Electron beam thermal evaporation is a sophisticated thin-film deposition technique that utilizes a high-energy electron beam to evaporate a source material within a vacuum environment. This process is widely used in industries requiring precise and high-quality thin-film coatings, such as semiconductors, optics, and microelectronics. The method involves heating a target material using an electron beam generated by thermionic emission from a tungsten filament. The electrons are accelerated and focused onto the material, converting their kinetic energy into thermal energy, which causes the material to evaporate. The vaporized material then condenses onto a substrate, forming a thin film. This technique is particularly advantageous for materials with high melting points and offers excellent control over film thickness and purity.
Key Points Explained:
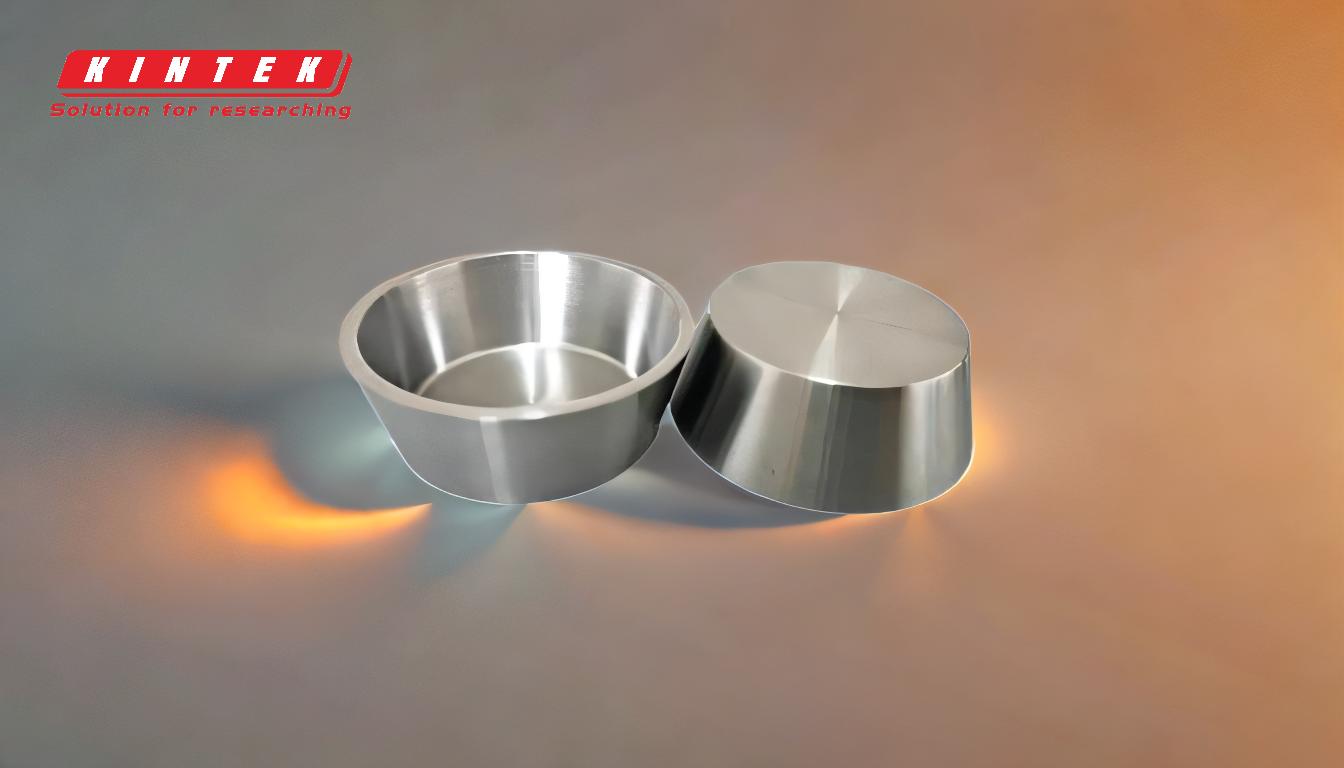
-
Fundamental Principle of Electron Beam Evaporation:
- Electron beam evaporation is a form of physical vapor deposition (PVD) that uses a high-energy electron beam to heat and evaporate a source material.
