.
- Higher energy consumption due to the vacuum environment.
-
ESR:
- Less complex equipment and no need for a vacuum, resulting in lower operational costs.
- More energy-efficient compared to VAR.
-
VAR:
-
Environmental and Safety Considerations:
-
VAR:
- The vacuum environment reduces the risk of contamination and gas absorption, but the process requires careful handling of high voltages and temperatures.
-
ESR:
- The use of molten slag requires proper handling to avoid environmental contamination, but the process is generally safer and easier to control.
-
VAR:
-
Electrochemical Cell:
- Both VAR and ESR processes involve electrochemical principles, especially in the way electrical energy is used to melt and refine the metal. In VAR, the electric arc generates heat, while in ESR, the electrical resistance of the slag generates heat. Understanding the role of the electrochemical cell in these processes can provide deeper insights into how energy is efficiently utilized to achieve the desired metal properties.
In summary, while both VAR and ESR are used to refine metals, they differ significantly in their processes, applications, and the quality of the final product. VAR is ideal for ultra-high-purity applications, whereas ESR offers a cost-effective solution for industrial-grade materials. The choice between the two depends on the specific requirements of the application and the desired properties of the metal.
Summary Table:
Aspect | VAR (Vacuum Arc Remelting) | ESR (Electroslag Remelting) |
---|---|---|
Process | Melts metal in a vacuum to remove impurities and gases. | Uses a molten slag layer to refine metal, improving purity and homogeneity. |
Applications | Aerospace, medical, and nuclear industries (ultra-high-purity metals). | Industrial applications like tool steels, stainless steels (cost-effective for large-scale use). |
Product Quality | Extremely low impurities, finer grain structure, improved mechanical properties. | Reduced segregation, improved surface quality, suitable for demanding applications. |
Cost | Higher operational costs due to vacuum chamber and sophisticated controls. | Lower operational costs, more energy-efficient. |
Environmental Impact | Reduced contamination risk, but requires careful handling of high voltages and temperatures. | Safer and easier to control, but requires proper slag handling to avoid contamination. |
Need help choosing between VAR and ESR for your application? Contact our experts today for personalized guidance!