Electron beam surface treatment is a sophisticated technology that utilizes a focused electron beam to modify the surface properties of materials. This process involves rapid heating of a thin surface layer, leading to localized changes such as hardening, annealing, tempering, texturing, and polishing. The high power-density of the electron beam creates significant temperature gradients, enabling self-quenching without the need for external coolants. Additionally, the technology can create microstructures like spike formations to enhance bonding and surface roughness. Electron beam surface treatment is widely used in various industries, including manufacturing, electronics, and food processing, due to its precision, efficiency, and environmental benefits.
Key Points Explained:
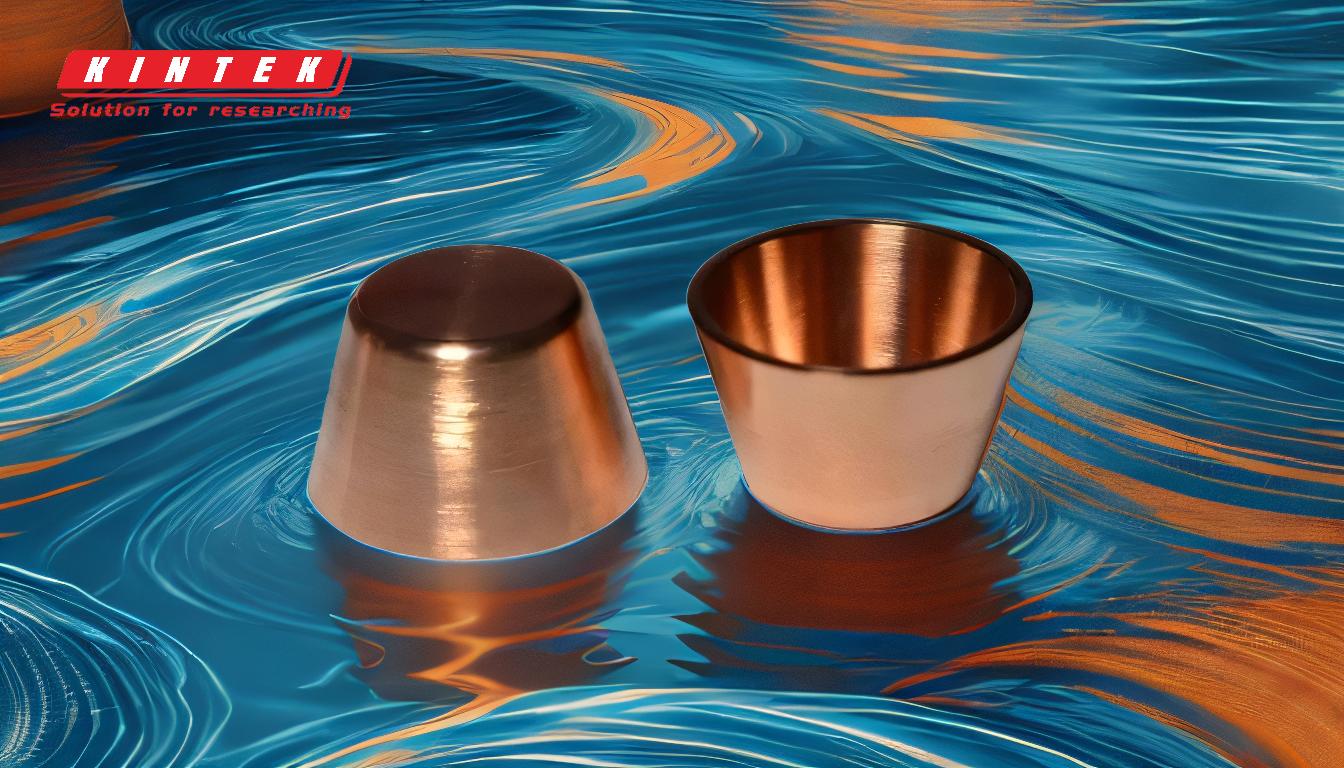
-
Principle of Electron Beam Surface Treatment:
- The electron beam heats the material's surface to temperatures above the austenitic range.
- Heat conduction into the cooler surrounding material causes rapid cooling (self-quenching).
- No external coolant is required due to the high power-density of the beam, which creates steep temperature gradients.
-
Types of Surface Treatments:
- Hardening: Increases surface hardness by rapid heating and cooling.
- Annealing: Reduces internal stresses and improves ductility.
- Tempering: Enhances toughness by controlled heating and cooling.
- Texturing and Polishing: Modifies surface roughness and creates microstructures for improved bonding.
-
Applications of Electron Beam Surface Treatment:
- Industrial Coatings: Used for solid colors, low COF coatings, ESD and anti-skid flooring, and antimicrobial coatings.
- Material Modification: Enhances properties of metals, ceramics, and polymers through crosslinking and chain scissioning.
- Microstructure Creation: Forms spike structures to improve surface adhesion and roughness.
-
Advantages of Electron Beam Processing:
- Precision: Targets only the surface layer, minimizing impact on the bulk material.
- Efficiency: Rapid processing reduces production time.
- Environmental Benefits: Eliminates the need for external coolants and reduces waste.
-
Electron Beam Deposition:
- A focused electron beam evaporates material from a crucible.
- The vapor condenses onto a substrate, forming a thin, uniform coating.
- Enhanced by ion beams for better adhesion and denser coatings.
-
Industrial and Commercial Uses:
- Manufacturing: Used in heat-shrinkable plastics, thermoset composite curing, and semiconductor enhancement.
- Food Processing: Ensures safety and extends shelf life through sterilization.
- Optical Coatings: Achieves precise thickness and conformal coatings for optical surfaces.
By leveraging the unique properties of electron beams, this technology offers a versatile and efficient solution for surface treatment across a wide range of applications, ensuring improved material performance and durability.
Summary Table:
Aspect | Details |
---|---|
Principle | Rapid heating and self-quenching via electron beam, no external coolants. |
Types of Treatments | Hardening, annealing, tempering, texturing, and polishing. |
Applications | Industrial coatings, material modification, microstructure creation. |
Advantages | Precision, efficiency, and environmental benefits. |
Industrial Uses | Manufacturing, food processing, optical coatings. |
Transform your material surfaces with electron beam technology—contact us today to learn more!