- The process occurs in a high-vacuum environment to minimize contamination and ensure high-purity thin films.
-
Components of the System:
- Electron Gun: Consists of a tungsten filament that emits electrons via thermionic emission when heated by an electric current.
- Acceleration and Focusing System: High voltage (5–15 kV) accelerates the electrons, and a magnetic field focuses them into a precise beam.
- Crucible: A water-cooled container that holds the target material to be evaporated.
- Substrate: The surface onto which the evaporated material condenses to form a thin film.
-
Process Mechanism:
- Electrons emitted from the filament are accelerated and directed toward the target material in the crucible.
- Upon impact, the kinetic energy of the electrons is converted into thermal energy, heating the material to its evaporation point.
- The vaporized material disperses in the vacuum chamber and deposits onto the substrate, forming a thin film.
-
Advantages of Electron Beam Evaporation:
- High Melting Point Capability: Suitable for evaporating materials with extremely high melting points, such as refractory metals and ceramics.
- High Purity: The vacuum environment minimizes contamination, resulting in high-purity films.
- Precise Control: Allows for accurate control over film thickness and uniformity.
- Line-of-Sight Deposition: Ideal for lift-off processes and applications requiring precise material placement.
-
Applications:
- Semiconductors: Used for depositing thin films in integrated circuits and semiconductor devices.
- Optics: Coating lenses, mirrors, and other optical components with high-performance films.
- Microelectronics: Fabricating thin-film resistors, capacitors, and other electronic components.
- Decorative Coatings: Applying durable and aesthetically pleasing coatings on consumer products.
-
Limitations:
- Limited Sidewall Coverage: Due to the line-of-sight nature of the process, it is challenging to achieve uniform coverage on complex geometries or sidewalls.
- High Equipment Cost: The need for a high-vacuum environment and specialized components makes the setup expensive.
- Material Constraints: While versatile, the process may not be suitable for all materials, particularly those sensitive to high-energy electron bombardment.
-
Reactive Deposition:
- Reactive gases such as oxygen or nitrogen can be introduced into the chamber to deposit non-metallic films, such as oxides or nitrides.
- This expands the range of materials that can be deposited and enhances the functional properties of the films.
-
Comparison with Other Deposition Techniques:
- Thermal Evaporation: Electron beam evaporation offers higher energy and temperature capabilities compared to traditional thermal evaporation.
- Sputtering: While sputtering provides better sidewall coverage, electron beam evaporation excels in high-purity and high-melting-point applications.
- Chemical Vapor Deposition (CVD): Unlike CVD, electron beam evaporation is a purely physical process, avoiding chemical reactions that could introduce impurities.
In summary, electron beam thermal evaporation is a highly effective and versatile thin-film deposition technique, particularly suited for applications requiring high purity, precise control, and the ability to handle materials with high melting points. Its limitations, such as limited sidewall coverage and high equipment costs, are often outweighed by its advantages in specialized industrial applications.
Summary Table:
Aspect | Details |
---|---|
Principle | Uses a high-energy electron beam to evaporate materials in a vacuum. |
Key Components | Electron gun, acceleration system, crucible, and substrate. |
Advantages | High melting point capability, high purity, precise control, line-of-sight. |
Applications | Semiconductors, optics, microelectronics, decorative coatings. |
Limitations | Limited sidewall coverage, high equipment cost, material constraints. |
Reactive Deposition | Allows deposition of oxides/nitrides by introducing reactive gases. |
Comparison with Others | Superior for high-purity and high-melting-point applications. |
Discover how electron beam thermal evaporation can elevate your thin-film processes—contact us today!