The filling stage in injection molding is the initial phase of the injection cycle, where molten material is injected into the mold cavity. This stage begins with the closing of the mold and concludes when the cavity is approximately 95% filled. The filling stage is critical as it determines the initial distribution of material within the mold, which impacts the quality and consistency of the final product. Proper control of parameters such as injection speed, pressure, and material temperature during this stage is essential to ensure complete filling, avoid defects, and achieve the desired product characteristics.
Key Points Explained:
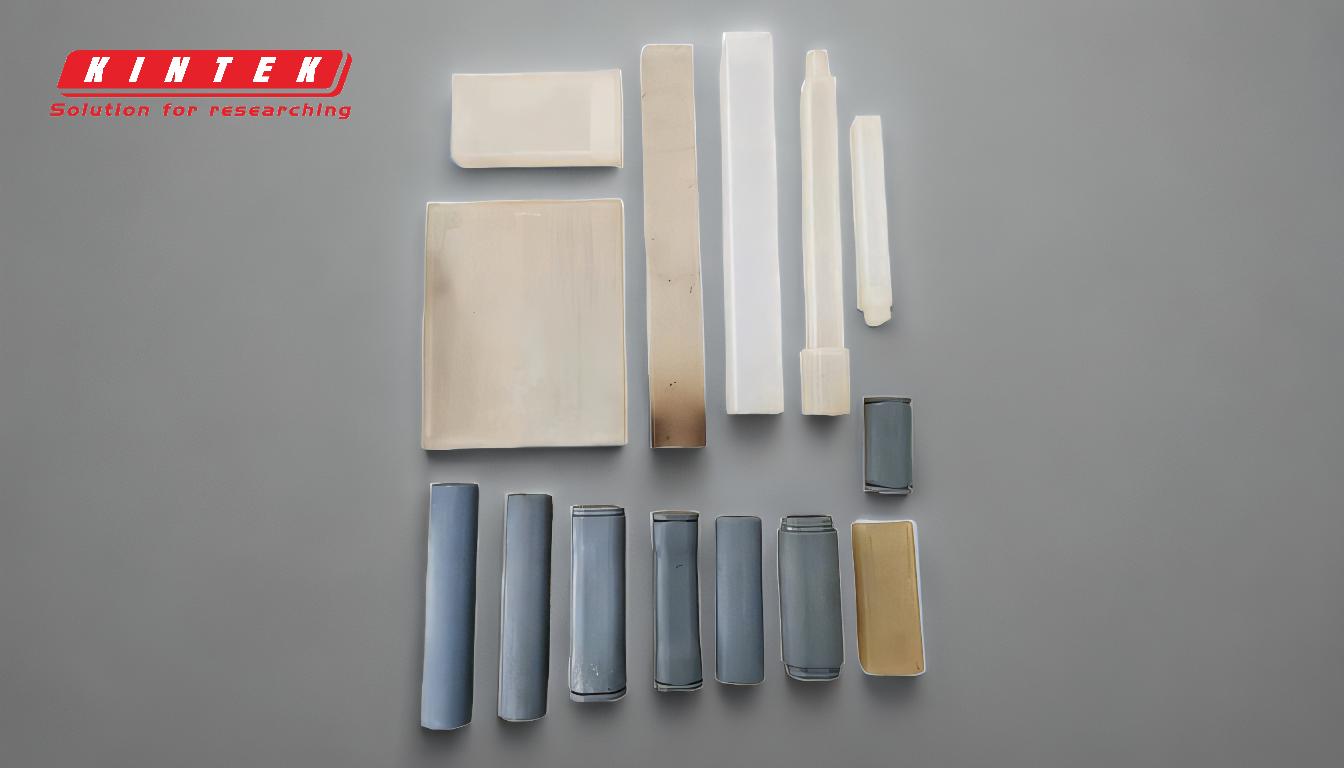
-
Definition and Purpose of the Filling Stage:
- The filling stage is the first step in the injection molding process, where molten material is injected into the mold cavity.
- Its primary purpose is to distribute the material evenly throughout the mold to form the basic shape of the product.
- This stage sets the foundation for the subsequent packing and cooling stages, which finalize the product's dimensions and properties.
-
Process Sequence:
- The filling stage begins with the mold closing securely to create a sealed cavity.
- Molten material is then injected into the cavity under controlled pressure and speed.
- The stage ends when the cavity is approximately 95% filled, leaving a small portion for the packing stage to complete.
-
Key Parameters:
- Injection Speed: Determines how quickly the material flows into the mold. Too fast can cause defects like air traps or burn marks, while too slow can lead to incomplete filling.
- Injection Pressure: Ensures the material is forced into all areas of the mold cavity. Proper pressure prevents short shots or uneven filling.
- Material Temperature: Affects the viscosity and flowability of the molten material. Optimal temperature ensures smooth filling and reduces the risk of defects.
-
Importance of Mold Design:
- The mold design, including gate location, runner system, and venting, plays a crucial role in the filling stage.
- Proper gate placement ensures even material distribution, while adequate venting prevents air traps and ensures complete filling.
-
Challenges and Defects:
- Common issues during the filling stage include short shots (incomplete filling), air traps, weld lines, and burn marks.
- These defects can arise from improper parameter settings, poor mold design, or material inconsistencies.
-
Transition to Packing Stage:
- The filling stage transitions seamlessly into the packing stage, where additional material is injected to compensate for shrinkage as the material cools.
- This ensures the final product has the correct dimensions and density.
By understanding and optimizing the filling stage, manufacturers can improve product quality, reduce defects, and enhance the efficiency of the injection molding process.
Summary Table:
Key Aspect | Details |
---|---|
Purpose | Distributes molten material evenly to form the product's basic shape. |
Process Sequence | Begins with mold closing, ends when cavity is ~95% filled. |
Key Parameters | Injection speed, pressure, and material temperature. |
Mold Design Importance | Gate location, runner system, and venting ensure complete filling. |
Common Defects | Short shots, air traps, weld lines, and burn marks. |
Transition to Packing | Ensures final product dimensions and density are achieved. |
Ready to optimize your injection molding process? Contact us today for expert guidance!