The two-plate mold is a fundamental and widely used design in injection molding. It consists of a single parting plane that splits the mold into two halves, typically referred to as the cavity side and the core side. This design allows for the efficient ejection of the molded part and the runner system when the mold opens. The simplicity and versatility of the two-plate mold make it suitable for a wide range of applications, especially in multi-cavity setups where the runner and gate systems are integrated into the parting plane. This ensures that both the molded parts and the runner system are ejected simultaneously during the mold opening process.
Key Points Explained:
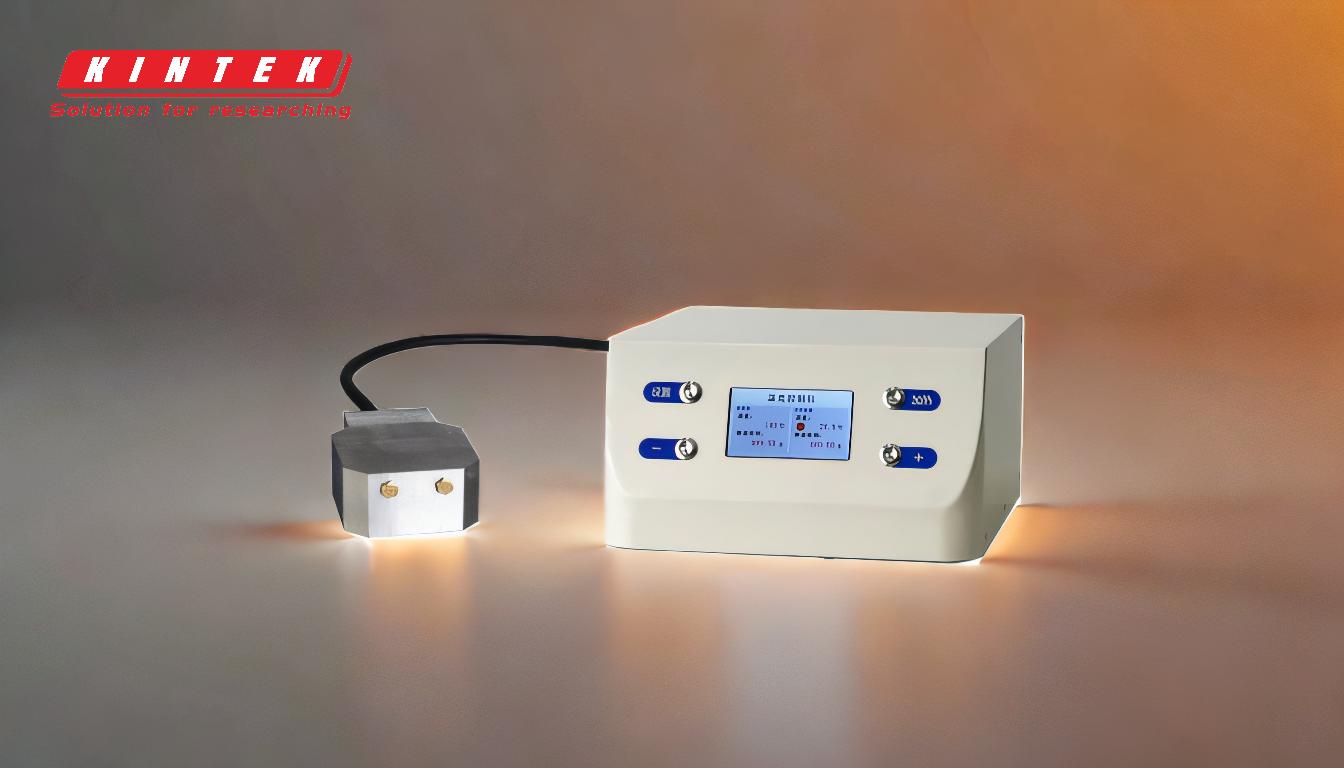
-
Basic Structure of a Two-Plate Mold:
- A two-plate mold consists of two main halves: the cavity side (stationary) and the core side (movable).
- These two halves meet at a single parting plane, which is the interface where the mold splits during the ejection process.
- The simplicity of this design makes it easy to manufacture, maintain, and operate.
-
Function of the Parting Plane:
- The parting plane is crucial for the mold's operation as it allows the mold to open and close smoothly.
- When the mold opens, the parting plane separates the cavity and core halves, enabling the ejection of the molded part and the runner system.
- In multi-cavity molds, the runner and gate systems are designed to lie within the parting plane, ensuring that they are ejected along with the parts.
-
Runner and Gate System:
- The runner is the channel through which molten plastic flows from the injection molding machine to the mold cavities.
- The gate is the entry point of the molten plastic into the mold cavity.
- In a two-plate mold, the runner and gate must be positioned in the parting plane to ensure that they are ejected when the mold opens. This is essential for the automatic operation of the mold and for preventing any obstruction in the molding process.
-
Ejection Mechanism:
- The ejection of the molded part and the runner system is facilitated by ejector pins or plates located on the core side of the mold.
- When the mold opens, the ejector mechanism pushes the part and the runner system out of the mold, allowing for continuous production cycles.
- The design of the ejection system is critical to ensure that the parts are released without damage and that the runner system is fully cleared from the mold.
-
Advantages of Two-Plate Molds:
- Simplicity: The straightforward design of two-plate molds makes them easy to manufacture and maintain.
- Cost-Effectiveness: Due to their simplicity, two-plate molds are generally more cost-effective compared to more complex mold designs.
- Versatility: They are suitable for a wide range of applications, from simple single-cavity molds to complex multi-cavity molds.
- Ease of Operation: The single parting plane and integrated runner and gate system make the operation of two-plate molds relatively easy, reducing the likelihood of errors during production.
-
Applications of Two-Plate Molds:
- Two-plate molds are commonly used in the production of a wide variety of plastic parts, including consumer goods, automotive components, and medical devices.
- They are particularly well-suited for high-volume production runs where efficiency and cost-effectiveness are critical.
- The ability to incorporate multiple cavities in a single mold makes them ideal for producing large quantities of identical parts.
-
Considerations for Design and Manufacturing:
- Material Selection: The choice of mold material is crucial to ensure durability and resistance to wear, especially in high-volume production.
- Cooling System Design: Efficient cooling is essential to maintain consistent part quality and cycle times. Proper design of cooling channels within the mold is necessary to achieve optimal cooling.
- Gate Design: The gate must be designed to allow smooth flow of molten plastic into the cavity while minimizing defects such as weld lines and air traps.
- Ejector System: The ejector system must be robust enough to handle the ejection of both the parts and the runner system without causing damage or deformation.
In summary, the two-plate mold is a versatile and cost-effective solution for injection molding, offering simplicity, ease of operation, and suitability for a wide range of applications. Its design ensures efficient ejection of both the molded parts and the runner system, making it an essential tool in the production of plastic components.
Summary Table:
Key Aspect | Details |
---|---|
Structure | Consists of two halves: cavity side (stationary) and core side (movable). |
Parting Plane | Enables smooth mold opening and ejection of parts and runner system. |
Runner & Gate System | Integrated into the parting plane for simultaneous ejection. |
Ejection Mechanism | Uses ejector pins/plates to push out parts and runners without damage. |
Advantages | Simple, cost-effective, versatile, and easy to operate. |
Applications | Used in consumer goods, automotive, medical devices, and high-volume runs. |
Design Considerations | Material selection, cooling system, gate design, and robust ejector system. |
Discover how two-plate molds can optimize your injection molding process—contact our experts today!